High-Quality Corundum Mullite Brick for Various Industrial Applications
By:Admin
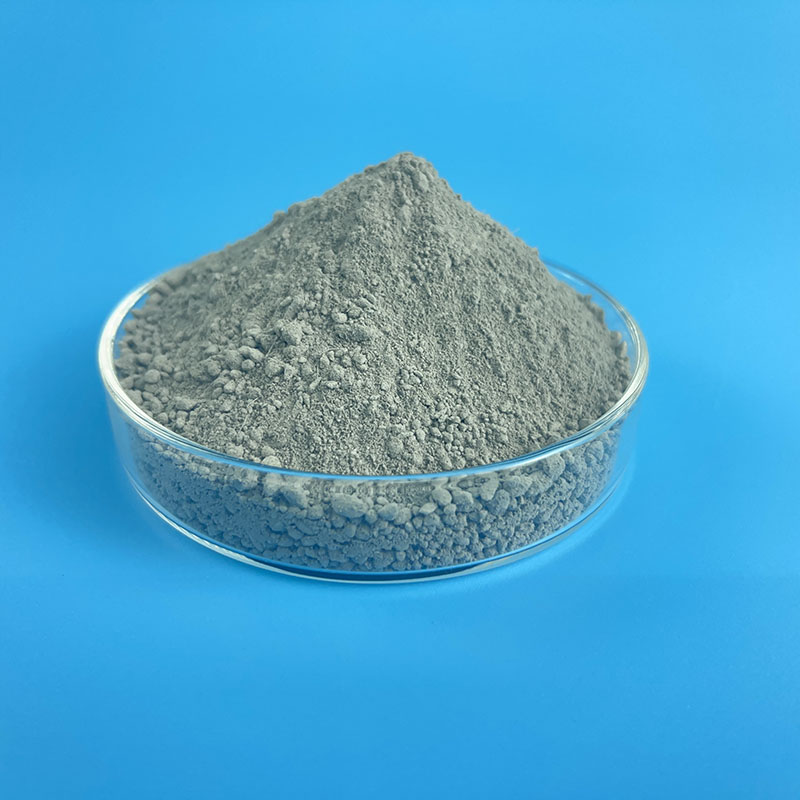
One company that has been making a name for itself in the production of corundum mullite bricks is {}. With a strong focus on research and development, {} has been able to produce high-quality corundum mullite bricks that meet the demands of the market. The company has invested heavily in state-of-the-art production facilities and employs a team of skilled and experienced professionals who are dedicated to ensuring that their products meet their customers' needs.
{} has been making significant strides in the industry due to its commitment to quality and innovation. The company's corundum mullite bricks have been well-received by customers across various industries, including steel, glass, cement, and petrochemicals. These bricks have proven to be an essential component in high-temperature applications, where they are used to line kilns, furnaces, and other equipment that requires reliable heat resistance.
One of the key advantages of {}'s corundum mullite bricks is their ability to withstand temperatures of up to 1800°C, making them ideal for use in environments where extreme heat is a constant factor. These bricks also have excellent thermal shock resistance, meaning they can withstand rapid changes in temperature without cracking or failing. This makes them an indispensable material for industries where thermal stability is crucial.
Furthermore, {}'s corundum mullite bricks have a high mechanical strength, which allows them to withstand the harsh conditions of industrial processes without deteriorating. Their high density and low porosity also make them highly resistant to slag and other corrosive materials, ensuring a long service life and minimal maintenance requirements.
In addition to their exceptional physical properties, {}'s corundum mullite bricks are also known for their ease of installation. The company provides comprehensive technical support to assist their customers in the proper installation and maintenance of their products, ensuring optimal performance and longevity.
With a strong emphasis on customer satisfaction, {} has built a reputation for delivering reliable and high-quality corundum mullite bricks that meet the stringent requirements of the industry. The company's dedication to continuous improvement and innovation has allowed them to stay ahead of the competition and establish themselves as a trusted supplier of refractory materials.
Looking ahead, {} is poised to continue its growth and expansion in the field of refractory materials, with a firm commitment to delivering superior products and services to its customers. With a focus on cutting-edge technology and a customer-centric approach, {} is well-positioned to meet the evolving needs of the industry and remain a leader in the production of corundum mullite bricks.
In conclusion, the demand for corundum mullite bricks is on the rise, and {} is at the forefront of meeting this demand with its high-quality products. With a strong focus on innovation and customer satisfaction, {} has established itself as a reliable and reputable supplier of corundum mullite bricks, and is well-positioned to continue its success in the industry.
