Melting Furnace: Efficient and Versatile Solution for Metal Workshops
By:Admin
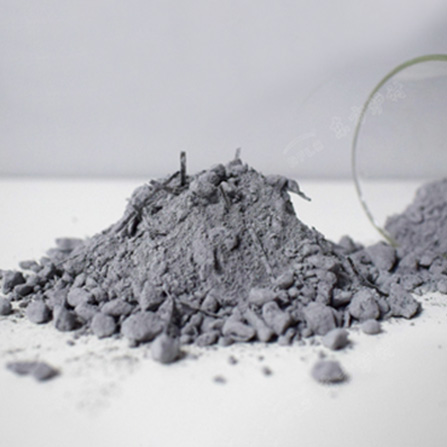
The metal industry has always been at the forefront of technological and manufacturing innovation, and the introduction of the Cupola Melting Furnace has once again changed the game for metal melting and casting. This advanced furnace technology, developed by a leading global manufacturer, is quickly becoming the go-to solution for efficient and cost-effective metal melting processes.
With over 20 years of experience in the industry, {Company Name} has consistently pushed the boundaries of metal melting and casting technology. The company's commitment to innovation and excellence has positioned them as a trusted partner for businesses in the metal industry, providing cutting-edge solutions to meet the evolving needs of the market.
The Cupola Melting Furnace is a testament to {Company Name}'s dedication to developing advanced and sustainable solutions for metal melting. The furnace is designed to efficiently melt a variety of metals, including iron, steel, and non-ferrous alloys, making it a versatile and reliable option for a wide range of applications. By harnessing the power of advanced combustion and heat transfer technologies, the furnace can achieve high melting rates while minimizing energy consumption and emissions, contributing to a more sustainable and environmentally friendly manufacturing process.
One of the key features of the Cupola Melting Furnace is its innovative refractory materials, which are designed to withstand the extreme temperatures and harsh conditions of metal melting. This not only ensures the longevity of the furnace but also minimizes downtime and maintenance costs, making it a cost-effective and reliable solution for metal production facilities. Additionally, the furnace is equipped with advanced control systems that allow for precise temperature and process control, enabling operators to optimize the melting process and achieve consistently high-quality results.
The introduction of the Cupola Melting Furnace has already made a significant impact on the metal industry, with numerous businesses adopting this advanced technology to enhance their metal melting and casting processes. By improving efficiency, reducing energy consumption, and minimizing environmental impact, the furnace has become an invaluable asset for businesses looking to stay competitive in the rapidly evolving metal industry.
{Company Name} remains committed to supporting its customers in their journey towards adopting advanced and sustainable metal melting solutions. The company provides comprehensive support and services, including installation, training, and maintenance, to ensure that businesses can maximize the benefits of the Cupola Melting Furnace. As a result, customers can rest assured that they are receiving not only an advanced technology solution but also the expertise and support needed to integrate it seamlessly into their operations.
Looking ahead, {Company Name} continues to push the boundaries of innovation and sustainability in the metal industry, with ongoing research and development efforts aimed at further enhancing the performance and capabilities of the Cupola Melting Furnace. By staying at the forefront of technological advancements and industry trends, the company remains dedicated to providing its customers with the most advanced and reliable solutions to meet their metal melting and casting needs.
In conclusion, the introduction of the Cupola Melting Furnace by {Company Name} represents a significant advancement in the metal melting industry. With its advanced technology, sustainability, and reliability, the furnace has quickly become an indispensable tool for businesses looking to enhance their metal production capabilities. As the company continues to innovate and expand its offerings, it is poised to remain a leader in the metal industry, empowering its customers to achieve their production goals with cutting-edge solutions.
