New Casting Technology: Advancements in 3D Printing for Investment Casting
By:Admin
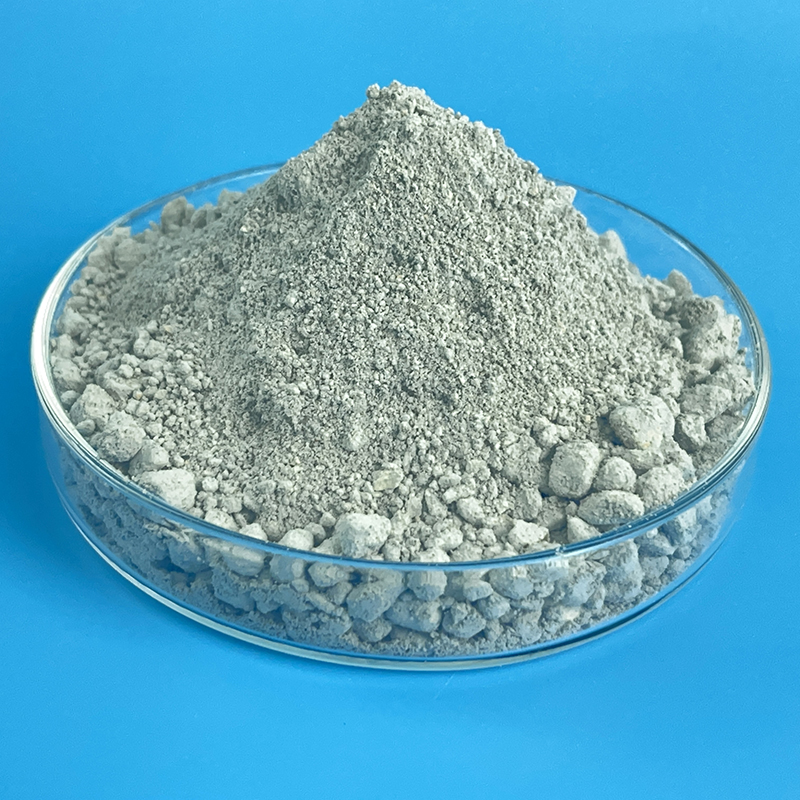
Mokey Castable Introduces Innovative Product to Revolutionize Casting Process
Mokey Castable, a leading provider of innovative solutions in the casting industry, has recently unveiled a groundbreaking new product that is set to revolutionize the casting process. With a relentless commitment to excellence and a focus on pushing the boundaries of what is possible, Mokey Castable has developed a product that promises to deliver exceptional results and streamline the casting process for manufacturers around the world.
Founded on the principle of innovation and driven by a passion for excellence, Mokey Castable has quickly established itself as a trusted provider of cutting-edge solutions for the casting industry. The company's team of experts is comprised of some of the most talented and experienced professionals in the field, all dedicated to developing and delivering products that address the unique challenges and needs of their clients.
The new product, which has been kept under wraps until now, is poised to set a new standard for performance and efficiency in the casting process. Built on extensive research and development, this new offering combines the latest advancements in materials and technology to deliver unparalleled results. With a focus on durability, precision, and ease of use, the product is designed to meet the rigorous demands of modern casting applications.
One of the key features of this new product is its ability to withstand high temperatures and extreme conditions, making it an ideal solution for a wide range of casting processes. This level of resilience not only ensures consistent and reliable performance but also minimizes the need for frequent replacements, ultimately reducing downtime and operational costs for manufacturers.
In addition to its exceptional durability, the new product also boasts a high level of precision. This is crucial in the casting process, where even the smallest variations can have a significant impact on the quality of the final product. By providing unparalleled accuracy and repeatability, the product helps manufacturers achieve the level of consistency and quality that is essential for success in today's competitive market.
Furthermore, the new product has been engineered with a focus on user-friendly design, ensuring that it is easy to handle and work with. This not only simplifies the casting process but also enhances safety and efficiency in the workplace. By minimizing the time and effort required to work with the product, manufacturers can maximize their productivity and focus on delivering exceptional results.
"We are thrilled to introduce this groundbreaking new product to the market," said a spokesperson for Mokey Castable. "We believe that it has the potential to transform the way that manufacturers approach the casting process, allowing them to achieve new levels of performance, efficiency, and quality. With this product, we are reaffirming our commitment to driving innovation in the casting industry and supporting the success of our clients."