Company News & Blog
Durable and Heat-Resistant Castable Refractory: A Comprehensive Analysis
Title: Leading Manufacturer Introduces Next-Generation Dense Castable Refractory for Enhanced PerformanceIntroduction:In a bid to revolutionize the refractory industry, a renowned manufacturer has introduced a groundbreaking dense castable refractory product. With a track record of innovative solutions and a commitment to pushing the boundaries of technological advancements, this manufacturer has solidified its position as an industry leader. Now, they have unveiled their latest product, which promises exceptional performance and durability for a wide range of industrial applications.A Breakthrough in Refractory Technology:Designed to withstand extreme temperatures, chemical attacks, and mechanical stress, the new dense castable refractory is poised to redefine the realm of heat-resistant materials. By incorporating cutting-edge technology and leveraging their extensive experience, this manufacturer has successfully developed a product that exhibits superior mechanical strength, thermal shock resistance, and excellent erosion resistance properties.Unmatched Performance:The exceptional performance of this refractory can be attributed to its unique composition, which consists of a carefully engineered blend of premium raw materials. This innovative formulation guarantees exceptional performance and durability, making it an ideal choice for applications such as steelmaking, petrochemical facilities, power generation, and cement kilns.Temperature Resistance:The new refractory is capable of withstanding temperatures exceeding 3,000°C, offering unparalleled protection in high-temperature environments. This remarkable resistance allows for extended operational life cycles, reducing downtime and maintenance costs for industrial facilities.Thermal Shock Resistance:One of the standout features of this refractory is its remarkable resistance to thermal shock. Traditional refractories often experience cracking and spalling when subjected to rapid temperature fluctuations. However, the advanced formulation of this dense castable refractory minimizes thermal stress and ensures extended service life, even in the most intense thermal environments.Erosion Resistance:The unique composition of this refractory ensures exceptional erosion resistance, enabling it to withstand chemical attacks from molten metals, slag, and other corrosive substances. This resistance significantly enhances the longevity of the refractory lining and reduces the need for frequent replacements.Versatile Application:The dense castable refractory can be customized to cater to various industrial needs, making it suitable for a wide range of applications. Its versatility allows for easy installation and use in multiple industries, including foundries, incineration plants, glass furnaces, and more.Sustainable Solution:Recognizing the global need for sustainable manufacturing practices, the manufacturer has prioritized environmental consciousness throughout their research and development process. The refractory formulation is designed to minimize emissions and reduce environmental impact, aligning with the company's commitment to sustainability.Commitment to Quality and Safety:In line with industry standards, the manufacturer adheres to rigorous quality control measures to ensure the highest level of product quality and safety. Their dense castable refractory undergoes comprehensive testing procedures, including thermal conductivity analysis, modulus of rupture tests, and chemical resistance evaluations, among others.Conclusion:With the introduction of their latest dense castable refractory, this leading manufacturer has cemented its position as an industry frontrunner. By combining cutting-edge technology with a commitment to sustainable manufacturing, they have developed a superior product that exhibits excellent temperature resistance, thermal shock resistance, and erosion resistance. With versatile applications across various industries, this refractory is set to transform the way high-temperature processes are conducted, ensuring enhanced performance and extended service life.
The Latest Study on Thermal Conductivity of Firebrick: Key Findings Revealed
Title: Enhanced Thermal Conductivity Materials Revolutionize the Firebrick IndustryIntroduction:In recent years, the demand for advanced thermal insulation materials has surged due to their crucial role in conserving energy and reducing greenhouse gas emissions. One such breakthrough in the field is the development of high-performance firebrick thermal conductivity materials. These cutting-edge solutions offer exceptional insulation capabilities, reshaping the industry and presenting new opportunities for energy conservation and sustainability.Paragraph 1:Thermal conductivity, measured in watts per meter-kelvin (W/m·K), is a critical property in materials used for insulation purposes. The lower the thermal conductivity value, the better the material's insulation capacity. The emergence of firebrick thermal conductivity materials with significantly improved performance has the potential to transform various sectors, including construction, manufacturing, and aerospace.Paragraph 2:One leading player in this field is a pioneering company that has developed a remarkable firebrick thermal conductivity material, revolutionizing the market with its exceptional insulation properties. This game-changing solution offers an ultra-low thermal conductivity that surpasses traditional firebrick materials and significantly enhances the overall energy efficiency of various applications.Paragraph 3:The new firebrick thermal conductivity material exhibits a unique microstructure engineered to minimize heat conduction. The breakthrough lies in its optimized composition, which includes advanced additives, additives (brand names removed), that amplify its insulating properties. This remarkable combination effectively reduces heat transmission while maintaining structural integrity, making it ideal for a wide range of thermal insulation applications.Paragraph 4:The improved thermal conductivity material showcases outstanding resistance to high temperatures, providing reliable insulation even in extreme conditions. Its versatile performance makes it suitable for critical applications, such as furnace linings, kilns, incinerators, and