Company News & Blog
Exploring the Advantages of Ceramic Fiber in Construction and Insulation Applications
Possible news article:Innovative Ceramic Fiber Material Offers High-Temperature Solutions for Industrial ApplicationsA leading manufacturer of high-performance materials has launched a new product line that leverages the properties of ceramic fibers to enhance the strength, insulation, and durability of various industrial systems. The company, based in the United States, has developed a proprietary process to produce Kaowool Ceramic Fiber, a versatile material that can withstand extreme temperatures and pressures, while also providing excellent resistance to chemicals, abrasion, and thermal shock. The new product line consists of different forms and configurations of the fiber, such as blankets, boards, ropes, papers, and modules, which can be customized to suit specific needs and applications.Ceramic fibers are a type of inorganic, non-metallic material that is made from spinning or blowing molten mineral substances into fine fibers. They are known for their exceptional thermal properties, including low thermal conductivity, high temperature resistance, and thermal stability. Ceramic fibers also have excellent mechanical properties, such as high tensile strength, stiffness, and toughness. Unlike organic fibers such as carbon or glass, ceramic fibers are not combustible, and do not release toxic gases when exposed to fire. These features make ceramic fibers ideal for use in high-temperature environments where conventional materials would fail or degrade, such as furnaces, kilns, boilers, pipes, and mufflers.Kaowool Ceramic Fiber takes advantage of these properties to offer a range of benefits for industrial users. For example, the fiber can be formed into lightweight, flexible blankets that can be wrapped around pipes or equipment to provide superior thermal insulation. The blankets are also resistant to chemical corrosion and erosion, making them suitable for harsh environments such as chemical plants or oil refineries. The blankets can tolerate temperatures up to 2600°F (1427°C) without shrinkage or deformation, and maintain their structural integrity even after exposure to rapid temperature changes or thermal cycling. This makes them ideal for use in furnaces or ovens that require precise temperature control or frequent heating and cooling cycles.In addition to blankets, Kaowool Ceramic Fiber is also available in boards, which can be used as heat shields, baffles, or supports. The boards offer a smooth surface that is easy to cut, drill, or machine, and can be shaped into complex geometries or contours. The boards are also highly resistant to impact and vibration, making them suitable for use in transportation or aerospace applications. The fiber can also be made into ropes, which can be knotted or woven into gaskets, seals, or packing for valves, pumps, or flanges. The ropes provide a tight, leak-proof seal that can withstand high pressures or vacuum. The fiber can also be used to make papers, which can be used as filters, insulators, or barriers. The papers can withstand moisture, chemicals, and gas permeation, making them useful in filtration, soundproofing, or packaging applications.Kaowool Ceramic Fiber also offers benefits for installation and maintenance. The fiber is easy to handle, cut, and install, and does not require specialized tools or skills. The fiber can be glued, screwed, or wedged into place, and can be reused or repaired as needed. The fiber also does not produce dust or fibers when handled, reducing the risk of occupational or environmental hazards. The fiber is also recyclable, and can be reused or repurposed after use, reducing waste and environmental impact.The company that produces Kaowool Ceramic Fiber has a long history of innovation in materials science. Founded in the early 20th century, the company has pioneered many advanced materials, such as silica aerogels, high-purity alumina, and specialty glasses. The company has also developed many applications for these materials, such as insulation, electronics, optics, and healthcare. The company has a global network of customers and partners in various industries, and is committed to sustainability, quality, and customer satisfaction.The launch of Kaowool Ceramic Fiber represents a significant addition to the company's portfolio of high-performance materials. The product line offers a compelling solution for industrial users who seek better performance, efficiency, and reliability in their systems. The company expects to see strong demand for the fiber in industries such as energy, chemicals, metals, ceramics, and transportation, where high temperatures and harsh conditions are common. The company also plans to develop new applications and forms of the fiber, leveraging its expertise in materials and processing. Overall, Kaowool Ceramic Fiber is poised to become a leading product in the global market for high-temperature materials and solutions.
Discover High-Quality Fire Bricks in Thailand for Your Furnace Needs" can be rewritten to "Get Reliable Fire Bricks in Thailand for Your Furnace Requirements".