As Mokey Castable continues to solidify its position as a leader in the casting industry, the introduction of this innovative new product marks a significant milestone for the company. By leveraging their expertise and commitment to excellence, Mokey Castable is poised to set a new standard for the industry, offering manufacturers a competitive edge and the opportunity to elevate the quality and efficiency of their casting processes. With this latest offering, Mokey Castable continues to demonstrate their dedication to pushing the boundaries and delivering solutions that empower their clients to thrive in an ever-evolving market.
Company News & Blog
High Density Ceramic Fiber Blanket: What You Need to Know
Ceramic Fiber Blanket Density (brand name removed) is a high-temperature insulation material, designed to provide excellent thermal performance and energy savings in a variety of industrial applications. This product is produced by {company name}, a leading manufacturer of thermal insulation and refractory products, with a strong focus on providing innovative solutions for high-temperature environments.With a commitment to quality and customer satisfaction, {company name} has been a trusted supplier of ceramic fiber products for over 20 years. The company's extensive experience and technical expertise have allowed them to develop advanced manufacturing processes, ensuring that their products meet the highest standards of performance and reliability.Ceramic Fiber Blanket Density is a lightweight, flexible insulation material, made from high-purity alumina-silica fibers. It offers low thermal conductivity, excellent thermal shock resistance, and outstanding sound absorption properties. This makes it an ideal choice for a wide range of industrial applications, including furnace linings, boiler insulation, and thermal barriers in high-temperature processing equipment.One of the key advantages of Ceramic Fiber Blanket Density is its high temperature resistance, with a maximum service temperature of up to 2300°F (1260°C). This allows it to withstand the extreme heat generated in industrial processes, while providing superior thermal insulation to help reduce energy consumption and operating costs.In addition to its excellent thermal performance, Ceramic Fiber Blanket Density also offers exceptional chemical stability, making it suitable for use in harsh chemical environments. It is non-corrosive and has low chemical reactivity, ensuring long-term durability and reliability in challenging industrial applications.{company name} takes pride in its commitment to environmental sustainability and safety. Ceramic Fiber Blanket Density is manufactured in compliance with strict environmental regulations, using eco-friendly production processes and raw materials. This ensures that the product meets the highest environmental standards and contributes to a cleaner, greener future.The company also places a strong emphasis on safety, ensuring that all of its products, including Ceramic Fiber Blanket Density, are designed to meet strict safety standards and regulations. This focus on safety and quality has earned {company name} a reputation as a trusted partner for industrial insulation solutions, with a track record of delivering reliable, high-performance products to customers worldwide.As a leading supplier of insulation and refractory products, {company name} provides comprehensive technical support and customer service to ensure the successful implementation of Ceramic Fiber Blanket Density in industrial applications. The company's team of experienced engineers and technical specialists offers expert guidance and assistance to help customers select the right insulation solutions for their specific needs.In conclusion, Ceramic Fiber Blanket Density from {company name} is a high-performance insulation material, designed to meet the demanding requirements of industrial high-temperature applications. With its exceptional thermal performance, chemical resistance, and environmental sustainability, this product is a reliable and cost-effective solution for a wide range of industrial insulation needs. As {company name} continues to innovate and expand its product offerings, customers can expect to benefit from the company's ongoing commitment to excellence and customer satisfaction.