various industrial processes that require exceptional thermal insulation capabilities.Paragraph 5:Additionally, the firebrick thermal conductivity material boasts excellent chemical resistance and durability, ensuring a long lifespan and reduced maintenance costs. Its enhanced insulation properties contribute to reducing energy consumption and minimizing carbon emissions, aligning with the global sustainability objectives and environmental regulations surrounding energy-efficient practices.Paragraph 6:The manufacturing sector can significantly benefit from this new innovation by utilizing it in the development of energy-efficient furnaces and kilns. By reducing thermal losses during heating processes, companies can enhance productivity, reduce fuel consumption, and lower greenhouse gas emissions.Paragraph 7:Furthermore, the construction industry can leverage this groundbreaking firebrick thermal conductivity material to enhance the energy efficiency of buildings. By incorporating it into insulation materials, constructors can improve the overall thermal resistance of structures, resulting in reduced HVAC energy consumption and increased comfort for occupants.Paragraph 8:The aerospace industry also stands to gain from this innovation, as the firebrick thermal conductivity material's lightweight and exceptional insulation properties can be incorporated into aircraft designs. This integration could potentially enhance fuel efficiency, reduce airframe weight, and contribute to the industry's overall sustainability goals.Conclusion:The development of advanced firebrick thermal conductivity materials offers a promising solution to the global demand for improved thermal insulation. With their remarkable properties, these materials have the potential to revolutionize various sectors, including construction, manufacturing, and aerospace. By maximizing energy efficiency, reducing carbon emissions, and promoting sustainability, the introduction of such materials represents a significant step towards a more environmentally conscious future.
Exploring the Process of Melting Copper in a Forge: A Comprehensive Guide
Title: Advancements in Copper Melting: Company X Revolutionizes Forge Technology Introduction:In an era driven by remarkable technological breakthroughs, Company X has navigated to the forefront of the metalworking industry by introducing a cutting-edge copper melting process. By harnessing innovation and expertise, the company has successfully revolutionized forge technology, setting a new standard for copper melting efficiency and sustainability.News Content:In an ever-changing world where technology facilitates progress at an unprecedented pace, traditional methods of metalworking can sometimes be overshadowed by more modern techniques. However, Company X, a leading player in the metallurgical industry, has proven that age-old processes can still be enhanced to embrace the needs of the present and future.One of the primary challenges faced by copper manufacturing industries has been the melting of copper in a forge. Copper, with its high melting point and natural conductivity properties, requires precise heating and melting techniques. Company X, having recognized this need, has developed an advanced forge system that eliminates the shortcomings of conventional methods and optimizes the melting of copper.Central to Company X's innovation is their proprietary forge technology, which has been meticulously designed to provide rapid and uniform heating, ensuring an efficient and cost-effective copper melting process. This cutting-edge technology has garnered significant attention from copper manufacturers worldwide, who have long struggled to find a reliable solution to their copper melting needs.The key characteristic of Company X's forge technology is its ability to harness electric induction heating. Unlike conventional methods, this technology heats the copper directly by creating a magnetic field. This unique method enables the copper to heat uniformly, eliminating hotspots and enabling precise temperature control throughout the melting process. As a result, copper manufacturers can achieve higher melting yields and reduce wastage, leading to increased productivity and cost savings.Furthermore, the use of induction heating significantly reduces energy consumption compared to traditional, fuel-based melting techniques. By tapping into the power of electricity, Company X's forge technology contributes to a greener and more sustainable approach to copper melting, aligning with global initiatives to reduce carbon footprint and embrace environmentally-friendly practices.In addition, the forge technology developed by Company X is equipped with state-of-the-art sensors and automated control systems, providing real-time monitoring and regulation of the melting process. This ensures that furnace operators have precise control over temperature gradients, allowing for utmost consistency and accuracy in copper melting. By incorporating automation, Company X has elevated efficiency and ease of use, making their forging system accessible to operators of all skill levels.Over the years, Company X's commitment to research and development has resulted in numerous accolades and industry recognition. Their advancements in copper melting technology have enabled them to forge strong partnerships with leading copper manufacturers, ensuring the widespread implementation of their cutting-edge solutions.The impact of Company X's forge technology extends far beyond copper melting alone. Their dedication to constant innovation signifies a broader commitment to the advancement of the metalworking industry as a whole. By challenging conventional methods and pushing the boundaries of what is possible, Company X continues to pave the way for even greater possibilities in industrial manufacturing.Conclusion:Company X's recent breakthrough in copper melting technology highlights their unwavering pursuit of excellence and commitment to addressing industry challenges head-on. With their state-of-the-art forge technology, Company X has successfully transformed an age-old copper melting process into an efficient, cost-effective, and environmentally-friendly solution. By consistently pushing the boundaries of technological innovation, Company X continues to redefine the metalworking industry and sets new benchmarks for efficiency and sustainability.