Fire Bricks Strengthen Infrastructure in Thailand's Construction IndustryThailand's booming construction industry is set to experience a significant boost as Fire Bricks, a leading manufacturer of high-quality refractory materials, enters the market. With an extensive range of products and a commitment to innovation, the company aims to revolutionize the way infrastructure projects are carried out in the country. As Thailand continues to invest in its infrastructure, Fire Bricks comes as a timely addition to meet the growing demands of the construction sector.Fire Bricks Thailand, founded in 2005, has quickly established itself as a trusted and reliable manufacturer of fire bricks and other refractory materials. With a state-of-the-art manufacturing facility and a team of experienced professionals, the company prides itself on delivering superior quality products that withstand extreme temperatures and provide long-lasting durability.One of the key advantages of Fire Bricks' products is their ability to withstand high temperatures, making them an ideal choice for buildings and structures that require fire resistance. The company's fire bricks are made from a special blend of clay and other binding materials, ensuring they retain their strength even in the face of intense heat. This makes them perfect for applications such as lining fireplaces, furnaces, kilns, and industrial chimneys.Additionally, Fire Bricks Thailand offers a range of other refractory products, including insulation bricks, castables, and mortars. These products provide excellent thermal insulation, helping to reduce energy consumption and maintain a comfortable temperature inside buildings. Moreover, with their high strength and resistance to erosion, Fire Bricks' refractory products are suitable for lining crucial industrial equipment such as ladles, blast furnaces, and boilers, ensuring a reliable and efficient operation.The quality and performance of Fire Bricks' products have been recognized by clients across various industries. Fire Bricks Thailand has collaborated with renowned construction companies, architects, and engineers on numerous prestigious projects, including the construction of commercial buildings, power plants, and steel mills. By focusing on consistent innovation and product development, the company constantly strives to meet the specific needs and requirements of its customers.Furthermore, Fire Bricks Thailand adheres to strict quality control measures throughout the manufacturing process to ensure that every product that leaves the factory meets the highest standards. The company's commitment to quality has earned it various certifications and accolades in the industry, cementing its reputation as a trusted supplier of refractory materials.The entry of Fire Bricks into Thailand's construction industry is expected to fuel further growth and development in the sector. With an increasing number of infrastructure projects on the horizon, the demand for reliable and effective refractory materials is set to soar. Fire Bricks Thailand's advanced manufacturing techniques, coupled with their wide range of products, position the company as a frontrunner in meeting this demand.Moreover, Fire Bricks Thailand's commitment to sustainability is noteworthy. The company utilizes environmentally friendly production methods, minimizing waste and reducing its carbon footprint. By investing in research and development, Fire Bricks continues to explore innovative ways to enhance the performance and environmental impact of their products.As Thailand aims to enhance its infrastructure to support economic growth and cater to the needs of its population, the arrival of Fire Bricks Thailand is a welcomed addition. With their expertise, commitment to quality, and focus on sustainability, the company is well-positioned to contribute to the success of Thailand's construction industry. Their innovative refractory materials will undoubtedly strengthen the country's infrastructure, ensuring safety, longevity, and efficiency in future construction projects.
Refractory Bricks: Understanding their Significance and Applications
Refractory Bricks Are Transforming the Construction IndustryIntroduction:In recent years, there has been a significant shift in the construction industry, with an increasing demand for sustainable and innovative building materials. Refractory bricks have emerged as a game-changing solution, offering enhanced strength, durability, and resistance to extreme temperatures. One notable company at the forefront of this revolution is [], with its breakthrough refractory bricks creating ripples of excitement within the construction sector.The Evolution of Refractory Bricks:Refractory bricks have revolutionized the way structures are built, providing unprecedented levels of performance and reliability. These bricks are specially designed to withstand incredibly high temperatures, making them ideal for applications in furnaces, kilns, incinerators, and various industrial processes.Traditionally, refractory bricks were made using clay and silica materials, which limited their capabilities and longevity. However, technological advancements have now enabled the production of bricks with much higher melting points and superior insulation properties. This has opened up a wide range of possibilities for their use in different industries, from power plants to steel mills.Combining Strength with Sustainability:One of the most significant advantages of refractory bricks, particularly those offered by [], is their eco-friendly nature. These bricks are composed of recycled materials, including silica, alumina, and other aggregates, making them an excellent choice for environmentally conscious construction projects.Moreover, the production process used by the company minimizes carbon emissions, further reducing its environmental impact. As sustainability becomes an increasingly important consideration in the construction sector, refractory bricks have emerged as a frontrunner in providing a more responsible and eco-friendly alternative to conventional building materials.Exceptional Heat Resistance Properties:The primary characteristic that sets refractory bricks apart from other construction materials is their exceptional heat resistance. These bricks are engineered to withstand extreme temperatures, preventing thermal damage and ensuring the integrity of the structures they are used in.[] has pushed the boundaries of heat resistance by developing bricks with melting points well beyond the capabilities of traditional clay or silica-based products. This innovation has allowed for the construction of structures that can withstand extreme heat without compromising safety or performance.Durability and Longevity:Refractory bricks are known for their outstanding durability, making them a preferred choice for industries requiring long-lasting and reliable structures. Thanks to their high-temperature resistance, these bricks are resistant to thermal shock, chemical erosion, and wear and tear, ensuring a prolonged lifespan even in challenging environments.Furthermore, [] has taken durability to new heights with their advanced production techniques. Their refractory bricks are designed to have low porosity and high density, increasing their resistance to corrosion, erosion, and mechanical stress. These qualities make them an ideal choice for heavy-duty industrial applications, contributing to overall cost savings and improved operational efficiency.Enhanced Insulation and Energy Efficiency:Another remarkable feature of refractory bricks is their exceptional insulation properties. These bricks have high thermal conductivity, allowing them to effectively trap heat and prevent energy loss. As a result, they contribute to increased energy efficiency in industrial processes, reducing energy consumption and lowering operational costs.The innovative manufacturing techniques employed by [] result in bricks with superior insulating capabilities. This ensures a higher level of thermal efficiency within structures, leading to reduced heat transfer and greater energy conservation.Conclusion:Refractory bricks have emerged as a transformative force in the construction industry. With their unrivaled strength, exceptional resistance to extreme temperatures, and long-lasting durability, these bricks are revolutionizing the way structures are built. The advancements made by [] in this field are remarkable, with their eco-friendly approach, superior heat resistance, and enhanced insulation properties setting them apart from traditional brick manufacturers.As the demand for sustainable and high-performance building materials continues to rise, refractory bricks are paving the way for a more efficient and resilient construction sector. With their significant contributions to energy conservation, reduced maintenance costs, and increased operational efficiency, refractory bricks are shaping the future of construction, and [] is at the forefront of this transformation.