Refractory Bricks: Understanding their Significance and Applications
Refractory Bricks Are Transforming the Construction IndustryIntroduction:In recent years, there has been a significant shift in the construction industry, with an increasing demand for sustainable and innovative building materials. Refractory bricks have emerged as a game-changing solution, offering enhanced strength, durability, and resistance to extreme temperatures. One notable company at the forefront of this revolution is [], with its breakthrough refractory bricks creating ripples of excitement within the construction sector.The Evolution of Refractory Bricks:Refractory bricks have revolutionized the way structures are built, providing unprecedented levels of performance and reliability. These bricks are specially designed to withstand incredibly high temperatures, making them ideal for applications in furnaces, kilns, incinerators, and various industrial processes.Traditionally, refractory bricks were made using clay and silica materials, which limited their capabilities and longevity. However, technological advancements have now enabled the production of bricks with much higher melting points and superior insulation properties. This has opened up a wide range of possibilities for their use in different industries, from power plants to steel mills.Combining Strength with Sustainability:One of the most significant advantages of refractory bricks, particularly those offered by [], is their eco-friendly nature. These bricks are composed of recycled materials, including silica, alumina, and other aggregates, making them an excellent choice for environmentally conscious construction projects.Moreover, the production process used by the company minimizes carbon emissions, further reducing its environmental impact. As sustainability becomes an increasingly important consideration in the construction sector, refractory bricks have emerged as a frontrunner in providing a more responsible and eco-friendly alternative to conventional building materials.Exceptional Heat Resistance Properties:The primary characteristic that sets refractory bricks apart from other construction materials is their exceptional heat resistance. These bricks are engineered to withstand extreme temperatures, preventing thermal damage and ensuring the integrity of the structures they are used in.[] has pushed the boundaries of heat resistance by developing bricks with melting points well beyond the capabilities of traditional clay or silica-based products. This innovation has allowed for the construction of structures that can withstand extreme heat without compromising safety or performance.Durability and Longevity:Refractory bricks are known for their outstanding durability, making them a preferred choice for industries requiring long-lasting and reliable structures. Thanks to their high-temperature resistance, these bricks are resistant to thermal shock, chemical erosion, and wear and tear, ensuring a prolonged lifespan even in challenging environments.Furthermore, [] has taken durability to new heights with their advanced production techniques. Their refractory bricks are designed to have low porosity and high density, increasing their resistance to corrosion, erosion, and mechanical stress. These qualities make them an ideal choice for heavy-duty industrial applications, contributing to overall cost savings and improved operational efficiency.Enhanced Insulation and Energy Efficiency:Another remarkable feature of refractory bricks is their exceptional insulation properties. These bricks have high thermal conductivity, allowing them to effectively trap heat and prevent energy loss. As a result, they contribute to increased energy efficiency in industrial processes, reducing energy consumption and lowering operational costs.The innovative manufacturing techniques employed by [] result in bricks with superior insulating capabilities. This ensures a higher level of thermal efficiency within structures, leading to reduced heat transfer and greater energy conservation.Conclusion:Refractory bricks have emerged as a transformative force in the construction industry. With their unrivaled strength, exceptional resistance to extreme temperatures, and long-lasting durability, these bricks are revolutionizing the way structures are built. The advancements made by [] in this field are remarkable, with their eco-friendly approach, superior heat resistance, and enhanced insulation properties setting them apart from traditional brick manufacturers.As the demand for sustainable and high-performance building materials continues to rise, refractory bricks are paving the way for a more efficient and resilient construction sector. With their significant contributions to energy conservation, reduced maintenance costs, and increased operational efficiency, refractory bricks are shaping the future of construction, and [] is at the forefront of this transformation.
Advancements in Continuous Casting Furnace Technology for Enhanced Industrial Efficiency
[Company Introduction]{Insert Company Name} is a renowned leader in the manufacturing sector, known for its cutting-edge technologies and innovative solutions. With a global footprint and an extensive portfolio of products, the company has established its presence across various industries, including the metals industry.[News Content]Continuous Casting Furnace Revolutionizes the Metals Industry{City, Date} - In a bid to redefine the way metal products are manufactured, {Insert Company Name}, a pioneer in industrial technologies, has unveiled its latest breakthrough in the field of metal casting - the state-of-the-art Continuous Casting Furnace (CCF). This revolutionary furnace is set to transform the metals industry, offering unmatched efficiency, precision, and sustainability.Traditionally, metal casting processes have relied on batch production, which involved melting large quantities of metal to create discrete batches of products. However, the Continuous Casting Furnace, developed by {Insert Company Name}, eliminates the need for batch production, leading to significant improvements in productivity and product quality.The Continuous Casting Furnace incorporates advanced technologies that allow for the continuous production of metal products, such as steel billets, slabs, and blooms. This continuous process ensures a constant flow of output, minimizing downtime and maximizing overall throughput. With this innovative furnace, manufacturers can achieve higher production volumes, reducing lead times and meeting the ever-increasing demands of the market.One of the standout features of the Continuous Casting Furnace is its ability to enhance product quality and consistency. By maintaining a steady, controlled flow of molten metal, the furnace ensures uniformity in the casting process, resulting in products with fewer defects, improved dimensional accuracy, and enhanced surface finishes. This translates into superior end products that meet the stringent quality standards of various industries.In addition to its efficiency and product quality benefits, the Continuous Casting Furnace also offers remarkable sustainability advantages. The furnace utilizes advanced energy management systems that optimize energy consumption and decrease environmental impact. By streamlining the casting process, manufacturers can significantly reduce energy usage and minimize waste generated during production. This ensures a more sustainable approach to manufacturing, aligning with global efforts to reduce carbon emissions and promote eco-friendly practices.