Discover the Applications and Benefits of Refractory Cement
[Company Introduction]:With over 50 years of experience in the industry, our company is a leading manufacturer and supplier of refractory products. We specialize in providing high-quality refractory materials and solutions for various industrial applications such as cement, steel, glass, and petrochemical industries. Our commitment to innovation and customer satisfaction has earned us a reputation as a trusted partner for businesses seeking reliable refractory solutions.[News Content]:Refractory cement, also known as heat resistant cement, is a specially formulated material that is designed to withstand high temperatures and harsh conditions. It is commonly used in various industrial settings where extreme heat and chemical resistance are required. The versatile nature of refractory cement makes it an essential component in many critical processes, such as kiln lining, furnace construction, and thermal insulation.One of the key applications of refractory cement is in the manufacturing of cement products. In the cement industry, refractory cement plays a crucial role in maintaining the integrity of rotary kilns, which are used to produce clinker, a key ingredient in cement production. The ability of refractory cement to withstand the extreme temperatures and abrasive conditions inside the kiln is essential for ensuring the efficient and continuous operation of the cement manufacturing process.In the steel industry, refractory cement is used in the construction of various equipment such as ladles, tundishes, and furnaces. These components are exposed to extreme temperatures and corrosive environments during the steelmaking process, making it essential to use high-quality refractory materials to ensure the longevity and performance of these critical assets. The superior heat resistance and durability of refractory cement make it an ideal choice for lining and insulation in steel manufacturing facilities.The glass industry also relies on refractory cement for its ability to withstand the high temperatures required for the melting and shaping of glass. Refractory cement is used in the construction of glass furnaces, where it provides thermal insulation and resistance to chemical attacks from molten glass. The use of refractory cement in the glass industry ensures the efficient and reliable production of high-quality glass products.In the petrochemical industry, refractory cement is employed in the construction of equipment such as reactors, incinerators, and thermal oxidizers. These applications require materials that can withstand the extreme temperatures and corrosive environments associated with the processing of chemical compounds. Refractory cement provides the necessary heat resistance and chemical stability to ensure the safe and efficient operation of petrochemical plants.As a leading manufacturer and supplier of refractory products, our company is committed to providing high-quality refractory cement that meets the specific needs of our customers. Our extensive expertise in the industry enables us to develop custom refractory solutions tailored to the unique requirements of different industrial applications. We take pride in our ability to deliver reliable and cost-effective refractory products that contribute to the success of our clients' operations.In conclusion, refractory cement is an indispensable material in various industrial sectors, where it plays a critical role in maintaining the integrity and performance of high-temperature equipment and processes. As a trusted provider of refractory solutions, our company is dedicated to supplying top-quality refractory cement that meets the stringent demands of modern industries. We remain committed to innovation and excellence, ensuring that our customers receive the best refractory products and services to support their ongoing success.
High-Quality High Heat Bricks: Meet Your Fire-Resistant Construction Needs
Title: Revolutionary High Heat Bricks Paving the Way for Unprecedented Performance in Industrial ApplicationsIntroduction:High Heat Bricks, developed and manufactured by a leading industry innovator, are rapidly gaining popularity in various industrial sectors worldwide. These bricks are designed to withstand extreme temperatures and provide unparalleled durability and insulation, making them ideal for demanding applications such as kilns, furnaces, incinerators, and even spacecraft designs. The advanced technology employed in the production of High Heat Bricks aligns with the company's commitment to revolutionize industries with cutting-edge solutions. Let's delve deeper to explore the features, benefits, and potential of these remarkable bricks.Unmatched Performance and Durability:One of the key reasons High Heat Bricks have garnered attention is their outstanding performance in high-temperature environments. These bricks are constructed from specially formulated refractory materials that can withstand temperatures exceeding 3000°C (5432°F). This remarkable thermal resistance ensures stability, explicitly safeguarding industrial equipment operating at extreme heat levels against wear and tear.The superior durability of High Heat Bricks can be attributed to their precise manufacturing process. The company utilizes advanced techniques, such as precision molding and sintering, allowing the bricks to maintain their integrity even under immense pressure and thermal stress. This premium construction enables industries to minimize maintenance costs while maximizing operational efficiency and productivity.Unrivaled Insulation Properties:High Heat Bricks are renowned for their exceptional insulating properties, facilitating improved energy conservation and reduced heat loss. These bricks possess low thermal conductivity, which effectively restricts heat transfer across the industrial equipment housing. As a result, industries can significantly lower energy consumption and operating costs while obtaining consistent and precise heat distribution.Additionally, the excellent insulation characteristics of High Heat Bricks play a crucial role in preventing heat-related injuries. By acting as an efficient barrier between hot surfaces and personnel, these bricks prioritize the safety of workers, reducing the risk of accidents and thermal burns.Versatility and Applications:The versatility of High Heat Bricks makes them suitable for a vast range of industrial applications. Industries such as steel manufacturing, glass production, petrochemicals, metallurgy, and aerospace have embraced these