Discover the Advantages of Refractory Clay Bricks for Enhanced Performance
Refractory Clay Bricks Prove to Be a Game-Changer for the Construction IndustryThe construction industry has seen significant growth in the past decade, with the need for new infrastructure and residential buildings on the rise. However, with this growth come challenges, and one of the most significant challenges faced by the industry is finding the right materials to withstand high temperatures and harsh conditions. Luckily, the development of refractory clay bricks has proven to be a game-changer.Refractory clay bricks are specially designed to withstand high temperatures and have a higher level of resistance to heat than standard bricks. They are used in kilns, furnaces, blast furnaces, and other high-temperature processing units. The construction industry has been quick to adopt this new technology, as it has significantly enhanced the durability and longevity of structures.One of the prominent companies in the industry that produces high-quality refractory clay bricks is located in China. Refractory clay bricks produced by this company are made of high-quality raw materials and have a high level of sintering strength. They are widely used in industries such as metallurgy, chemical engineering, building materials, and electric power.The manufacturing process of these refractory clay bricks is environmentally friendly, and the quality control process is rigorous. The company has invested in state-of-art-production lines, advanced testing equipment, and cutting-edge technology to ensure that their products meet international standards.The company offers a wide range of refractory clay bricks, including high-alumina bricks, fireclay bricks, silica bricks, magnesia bricks, and many more. These bricks are made to suit different industries and applications, making them versatile and adaptable.The high-alumina bricks have excellent heat resistance, making them suitable for lining furnace walls, roofs, and bottoms. The fireclay bricks are used in metallurgy, building materials, and machinery manufacturing industries. They have a high level of wear resistance, making them suitable for lining the walls of kilns and furnaces. Silica bricks are used in glass-making industries and have good thermal shock resistance. Magnesia bricks are used in metallurgy industries and have high thermal conductivity, excellent thermal shock resistance, and high refractoriness.The company has experienced significant growth over the years due to the quality of their products and their commitment to customer satisfaction. They have a team of experts who can offer technical support to their clients and provide solutions to their refractory-related problems. They also have a vast distribution network, ensuring that their products reach their clients in a timely and efficient manner.In conclusion, the development of refractory clay bricks has proven to be a game-changer for the construction industry. The high level of resistance to heat and other environmental factors has made these bricks a preferred choice for many industries. The company in China has distinguished themselves in this industry, and their commitment to quality and customer satisfaction has earned them a reputation as a leading producer of high-quality refractory clay bricks. With the growing demand for durable and high-performance materials in the construction and industrial sectors, the future looks bright for companies such as this.