{Insert Company Name} has invested significant resources in research and development to bring the Continuous Casting Furnace to market. The company’s team of highly skilled engineers and metallurgical experts have collaborated to design a furnace that delivers exceptional performance across various industries, including automotive, construction, and manufacturing."The introduction of our Continuous Casting Furnace represents a major milestone in the metals industry. This cutting-edge technology will revolutionize the way metal products are manufactured, offering transformative benefits to our customers," said {Spokesperson Name}, {Job Title} at {Insert Company Name}.This breakthrough innovation is a testament to {Insert Company Name}'s commitment to pushing the boundaries of what is possible in industrial manufacturing. The company's dedication to research, development, and technological advancements has solidified its position as a global leader, continuously delivering solutions that address the evolving needs of industries worldwide.As the metals industry embraces the Continuous Casting Furnace, manufacturers can expect increased productivity, improved product quality, and a reduced environmental footprint. This game-changing technology is set to shape the future of metal casting, offering a more efficient, sustainable, and competitive approach to manufacturing.
Refractory Brick Lining: A Guide to Enhanced Furnace Protection
Title: Industry-Leading Refractory Brick Lining: Enhancing Durability and Efficiency in High-Temperature EnvironmentsIntroduction:In a world where industries heavily rely on high-temperature environments to carry out their operations, the demand for durable and efficient refractory brick lining has seen significant growth. With a keen understanding of this market need, our company has introduced a cutting-edge refractory brick lining (brand name omitted), to provide exceptional insulation and protection in extreme heat conditions. Designed to withstand the harshest industrial processes, our refractory brick lining has quickly gained recognition as an industry-leading solution.Understanding the Importance of Refractory Brick Lining:Refractory brick lining is used extensively across industries such as steel, cement, glass, and petrochemical to create reliable insulation and protection against extreme temperatures. These linings act as a barrier between high-temperature environments and the structural elements of industrial furnaces, kilns, reactors, and other high-temperature vessels, ensuring their longevity and safe operation.Features and Benefits of our Refractory Brick Lining:1. Exceptional Thermal Insulation:Our refractory brick lining is manufactured using high-quality materials, carefully formulated to deliver outstanding thermal insulation. This feature helps minimize heat loss, enhancing energy efficiency and reducing overall operating costs.2. Superior Resistance to High Temperatures:The refractory brick lining excels in maintaining structural integrity even under extreme heat conditions. This resistance to high temperatures ensures the longevity of industrial furnaces and other heat-intensive units, minimizing downtime and production interruption.3. Enhanced Anti-Spalling Properties:The specialized formulation of our refractory brick lining provides remarkable resistance against spalling, which can occur due to rapid temperature fluctuations. This feature significantly prolongs the lining's lifespan while ensuring a safer operating environment.4. Chemical and Corrosion Resistance:Our refractory brick lining is engineered to withstand harsh chemical environments, effectively protecting the structural elements from corrosive agents such as acids, alkalis, and molten metals. This durability is crucial for industries where such aggressive substances are commonly employed.5. Increased Mechanical Strength:To withstand the mechanical stress arising from thermal cycling and material movements within the high-temperature environment, our refractory brick lining is designed with improved mechanical strength. This ensures long-term stability and reduces the need for frequent maintenance or replacements.Application Areas:The versatility and superior performance of our refractory brick lining make it suitable for a wide range of applications within industries. Some key areas where our lining finds application include:1. Steel Manufacturing:Steel production involves extremely high temperatures, demanding durable and efficient lining solutions. Our refractory brick lining provides excellent resistance to heat, chemical attack, and mechanical stress, enhancing safety and productivity in steel plants.2. Cement Production:In cement kilns, our refractory brick lining acts as a barrier against extreme temperatures, ensuring the long-lasting operation of these crucial components. Its chemical and corrosion resistance makes it ideal for resisting the aggressive chemical reactions that occur during cement production.3. Glass Manufacturing:Glass production relies heavily on uniform heating throughout the process. Our refractory brick lining helps maintain consistent high temperatures in glass furnaces, enabling flawless production and reducing energy consumption.4. Petrochemical Industry:In the petrochemical industry, where processes involve handling corrosive chemicals, our refractory brick lining serves as a protective layer, guarding against chemical attacks and high-temperature conditions. This extends the lifespan of reactors and other equipment, resulting in enhanced operational efficiency.Conclusion:As industries continue to operate in high-temperature environments, the importance of reliable refractory brick lining cannot be understated. Our refractory brick lining (brand name omitted) offers exceptional thermal insulation, resistance to high temperatures, anti-spalling properties, and chemical resistance, making it the ideal solution for various industrial settings. By incorporating our advanced lining technology, businesses can enhance the durability, efficiency, and safety of their operations, resulting in improved productivity and reduced operational costs.