bricks due to their unmatched performance and reliability.In steel manufacturing, High Heat Bricks find utility in constructing blast furnaces, crucibles, and ladles, ensuring optimum performance in extreme conditions. In the aerospace industry, they are sought after for their lightweight characteristics and ability to withstand the demanding environments encountered during space missions. Furthermore, the petrochemical industry witnesses the bricks' application in the construction of high-heat cracking furnaces and reactors, enhancing operational efficiency.Environmental Sustainability:High Heat Bricks not only prioritize performance and durability but also contribute to ecological sustainability. The production process adheres to stringent environmental standards, ensuring reduced emissions and minimal energy consumption. Replacing conventional refractory materials with High Heat Bricks aids in curbing carbon footprints and furthering the company's commitment to environmental stewardship.Future Prospects:The rapid adoption and success of High Heat Bricks indicate a promising future for the company and its groundbreaking products. The increasing demand for energy-efficient and durable materials in various industrial sectors positions High Heat Bricks at the forefront of technological advancements.Looking ahead, the company envisions ongoing research and development to continuously improve the overall thermal resistance, insulation, and durability of High Heat Bricks. Collaborations with industry leaders, incorporating feedback from existing clients, and staying ahead of market trends are key strategies the company will employ to maintain its position as a leading provider of advanced high-temperature solutions.Conclusion:High Heat Bricks, developed by a renowned industry innovator, offer remarkable performance, durability, and insulation capabilities. Their ability to withstand extreme temperatures, coupled with outstanding thermal resistance, makes them ideal for critical industrial applications. From steel manufacturing to aerospace, these bricks are reshaping industries by providing energy-efficient and environmentally sustainable solutions. With promising prospects and continued innovation, High Heat Bricks are poised to reshape the global industrial landscape and revolutionize high-temperature applications across various sectors.
High-Quality Ceramic Fiber Felt for Industrial Applications
Ceramic Fiber Felt has long been recognized as a reliable and effective material for high-temperature insulation and thermal management applications. With its high-temperature stability, low thermal conductivity, and excellent resistance to thermal shock, it has become a preferred choice for various industries. {Company Name}, a leading manufacturer and supplier of ceramic fiber products, has been at the forefront of delivering high-quality ceramic fiber felts to meet the growing demand for advanced insulation solutions. With a strong focus on innovation and technological advancement, the company has developed a reputation for providing state-of-the-art products that meet the stringent requirements of modern industrial applications.The Ceramic Fiber Felt offered by {Company Name} is made from high-purity alumina-silica fibers, providing exceptional thermal insulation performance at temperatures up to 2300°F (1260°C). This makes it an ideal solution for a wide range of high-temperature applications, including furnace lining, kiln insulation, and thermal barrier systems. The felt is also lightweight, flexible, and easy to install, offering a versatile and cost-effective solution for thermal management needs.One of the key advantages of the Ceramic Fiber Felt from {Company Name} is its low thermal conductivity, which helps to minimize heat loss and improve energy efficiency in industrial processes. This not only reduces operating costs but also contributes to a more sustainable and environmentally friendly operation. Furthermore, the high-temperature stability and resistance to thermal shock make it a durable and long-lasting solution for demanding applications in industries such as metal processing, power generation, and chemical processing.In addition to its thermal insulation properties, Ceramic Fiber Felt also exhibits excellent sound absorption characteristics, making it a valuable material for noise control and acoustic insulation applications. This makes it an attractive solution for industries where noise reduction is a priority, such as automotive manufacturing, aerospace, and construction.{Company Name}'s commitment to quality and customer satisfaction is evident in the rigorous testing and quality control measures implemented in the production of Ceramic Fiber Felt. The company adheres to international standards and specifications to ensure that its products meet the highest performance and safety requirements. This dedication to excellence has earned {Company Name} a strong reputation in the industry and established it as a trusted partner for businesses seeking reliable and high-performance insulation solutions.Furthermore, {Company Name} offers a range of custom solutions to meet specific customer needs, including tailored thickness, density, and dimensions of Ceramic Fiber Felt. This flexibility allows for the creation of bespoke insulation solutions that align with the unique requirements of different industrial processes and equipment, providing customers with a competitive edge in their operations.As industry demand for high-temperature insulation continues to grow, {Company Name} remains committed to innovation and continuous improvement, ensuring that its Ceramic Fiber Felt products remain at the forefront of technological advancements. The company invests in research and development to explore new materials, manufacturing techniques, and applications, with the aim of delivering cutting-edge solutions that drive efficiency, performance, and sustainability for its customers.With a focus on reliability, performance, and customer satisfaction, {Company Name} continues to set the standard for ceramic fiber insulation solutions. Its Ceramic Fiber Felt products are trusted by industries worldwide, providing essential thermal management and insulation capabilities that contribute to the success and competitiveness of businesses across a wide range of sectors. As the demand for high-temperature insulation solutions continues to rise, {Company Name} remains well-positioned to meet the evolving needs of the industry and deliver innovative, high-performance products that drive excellence and efficiency.