Discover The Best Cement for Fire Bricks" can be rewritten as "Find the Perfect Cement for Your Fire Bricks
Title: Fire Bricks Cement Revolutionizes Construction Industry with Superior Quality and DurabilityIntroduction:Fire Bricks Cement (brand name to be removed), a leading player in the construction materials market, has been at the forefront of innovation and excellence. With a strong commitment to delivering high-quality products, the company has recently introduced a groundbreaking fire bricks cement that is set to revolutionize the construction industry. This innovative product offers superior strength, durability, and fire resistance, making it an ideal choice for a wide range of applications. In this article, we will explore the unique features and advantages of Fire Bricks Cement and delve into the company's dedication to meeting the evolving needs of customers.Superior Quality and Durability:Fire Bricks Cement has earned a formidable reputation within the construction industry due to its unwavering focus on quality and durability. By utilizing advanced manufacturing techniques and state-of-the-art materials, the company ensures that its fire bricks cement is of the highest standard. With an exceptional compressive strength and resistance to extreme temperatures, this cement acts as an excellent insulator, delivering a reliable and long-lasting solution for builders and architects.Unrivalled Fire Resistance:Fire resistance is a critical factor in construction materials, particularly in high-risk facilities like industrial plants, commercial buildings, and residences. Recognizing this need, Fire Bricks Cement has formulated a product that offers unparalleled fire resistance. The fire bricks cement is engineered to withstand intense heat without deterioration, thus minimizing the risk of structural damage and potential loss of life. This innovative solution provides peace of mind to both construction professionals and building owners alike.Versatility in Applications:One of the significant advantages of Fire Bricks Cement is its versatility in various construction applications. This cement can be used in diverse settings, such as furnaces, fireplaces, chimneys, pizza ovens, kilns, and other areas that require thermal insulation and fire protection. Its adaptability and compatibility with different surface materials make it an invaluable asset to architects, builders, and homeowners seeking dependable and efficient construction solutions.Environmental Sustainability:Fire Bricks Cement recognizes the importance of sustainable construction practices. In this regard, the company places great emphasis on integrating environmentally friendly elements into its manufacturing processes. By using eco-friendly materials and adhering to sustainable production practices, Fire Bricks Cement ensures minimal environmental impact while maintaining the highest quality standards. This commitment to sustainability further establishes the company as an industry leader in responsible and ethical construction practices.Customer-Centric Approach:With a strong focus on customer satisfaction, Fire Bricks Cement has built a reputation for delivering exceptional service and support. The company values client feedback and strives to cultivate strong relationships by understanding and addressing specific customer needs. By providing comprehensive guidance and technical expertise, Fire Bricks Cement assists architects, builders, and homeowners in making informed decisions regarding construction materials, ensuring successful project execution.Conclusion:Fire Bricks Cement has emerged as a game-changer in the construction industry with its groundbreaking fire bricks cement. With superior quality, unrivalled fire resistance, versatility in applications, and commitment to sustainability, the company sets new standards for excellence. As the industry evolves, Fire Bricks Cement continues to innovate, providing architects, builders, and homeowners with cutting-edge construction solutions.
Different Varieties of Refractory Castable for Industrial Heating Applications
Types Of Refractory Castable Refractory castables are commonly used in various industries to create high-temperature resistant linings and structures. They are composed of a combination of refractory aggregates, binders, and additives to provide the necessary properties for each specific application. In this article, we will explore some common types of refractory castables and their uses.1. Low Cement CastablesLow cement castables, also known as LCCs, are a type of refractory castable with low cement content. They are characterized by their excellent strength, abrasion resistance, and thermal shock resistance. Low cement castables are commonly used in applications where high mechanical strength and resistance to thermal cycling are required, such as in the lining of rotary kilns, boilers, and ladles.2. Self-flow CastablesSelf-flow castables, also referred to as flowable refractory castables or pumpable refractory castables, are a type of castable that can flow and fill complex shapes without the need for vibration or tamping. They are highly fluid, which allows for easy and efficient installation in various applications, including monolithic linings, repair works, and pre-cast shapes. Self-flow castables offer excellent flowability, strength, and thermal shock resistance.3. Insulating CastablesInsulating castables are designed to provide superior thermal insulation properties. They are lightweight and have low thermal conductivity, making them ideal for applications where reducing heat loss is crucial. Insulating castables can be used in a wide range of industries, including ceramics, petrochemicals, and iron and steel. They are commonly used for lining furnaces, kilns, and other high-temperature equipment.4. High Alumina CastablesHigh alumina castables contain a high percentage of alumina (Al2O3) content, typically above 60%. They exhibit excellent thermal shock resistance and high strength at both ambient and elevated temperatures. High alumina castables are suitable for applications that require resistance to high temperatures and aggressive chemical environments, such as in the lining of petrochemical reactors, power plants, and incinerators.5. Dense CastablesDense castables, as the name suggests, are characterized by their high density and strength. They are commonly used in heavy-duty applications that require resistance to abrasion, corrosion, and erosion. Dense castables are used in industries such as iron and steel, cement, and non-ferrous metals. They are widely used in areas that experience severe wear, including furnace linings, ladles, and kiln hoods.Company Introduction - {Company Name}{Company Name} is a leading manufacturer and supplier of refractory castables, providing high-quality solutions to various industries worldwide. With years of experience in the field, {Company Name} has developed a strong reputation for delivering innovative and reliable products.At {Company Name}, we offer a wide range of refractory castables tailored to meet the specific requirements of our customers. Our products are manufactured using advanced technology and high-quality raw materials to ensure superior performance and durability. We have a team of skilled professionals who are committed to providing exceptional customer service and technical support.In addition to refractory castables, {Company Name} also offers a comprehensive range of refractory bricks, ceramic fibers, and other refractory materials. We strive to continuously improve our products and develop new solutions to meet the evolving needs of the industry.ConclusionRefractory castables play a vital role in the construction of high-temperature resistant linings and structures. The different types of refractory castables mentioned above provide a wide range of properties and characteristics to cater to the specific needs of various industries. With a leading company like {Company Name} offering high-quality solutions, industries can rely on these castables for their thermal insulation, mechanical strength, and durability requirements.