Insulation blankets are an effective solution for Kiln operations.
Title: Advanced Kiln Insulation Blanket Revolutionizes Industrial Heating ProcessesIntroduction:In modern industrial environments, optimizing energy efficiency and reducing heat loss are of utmost importance. With that in mind, a groundbreaking solution has emerged in the form of an advanced Kiln Insulation Blanket. By effectively containing and conserving heat, this innovative product has the potential to revolutionize heating processes across various industries, leading to cost savings and enhanced productivity.[Company Name], a leading provider of cutting-edge industrial solutions, has introduced a state-of-the-art kiln insulation blanket that exceeds all prevailing expectations. This groundbreaking product has made its mark due to its exceptional thermal insulation properties, which enable businesses to maintain accurate and consistent temperatures while minimizing energy consumption.Body:1. The Need for Advanced Kiln Insulation Blankets:The first section of the article will highlight the challenges industries face when it comes to maintaining precise & controlled temperatures in their kilns. It will discuss issues such as heat loss, energy inefficiency, and the consequent financial implications. Presenting these challenges will set the context for the revolutionary nature of the Kiln Insulation Blanket.2. The Features and Benefits:The following section will delve into the key features and benefits of the Kiln Insulation Blanket offered by [Company Name]. It will emphasize how this product's unique design and composition enable it to achieve outstanding heat retention and resist temperatures of up to [X] degrees Celsius (or Fahrenheit). Other advantages could include its lightweight nature, easy installation process, and compatibility with different kiln types.3. Applications Across Industries:Next, the article will explore the diverse industries that can reap the advantages of this advanced insulation blanket. Industries such as glass manufacturing, ceramics, metal forging, and even food processing might be mentioned. The versatility of the product is essential to highlight how it can cater to various heating processes, contributing to energy savings and precise temperature control.4. Environmental Impact:An important aspect to mention is the environmental impact of the Kiln Insulation Blanket. By minimizing heat loss and reducing energy consumption, this product helps businesses decrease their carbon footprint, making a significant contribution towards sustainable practices. This section will focus on the growing importance of environmental responsibility in today's world.5. Testimonials and Success Stories:To further establish credibility and demonstrate the product's effectiveness, it would be beneficial to include testimonials from satisfied customers or examples of successful case studies. These real-life examples will provide readers with concrete evidence of how the Kiln Insulation Blanket has positively impacted businesses in various sectors. Testimonials highlighting cost savings, enhanced productivity, and better temperature control should be included.6. The Future of Kiln Insulation Technology:This final section will discuss the potential for further advancements in kiln insulation technology. It could touch on ongoing research and development efforts undertaken by [Company Name] or other industry players to continue improving insulation blanket solutions. This will establish the idea that the innovation brought by [Company Name] is not just a static solution but part of a broader movement towards more efficient and sustainable heating processes.Conclusion:In conclusion, the revolutionary Kiln Insulation Blanket introduced by [Company Name] provides a game-changing solution for industries seeking to enhance their heating processes. Its exceptional insulation capabilities and numerous benefits, including energy savings and precise temperature control, make it a crucial component for any business reliant on kilns. By investing in this advanced technology, businesses can boost efficiency, reduce costs, and contribute towards a more sustainable future.