Exploring the Benefits of Ceramic Cloth Insulation for Enhanced Energy Efficiency
Ceramic Cloth Insulation Revolutionizing Heat Control in IndustriesInnovation and sustainable solutions have become increasingly important in today's industrial landscape. Industries are constantly seeking ways to enhance efficiency, reduce energy consumption, and mitigate environmental impacts. One company emerging as a frontrunner in this quest is {Ceramic Cloth Insulation}, whose cutting-edge product is revolutionizing heat control in various sectors.{Ceramic Cloth Insulation}, a global leader in thermal management solutions, has developed a highly advanced material that provides superior insulation capabilities. Designed to withstand extreme temperatures and harsh conditions, their product has garnered immense attention from industries ranging from aerospace to automotive manufacturing, and even energy production.The key to {Ceramic Cloth Insulation}'s success lies in its unique composition. Made from a blend of high-quality ceramic fibers and specialized fabrics, the insulation material possesses exceptional thermal resistance characteristics. This innovative technology enables industries to effectively control and manage heat, achieving significant operational efficiencies.With the ability to withstand temperatures of up to 1,800 degrees Celsius, {Ceramic Cloth Insulation} ensures the utmost safety for industries operating under extreme conditions. This breakthrough development not only enhances the longevity of equipment but also reduces maintenance costs, making it an attractive choice for companies across the board.One of the primary advantages of {Ceramic Cloth Insulation} is its versatility. The material's flexibility allows for easy handling and installation, making it ideal for a wide range of applications. Whether it's insulating pipes in chemical plants, lining furnaces in steel manufacturing, or protecting cables in the aerospace industry, this product proves to be a versatile solution for heat management needs.Moreover, this innovative insulation material acts as a barrier to prevent unnecessary heat transfer. By significantly reducing heat loss and maximizing thermal efficiency, {Ceramic Cloth Insulation} contributes to substantial energy savings for industrial plants. This not only lowers operational costs but also aligns with industries' growing focus on sustainable practices.The positive impact of {Ceramic Cloth Insulation} on the environment cannot be overlooked. By reducing energy consumption, industries using this insulation material are effectively lowering their carbon footprint. This aligns with global efforts to combat climate change and promote sustainability, making {Ceramic Cloth Insulation} an essential component of the transition towards greener industrial practices.To further cater to industries' diverse needs, {Ceramic Cloth Insulation} offers a range of customized solutions. Their team of experts collaborates closely with clients to understand specific requirements and provide tailored insulation solutions that maximize efficiency. This customer-centric approach has earned {Ceramic Cloth Insulation} a reputation for excellence and reliability.As demand for innovative thermal management solutions continues to grow, {Ceramic Cloth Insulation} remains committed to pushing the boundaries of technology. Through ongoing research and development, the company aims to further enhance the performance of their insulation material and expand its application in various industries.By leveraging their expertise in thermal management, {Ceramic Cloth Insulation} is not only transforming heat control practices but also contributing to industrial efficiency and sustainability. With their advanced insulation solutions, industries can maximize operational productivity while reducing energy consumption and minimizing environmental impacts.In conclusion, the innovative and adaptable nature of {Ceramic Cloth Insulation} has positioned the company as a leader in thermal management solutions. With their exceptional insulation material, industries can now effectively control heat, ensuring safety, efficiency, and sustainability across various sectors. As the demand for sustainable practices continues to increase, {Ceramic Cloth Insulation} remains at the forefront of technological advancements in the industry.