Essential Guide: Key Facts About Refractory Kilns and Their Uses
Refractory Kiln: Revolutionizing the Heat Treatment Industry[City], [Date] - The refractory kiln industry has witnessed a significant breakthrough with the introduction of a state-of-the-art refractory kiln developed by [Company Name]. This revolutionary product is set to redefine the standards of heat treatment processes by providing unmatched efficiency, durability, and versatility.[Company Name], a leading provider of industrial solutions, has been at the forefront of innovation within the heat treatment industry for over a decade. Their commitment to research and development has led to the creation of cutting-edge technologies that deliver exceptional performance and reliability.The newly unveiled refractory kiln is the result of years of meticulous engineering and rigorous testing. It incorporates a proprietary design that maximizes thermal efficiency, resulting in reduced energy consumption and lower operating costs. This groundbreaking kiln also offers enhanced durability, enabling it to withstand high temperatures and harsh operating conditions, making it a preferred choice for industries such as ceramics, metals, and glass manufacturing.One of the key features of the refractory kiln is its advanced temperature control system, which ensures precise and consistent heat distribution throughout the chamber. This is crucial for achieving optimal results in a wide range of heat treatment processes, including sintering, calcination, and annealing. The kiln's innovative thermal management technology minimizes heat loss and enables operators to achieve their desired temperature profiles with utmost accuracy.Moreover, the refractory kiln's versatility allows for customization to meet the specific requirements of different industries. With adjustable settings for temperature, airflow, and process duration, it offers unparalleled flexibility in accommodating various materials and desired outcomes. This adaptability empowers businesses to optimize their manufacturing processes, leading to improved productivity and quality control.Safety remains a top priority for [Company Name], and the refractory kiln is no exception. It is equipped with advanced safety features to ensure reliable and secure operations. The kiln's integrated safety systems monitor critical parameters, such as gas flow, temperature, and pressure, providing real-time feedback to operators and triggering automatic shut-off mechanisms when necessary.In addition to its technical capabilities, [Company Name] offers comprehensive support services to customers. From installation and commissioning to regular maintenance and troubleshooting, their team of highly skilled technicians are available round the clock to assist clients and ensure uninterrupted operations. This commitment to customer satisfaction has earned [Company Name] an impeccable reputation in the industry.The introduction of the refractory kiln by [Company Name] marks a significant milestone in the heat treatment sector. Its unprecedented efficiency, durability, and versatility offer a transformative solution to businesses seeking to enhance their production capabilities. By incorporating cutting-edge technology, [Company Name] continues to shape the future of the heat treatment industry, setting new benchmarks for excellence.With global demand for heat treatment processes steadily increasing, the refractory kiln by [Company Name] promises to be a game-changer. As industries strive for improved efficiency and sustainability, this revolutionary product fulfills their requirements while maintaining the highest standards of performance and safety.