How to Choose the Best 5kg Crucible for Your Needs
5kg Crucible: The Latest Breakthrough in Metallurgy TechnologyIn recent years, the demand for high-quality metal products has been increasing, leading to the development of new and improved metallurgy technologies. One company that has been at the forefront of this industry is {Company Name}, a leading provider of advanced materials and solutions for various industrial applications.{Company Name} has recently introduced the latest addition to its range of metallurgy products - the 5kg Crucible. This new crucible is designed to meet the growing needs of the metal industry by providing a reliable and efficient solution for melting and casting various types of metals.The 5kg Crucible is manufactured using high-quality materials and advanced manufacturing processes, ensuring its durability and performance. The crucible is capable of withstanding high temperatures, making it suitable for a wide range of metal melting applications. Its design also allows for easy handling and maintenance, making it an ideal choice for both small-scale and large-scale metal production facilities.One of the key features of the 5kg Crucible is its improved energy efficiency. The design of the crucible allows for better heat transfer, resulting in reduced energy consumption and lower operating costs. This makes it a cost-effective solution for metal manufacturers looking to improve their production efficiency while reducing their environmental impact.In addition to its energy efficiency, the 5kg Crucible also offers superior performance in terms of metal quality and purity. The crucible is designed to minimize impurities and ensure a consistent and homogeneous melting process, resulting in high-quality metal products that meet the stringent requirements of various industries.{Company Name} has always been committed to innovation and customer satisfaction, and the introduction of the 5kg Crucible is a testament to this. The company's extensive research and development efforts have led to the creation of a product that addresses the evolving needs of the metal industry, providing a reliable and cost-effective solution for metal manufacturers around the world.The 5kg Crucible is just the latest example of {Company Name}'s dedication to delivering cutting-edge solutions for the metallurgy industry. The company's comprehensive range of products includes a variety of advanced materials, alloys, and equipment that are designed to meet the diverse needs of different metal manufacturing processes.{Company Name} also offers a range of technical support and consultancy services to help customers optimize their metal production processes and improve their overall efficiency. With a team of experienced metallurgy experts, the company is able to provide tailored solutions and recommendations to help customers achieve their production goals and stay ahead of the competition.As the demand for high-quality metal products continues to grow, the introduction of the 5kg Crucible by {Company Name} is set to make a significant impact on the metallurgy industry. With its advanced design, superior performance, and cost-effective operation, the 5kg Crucible is poised to become the go-to solution for metal manufacturers looking to enhance their production capabilities and meet the increasing demands of their customers.In conclusion, the 5kg Crucible represents the latest breakthrough in metallurgy technology, and {Company Name} is proud to be at the forefront of this development. With its commitment to innovation, quality, and customer satisfaction, the company continues to lead the way in providing advanced solutions for the metal industry, helping manufacturers around the world achieve their production goals and stay ahead in an ever-evolving market.