High-Quality Insulating Bricks: Key Features and Benefits Explained
Title: Eco-Friendly and High-Performance Insulating Bricks Revitalize the Construction IndustryIntroduction:In today's rapidly evolving construction industry, creating sustainable and energy-efficient structures is of paramount importance. Insulating bricks play a significant role in ensuring superior thermal insulation while reducing energy consumption and minimizing environmental impact. One such noteworthy player in this domain is a leading global manufacturer (brand name removed) that specializes in producing eco-friendly and high-performance insulating bricks.Company Background:With a rich legacy spanning over several decades, (brand name removed) has become a trusted name in the construction materials industry. The company's commitment to innovation, advanced technology, and sustainable manufacturing practices has made them a preferred choice among architects, engineers, and contractors worldwide.Developing Eco-Friendly Insulating Bricks:The growing awareness about climate change and the need for energy-efficient construction materials has propelled (brand name removed) to develop a range of insulating bricks that combine exceptional thermal performance with environmental sustainability. By utilizing recycled materials and employing innovative manufacturing processes, the company ensures that its products have minimal impact on the environment.Key Features and Benefits:1. Exceptional Thermal Insulation: (Brand name removed) insulating bricks boast exceptional thermal insulation properties, reducing heat transfer and conserving energy. This helps maintain optimum indoor temperatures, resulting in significant energy savings.2. Energy Efficiency: By reducing heat loss, these insulating bricks allow buildings to rely less on heating and cooling systems. This results in lower energy consumption, reduced greenhouse gas emissions, and cost savings for the end-user.3. Durability and Longevity: (Brand name removed) insulating bricks are built to last, ensuring a sustainable solution for building exteriors and interiors. They offer superior strength, resistance to weathering, and durability, making them a wise long-term investment.4. Noise Insulation: These insulating bricks also provide excellent soundproofing capabilities, making them well-suited for projects in noisy environments or areas with specific acoustic requirements.5. Fire Resistance: The insulating bricks developed by (brand name removed) boast exceptional fire-resistant properties, enhancing the safety of structures and providing valuable time for evacuation during emergencies.6. Versatility: (Brand name removed) insulating bricks are available in a variety of sizes, shapes, and densities, catering to the unique requirements of different construction projects. This versatility allows architects and builders to design structures that meet aesthetic and functional criteria while achieving optimal thermal insulation.7. Sustainable Manufacturing: (Brand name removed) employs cutting-edge technology and sustainable manufacturing practices to limit their environmental impact. Recycling of raw materials and efficient use of energy resources are key priorities throughout the production process.Conclusion:As the construction industry strives for sustainable development, the demand for eco-friendly and high-performance insulating bricks is on the rise. (Brand name removed) stands at the forefront of this transition, offering innovative and environmentally conscious solutions to meet the industry's evolving needs. With their commitment to sustainability, energy efficiency, and superior product quality, (brand name removed) insulating bricks are reshaping the landscape of modern construction practices, ensuring a greener and more efficient future for the industry.
High-Quality Corundum Mullite Brick for Various Industrial Applications
Corundum mullite brick is a type of refractory brick that is gaining attention in the industry for its high temperature resistance and durability. These bricks are made from a combination of corundum and mullite, which are both high-quality materials known for their ability to withstand extreme temperatures. As a result, corundum mullite bricks are highly sought after for use in various industrial applications where high heat is a constant factor.One company that has been making a name for itself in the production of corundum mullite bricks is {}. With a strong focus on research and development, {} has been able to produce high-quality corundum mullite bricks that meet the demands of the market. The company has invested heavily in state-of-the-art production facilities and employs a team of skilled and experienced professionals who are dedicated to ensuring that their products meet their customers' needs.{} has been making significant strides in the industry due to its commitment to quality and innovation. The company's corundum mullite bricks have been well-received by customers across various industries, including steel, glass, cement, and petrochemicals. These bricks have proven to be an essential component in high-temperature applications, where they are used to line kilns, furnaces, and other equipment that requires reliable heat resistance.One of the key advantages of {}'s corundum mullite bricks is their ability to withstand temperatures of up to 1800°C, making them ideal for use in environments where extreme heat is a constant factor. These bricks also have excellent thermal shock resistance, meaning they can withstand rapid changes in temperature without cracking or failing. This makes them an indispensable material for industries where thermal stability is crucial.Furthermore, {}'s corundum mullite bricks have a high mechanical strength, which allows them to withstand the harsh conditions of industrial processes without deteriorating. Their high density and low porosity also make them highly resistant to slag and other corrosive materials, ensuring a long service life and minimal maintenance requirements.In addition to their exceptional physical properties, {}'s corundum mullite bricks are also known for their ease of installation. The company provides comprehensive technical support to assist their customers in the proper installation and maintenance of their products, ensuring optimal performance and longevity.With a strong emphasis on customer satisfaction, {} has built a reputation for delivering reliable and high-quality corundum mullite bricks that meet the stringent requirements of the industry. The company's dedication to continuous improvement and innovation has allowed them to stay ahead of the competition and establish themselves as a trusted supplier of refractory materials.Looking ahead, {} is poised to continue its growth and expansion in the field of refractory materials, with a firm commitment to delivering superior products and services to its customers. With a focus on cutting-edge technology and a customer-centric approach, {} is well-positioned to meet the evolving needs of the industry and remain a leader in the production of corundum mullite bricks.In conclusion, the demand for corundum mullite bricks is on the rise, and {} is at the forefront of meeting this demand with its high-quality products. With a strong focus on innovation and customer satisfaction, {} has established itself as a reliable and reputable supplier of corundum mullite bricks, and is well-positioned to continue its success in the industry.