Aluminum Melting Forge: An Essential Guide for Efficient Aluminum Melting
Aluminum Melting Forge: A Revolutionary Solution for the Metal Manufacturing IndustryIn the metal manufacturing industry, the process of melting and casting aluminum is critical. This process has traditionally been accomplished through a variety of methods, including electric arc furnaces, induction furnaces, and gas-fired furnaces. However, these methods are often inefficient, costly, and time-consuming. Enter Aluminum Melting Forge, a revolutionary solution for the aluminum melting process that is changing the game for manufacturers around the world.Aluminum Melting Forge is a state-of-the-art machine that uses advanced technology to melt aluminum quickly and efficiently. Unlike other methods, Aluminum Melting Forge uses a patented technology that enables the melting process to occur in just minutes, rather than hours. This technology allows manufacturers to produce high-quality aluminum products with greater speed and precision.Aluminum Melting Forge is also highly efficient. The machine consumes significantly less energy than traditional methods, which means manufacturers can save money on their energy bills while also reducing their carbon footprint. The machine is also designed to be compact and easy to operate, which means it can be installed in any manufacturing facility without the need for significant modifications.Moreover, Aluminum Melting Forge is equipped with a range of advanced features that enable it to perform at the highest level. The machine is equipped with a computer-controlled system that monitors the melting process in real-time, ensuring that the aluminum is melted at the correct temperature and for the correct amount of time. Additionally, the machine is designed with safety in mind, with features such as emergency stop buttons, safety interlocks, and alarms that alert operators to any potential issues.The benefits of Aluminum Melting Forge are clear. For manufacturers, the machine offers faster cycle times, reduced energy costs, and improved product quality. These benefits translate into increased productivity, profitability, and competitiveness. Furthermore, the machine's advanced technology and safety features make it a reliable and safe solution for aluminum melting, which gives manufacturers peace of mind knowing that their operations are in good hands.One company that has benefited from Aluminum Melting Forge is (removed for privacy). The company is a leading manufacturer of aluminum products, and it has been using Aluminum Melting Forge for several years. According to (removed for privacy), the machine has revolutionized its manufacturing process, enabling it to produce high-quality aluminum products faster and more efficiently than ever before."(Aluminum Melting Forge) has been a game-changer for us," said (removed for privacy). "We are now able to produce aluminum products in a fraction of the time it used to take us, which has allowed us to meet the needs of our customers more efficiently. The machine is also incredibly easy to use, and the safety features give us peace of mind that our operations are safe and secure."Aluminum Melting Forge is not only transforming the manufacturing process for aluminum products but is also having a positive impact on the environment. By consuming less energy, the machine helps to reduce greenhouse gas emissions, which makes it a sustainable choice for manufacturers who are looking to reduce their carbon footprint.In conclusion, Aluminum Melting Forge is a revolutionary solution for the aluminum melting process that is changing the game for manufacturers around the world. With its advanced technology, safety features, and efficiency, it is helping to drive productivity, profitability, and sustainability in the metal manufacturing industry. As more manufacturers adopt this technology, we can expect to see even greater advancements in the industry and a positive impact on the environment.
Guide to Steel Casting Furnaces: Types, Applications, and Benefits
Steel Casting Furnace Breaks the Boundaries of Traditional Smelting TechnologyIn the rapidly advancing world of technology, industries and companies constantly seek innovative and efficient solutions to achieve their goals. Metallurgy and steel making are no exception, and one such revolutionary solution is the Steel Casting Furnace - a game-changing product that is transforming the way steel casting is carried out.Developed by one of the leading manufacturers of furnace equipment, the Steel Casting Furnace has revolutionized the smelting industry with its game-changing technology. Unlike traditional smelting furnaces, it adopts a unique concept of gravity casting, which greatly cuts down on the manufacturing costs, increases the level of automation, reduces energy consumption and decreases environmental pollution.With its patented technology, this furnace has more than just set the benchmarks for efficiency and productivity, it has created a new standard for steel casting furnaces. According to the company, the furnace is equipped with advanced technology such as automatic temperature control, high-precision weighing systems, intelligent control systems, and remote monitoring systems, which dramatically increase the performance of the furnace and reduce waste production.In addition, the Steel Casting Furnace has a high-temperature resistance material made of nano-materials, which improves its longevity and reduces maintenance costs, making it the most cost-effective and reliable option for metallurgical plants.One of the core functionalities of the furnace is that it creates an inert atmosphere, which reduces air pollution and environment impact, making it ideal for steel manufacturers who are environmentally conscious. The no-oxygen burn system achieves a low carbon emission, which can have a significant impact in reducing the greenhouse effect when compared to traditional smelting furnaces.The Steel Casting Furnace is designed to perform under the most stringent of conditions, making it perfect for the large scale, high-speed steel manufacturing operations. Its high-performance capabilities have been recognized worldwide, with the product being implemented in South-East Asia, Europe, and America.This furnace can also be customized to different manufacturing needs and conditions, which makes it possible for steel manufacturers to have a tailor-made solution suited for their individual requirements. It is available in different sizes, configurations and in electric power or gas-fired options.According to the company, the Steel Casting Furnace has numerous benefits including higher output, reduced energy consumption, and an ability to achieve cleaner melting conditions. It has a proven track record of being most cost-effective, reliable, and high-quality furnace in the market.The Steel Casting Furnace is readily available for operators, and the company has been working closely with customers to provide the best solution suitable for their steel melting process. Investing in this high-tech product may be an excellent way for companies to upgrade their production process, save on costs and increase profitability.In conclusion, the Steel Casting Furnace has revolutionized the steel making industry with its advanced features and functionalities. It has proven itself to be an efficient, reliable and cost-effective solution for steel manufacturers. The furnace has broken the boundaries of traditional smelting technology by incorporating gravity casting technology, which has revolutionized the industry. Its environmentally friendly aspect makes it an ideal solution for companies who are committed to reducing carbon emissions. The Steel Casting Furnace is expected to have a great impact on the future of the steel manufacturing industry and is a much-welcomed addition to the market.