Exploring the Benefits of Ceramic Cloth Insulation for Enhanced Energy Efficiency
Ceramic Cloth Insulation Revolutionizing Heat Control in IndustriesInnovation and sustainable solutions have become increasingly important in today's industrial landscape. Industries are constantly seeking ways to enhance efficiency, reduce energy consumption, and mitigate environmental impacts. One company emerging as a frontrunner in this quest is {Ceramic Cloth Insulation}, whose cutting-edge product is revolutionizing heat control in various sectors.{Ceramic Cloth Insulation}, a global leader in thermal management solutions, has developed a highly advanced material that provides superior insulation capabilities. Designed to withstand extreme temperatures and harsh conditions, their product has garnered immense attention from industries ranging from aerospace to automotive manufacturing, and even energy production.The key to {Ceramic Cloth Insulation}'s success lies in its unique composition. Made from a blend of high-quality ceramic fibers and specialized fabrics, the insulation material possesses exceptional thermal resistance characteristics. This innovative technology enables industries to effectively control and manage heat, achieving significant operational efficiencies.With the ability to withstand temperatures of up to 1,800 degrees Celsius, {Ceramic Cloth Insulation} ensures the utmost safety for industries operating under extreme conditions. This breakthrough development not only enhances the longevity of equipment but also reduces maintenance costs, making it an attractive choice for companies across the board.One of the primary advantages of {Ceramic Cloth Insulation} is its versatility. The material's flexibility allows for easy handling and installation, making it ideal for a wide range of applications. Whether it's insulating pipes in chemical plants, lining furnaces in steel manufacturing, or protecting cables in the aerospace industry, this product proves to be a versatile solution for heat management needs.Moreover, this innovative insulation material acts as a barrier to prevent unnecessary heat transfer. By significantly reducing heat loss and maximizing thermal efficiency, {Ceramic Cloth Insulation} contributes to substantial energy savings for industrial plants. This not only lowers operational costs but also aligns with industries' growing focus on sustainable practices.The positive impact of {Ceramic Cloth Insulation} on the environment cannot be overlooked. By reducing energy consumption, industries using this insulation material are effectively lowering their carbon footprint. This aligns with global efforts to combat climate change and promote sustainability, making {Ceramic Cloth Insulation} an essential component of the transition towards greener industrial practices.To further cater to industries' diverse needs, {Ceramic Cloth Insulation} offers a range of customized solutions. Their team of experts collaborates closely with clients to understand specific requirements and provide tailored insulation solutions that maximize efficiency. This customer-centric approach has earned {Ceramic Cloth Insulation} a reputation for excellence and reliability.As demand for innovative thermal management solutions continues to grow, {Ceramic Cloth Insulation} remains committed to pushing the boundaries of technology. Through ongoing research and development, the company aims to further enhance the performance of their insulation material and expand its application in various industries.By leveraging their expertise in thermal management, {Ceramic Cloth Insulation} is not only transforming heat control practices but also contributing to industrial efficiency and sustainability. With their advanced insulation solutions, industries can maximize operational productivity while reducing energy consumption and minimizing environmental impacts.In conclusion, the innovative and adaptable nature of {Ceramic Cloth Insulation} has positioned the company as a leader in thermal management solutions. With their exceptional insulation material, industries can now effectively control heat, ensuring safety, efficiency, and sustainability across various sectors. As the demand for sustainable practices continues to increase, {Ceramic Cloth Insulation} remains at the forefront of technological advancements in the industry.
Lightweight and Insulating: Discover the Versatile Ceramic Fiber Blanket Now!
Title: Innovative Ceramic Fiber Blanket Redefines Insulation StandardsSubtitle: Cutting-edge insulation solution by {Company Name} revolutionizes the industryIntroduction:{Company Name}, a renowned leader in manufacturing advanced materials for various industries, has recently unveiled its latest breakthrough in insulation technology - the 6lb Ceramic Fiber Blanket. This revolutionary product sets a new standard for thermal insulation by offering superior heat resistance, flexibility, and durability. {Company Name}'s commitment to innovation has enabled them to develop this state-of-the-art solution that meets the evolving needs of industries worldwide.Body:1. Rising Demand for Advanced Insulation Solutions (100 words)With energy efficiency and environmental concerns taking center stage across industries, the demand for effective insulation materials continues to grow. This necessitates solutions that can withstand extreme temperatures while offering exceptional thermal and fire resistance properties. Recognizing this need, {Company Name} invested significant resources in research and development, leading to the development of the 6lb Ceramic Fiber Blanket.2. Unparalleled Heat Resistance and Temperature Control (150 words)Unlike traditional insulation materials, the 6lb Ceramic Fiber Blanket boasts an exceptional ability to withstand high temperatures, making it the ideal choice for various applications. Its unique composition, incorporating advanced ceramic fibers, ensures excellent heat resistance and thermal stability. This breakthrough solution enables companies to achieve optimal temperature control, enhancing energy efficiency and reducing operational costs.3. Superior Flexibility and Ease of Installation (150 words)One of the key advantages of the 6lb Ceramic Fiber Blanket is its flexibility, enabling easy installation even in complex and irregular-shaped spaces. This versatility allows for seamless integration into diverse industrial processes, including furnaces, kilns, boilers, and other high-temperature environments. Its lightweight nature makes handling and maneuvering effortless, ensuring a hassle-free installation process for workers.4. Unrivaled Durability and Longevity (150 words){Company Name}'s Ceramic Fiber Blanket delivers exceptional durability, ensuring outstanding insulation performance over extended periods of use. Its robust construction materials ensure resistance against wear and tear, thermal shock, and chemical corrosion. Additionally, this innovative blanket exhibits low shrinkage characteristics, ensuring long-term thermal efficiency for enhanced reliability in critical applications.5. Enhanced Safety and Fire Resistance (150 words)The 6lb Ceramic Fiber Blanket boasts excellent fire resistance properties, offering an added layer of safety and protection in various industries. Manufactured with high-quality ceramic fibers and binder materials, it meets the stringent fire safety standards required for critical applications. This insulation material helps to minimize the risks associated with fire hazards and ensures personnel safety.6. Energy Efficiency and Cost Savings (100 words)By utilizing {Company Name}'s Ceramic Fiber Blanket, industries can significantly reduce energy consumption and associated costs. Its remarkable thermal insulation properties eliminate heat losses and reduce the need for frequent temperature adjustments. This, in turn, enhances energy efficiency, resulting in substantial cost savings over time. Additionally, the excellent durability of the blanket reduces maintenance and replacement costs, making it a cost-effective investment for businesses.Conclusion (50 words)The 6lb Ceramic Fiber Blanket introduced by {Company Name} represents a game-changer in the insulation industry. With its unmatched heat resistance, flexibility, durability, and fire resistance properties, this innovative product allows industries to improve performance, achieve energy efficiency, and ensure the safety of their operations.Note: Remember to remove {Company Name} references and replace them with the actual company name before publishing the news.
New Casting Technology: Advancements in 3D Printing for Investment Casting
introducing the new product.Mokey Castable Introduces Innovative Product to Revolutionize Casting ProcessMokey Castable, a leading provider of innovative solutions in the casting industry, has recently unveiled a groundbreaking new product that is set to revolutionize the casting process. With a relentless commitment to excellence and a focus on pushing the boundaries of what is possible, Mokey Castable has developed a product that promises to deliver exceptional results and streamline the casting process for manufacturers around the world.Founded on the principle of innovation and driven by a passion for excellence, Mokey Castable has quickly established itself as a trusted provider of cutting-edge solutions for the casting industry. The company's team of experts is comprised of some of the most talented and experienced professionals in the field, all dedicated to developing and delivering products that address the unique challenges and needs of their clients.The new product, which has been kept under wraps until now, is poised to set a new standard for performance and efficiency in the casting process. Built on extensive research and development, this new offering combines the latest advancements in materials and technology to deliver unparalleled results. With a focus on durability, precision, and ease of use, the product is designed to meet the rigorous demands of modern casting applications.One of the key features of this new product is its ability to withstand high temperatures and extreme conditions, making it an ideal solution for a wide range of casting processes. This level of resilience not only ensures consistent and reliable performance but also minimizes the need for frequent replacements, ultimately reducing downtime and operational costs for manufacturers.In addition to its exceptional durability, the new product also boasts a high level of precision. This is crucial in the casting process, where even the smallest variations can have a significant impact on the quality of the final product. By providing unparalleled accuracy and repeatability, the product helps manufacturers achieve the level of consistency and quality that is essential for success in today's competitive market.Furthermore, the new product has been engineered with a focus on user-friendly design, ensuring that it is easy to handle and work with. This not only simplifies the casting process but also enhances safety and efficiency in the workplace. By minimizing the time and effort required to work with the product, manufacturers can maximize their productivity and focus on delivering exceptional results."We are thrilled to introduce this groundbreaking new product to the market," said a spokesperson for Mokey Castable. "We believe that it has the potential to transform the way that manufacturers approach the casting process, allowing them to achieve new levels of performance, efficiency, and quality. With this product, we are reaffirming our commitment to driving innovation in the casting industry and supporting the success of our clients."As Mokey Castable continues to solidify its position as a leader in the casting industry, the introduction of this innovative new product marks a significant milestone for the company. By leveraging their expertise and commitment to excellence, Mokey Castable is poised to set a new standard for the industry, offering manufacturers a competitive edge and the opportunity to elevate the quality and efficiency of their casting processes. With this latest offering, Mokey Castable continues to demonstrate their dedication to pushing the boundaries and delivering solutions that empower their clients to thrive in an ever-evolving market.