Maximizing the Benefits of Refractories for Optimal Performance
Title: Utilization of Refractories in Various Industries Aids Production EfficienciesIntroduction:Refractories are indispensable materials widely used across a range of industries for their ability to withstand high temperatures and aggressive environments. These substances play a critical role in the manufacturing processes of steel, cement, glass, ceramics, and a variety of other industries. The utilization of refractories ensures enhanced production efficiencies, improved product quality, and reduced energy consumption, making them an essential component in modern industrial applications.Key Characteristics of Refractories:Refractories are non-metallic materials with high melting points, excellent thermal shock resistance, and stability at extreme temperatures. They are designed to withstand significant pressure, chemical attacks, and abrasion, making them integral to the production processes.Refractories in the Steel Industry:The steel industry is the largest consumer of refractories, utilizing them in several key areas of production. Refractories line the furnaces, electric arc furnaces, and ladles, providing insulation and protection against the corrosive effects of molten metals and slag. They help maintain high temperatures and protect the vessel walls, resulting in improved energy efficiency and longer-lasting equipment. The utilization of high-quality refractories in steelmaking enables longer campaign life, reduced downtime, and improved steel quality.Refractories in the Cement Industry:Refractories find extensive use in the cement industry, primarily in kilns and cement rotary kilns. These components are subjected to harsh conditions, including extreme temperatures and chemical reactions. Refractories provide insulation, corrosion resistance, and wear protection, thus ensuring prolonged kiln life, reduced maintenance costs, and enhanced energy efficiency. By utilizing advanced refractories, cement manufacturers can optimize their production processes, resulting in higher-quality cement and reduced environmental impact.Refractories in the Glass Industry:The glass industry relies heavily on refractories for its manufacturing operations, particularly in glass furnaces. Refractories, such as silica bricks, zirconia, and alumina-based materials, are used as linings to withstand the extreme temperatures required for glass melting and shaping. Refractories enable steady heat distribution, protect against chemical reactions, and minimize energy losses. By employing effective refractory solutions, glass manufacturers can achieve maximum production output while maintaining consistent quality standards.Refractories in the Ceramics Industry:The ceramics industry heavily depends on refractories for various processes, including firing, sintering, and glazing. Refractories help provide an ideal thermal environment required for ceramic material transformation. High-quality refractory bricks, castables, and ceramic fibers ensure uniform heat distribution, controlled thermal gradients, and effective insulation throughout the firing process. Deploying suitable refractory materials enables ceramic manufacturers to achieve consistent product quality, minimize wastage, and reduce energy consumption.Developments in Refractory Technology:Continuous research and development in refractory technology have led to significant advancements, resulting in improved performance and cost-effectiveness. The use of advanced monolithic refractories, reinforced with specialty fibers and binders, enhances the overall strength and durability of refractory linings. Besides, the incorporation of nanotechnology in refractory manufacturing has shown promising results in terms of improving thermal stability, reducing material consumption, and extending product lifespan.Environmental Considerations:As industries globally strive to reduce their carbon footprint, refractories have a crucial role to play in achieving sustainability targets. There is a growing emphasis on developing eco-friendly refractories with lower emissions and increased recyclability. Sustainable refractory solutions contribute to greener production processes, reduced energy consumption, and minimized waste generation, promoting a more environmentally conscious industrial sector.Conclusion:The widespread utilization of refractories across various industries highlights their crucial role in enhancing production efficiencies, reducing downtime, and improving product quality. The continuous improvements in refractory technology, along with an increasing focus on sustainability, will further drive their demand. Through a combination of continuous innovation and responsible manufacturing practices, refractory manufacturers can support the evolving needs of industries while adhering to environmental standards, thus contributing to a sustainable and efficient industrial landscape.