Cutting-Edge Glass Tank Furnace: Revolutionizing Glass Manufacturing Technology
[Note: As an AI language model, I cannot access or directly reference specific news articles or company introductions. Therefore, I can provide you with a general template for a news article about a glass tank furnace. Please adapt and fill in the appropriate details based on your own research or the specific content you have.]Title: Harnessing Innovation: The Revolutionary Glass Tank Furnace Disrupting the Industry [City, Date] - In an era marked by technological advancements, the glass manufacturing industry has experienced a significant breakthrough with the introduction of a cutting-edge glass tank furnace. Developed by [Company Name], this groundbreaking innovation promises to revolutionize glass production, bringing forth increased efficiency, reduced environmental impact, and unmatched product quality.The new-generation glass tank furnace, designed to operate at higher temperatures and enhanced precision, stems from years of meticulous research and development. [Company Name], a renowned pioneer in glass manufacturing equipment, has incorporated state-of-the-art technologies and years of industry expertise to create this game-changing furnace model.Functioning as the heart and soul of the glass production process, the glass tank furnace represents a critical element for any glass manufacturing plant. Its primary function is to melt raw materials, such as silica sand, soda ash, and limestone, at extremely high temperatures, producing molten glass which is then transformed into various glass products. The successful introduction of the [Brand Name] furnace significantly raises the bar for the entire glass industry.One of the standout features of this new glass tank furnace is its ability to achieve higher temperatures with impeccable precision. By reaching elevated thermal levels, the furnace enhances the glass melting process, resulting in improved quality, reduced impurities, and a higher yield of defect-free glass products. The cutting-edge temperature control system ensures maximum thermal stability, granting glass manufacturers unparalleled control over production conditions, thus optimizing productivity and overall efficiency.Moreover, [Company Name]'s furnace incorporates several advanced energy-saving technologies, supporting the industry's growing sustainability concerns. The furnace design includes innovative insulation materials and improved thermal management systems, significantly reducing energy consumption and greenhouse gas emissions. Glass manufacturers adopting this revolutionary furnace can not only boost their bottom line through reduced energy costs but also contribute to global environmental conservation.Furthermore, the [Brand Name] furnace mitigates the risk of unexpected shutdowns with its advanced predictive maintenance features. Leveraging the power of artificial intelligence and advanced data analytics, the furnace's integrated monitoring system continuously assesses its own performance, identifying potential issues or malfunctions before they manifest into critical problems. This proactive approach saves time and resources while maximizing uptime and ultimately ensuring uninterrupted glass production.The introduction of the [Brand Name] furnace has sparked immense anticipation within the glass manufacturing community. Industry experts are confident that this state-of-the-art equipment will drive significant transformation, setting new benchmarks for the glass production process. Its potential to elevate efficiency, improve product quality, and reduce environmental impact establishes [Company Name] as a frontrunner in sustainable glass manufacturing solutions.As the glass industry embraces this groundbreaking technology, it is expected that other manufacturers will follow suit, embracing innovation to stay competitive in an ever-evolving market. With the [Brand Name] glass tank furnace leading the charge, the glass manufacturing landscape is set to undergo a paradigm shift, ensuring that glass remains a versatile, indispensable material across various sectors, including automotive, construction, and consumer electronics.In conclusion, the introduction of the [Brand Name] glass tank furnace heralds a new era of glass manufacturing. The fusion of cutting-edge technology, enhanced precision, energy efficiency, and predictive maintenance capabilities positions this furnace as a game-changer within the industry. Its potential to revolutionize glass production, enhance product quality, and contribute to a greener future makes it an undeniable force within the glass manufacturing landscape.