Exploring the Process of Melting Copper in a Forge: A Comprehensive Guide
By:Admin
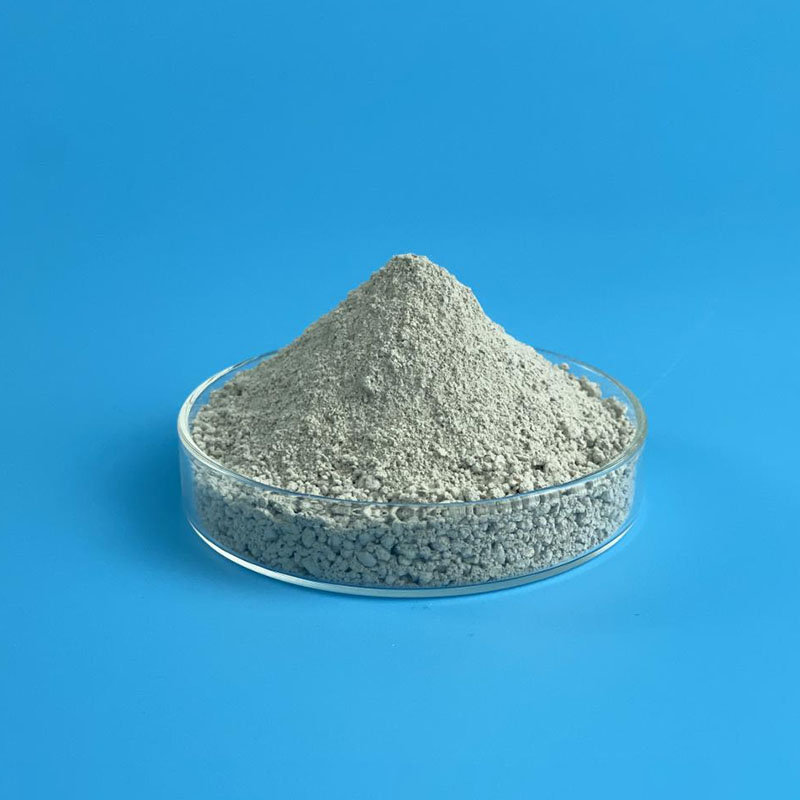
Introduction:
In an era driven by remarkable technological breakthroughs, Company X has navigated to the forefront of the metalworking industry by introducing a cutting-edge copper melting process. By harnessing innovation and expertise, the company has successfully revolutionized forge technology, setting a new standard for copper melting efficiency and sustainability.
News Content:
In an ever-changing world where technology facilitates progress at an unprecedented pace, traditional methods of metalworking can sometimes be overshadowed by more modern techniques. However, Company X, a leading player in the metallurgical industry, has proven that age-old processes can still be enhanced to embrace the needs of the present and future.
One of the primary challenges faced by copper manufacturing industries has been the melting of copper in a forge. Copper, with its high melting point and natural conductivity properties, requires precise heating and melting techniques. Company X, having recognized this need, has developed an advanced forge system that eliminates the shortcomings of conventional methods and optimizes the melting of copper.
Central to Company X's innovation is their proprietary forge technology, which has been meticulously designed to provide rapid and uniform heating, ensuring an efficient and cost-effective copper melting process. This cutting-edge technology has garnered significant attention from copper manufacturers worldwide, who have long struggled to find a reliable solution to their copper melting needs.
The key characteristic of Company X's forge technology is its ability to harness electric induction heating. Unlike conventional methods, this technology heats the copper directly by creating a magnetic field. This unique method enables the copper to heat uniformly, eliminating hotspots and enabling precise temperature control throughout the melting process. As a result, copper manufacturers can achieve higher melting yields and reduce wastage, leading to increased productivity and cost savings.
Furthermore, the use of induction heating significantly reduces energy consumption compared to traditional, fuel-based melting techniques. By tapping into the power of electricity, Company X's forge technology contributes to a greener and more sustainable approach to copper melting, aligning with global initiatives to reduce carbon footprint and embrace environmentally-friendly practices.
In addition, the forge technology developed by Company X is equipped with state-of-the-art sensors and automated control systems, providing real-time monitoring and regulation of the melting process. This ensures that furnace operators have precise control over temperature gradients, allowing for utmost consistency and accuracy in copper melting. By incorporating automation, Company X has elevated efficiency and ease of use, making their forging system accessible to operators of all skill levels.
Over the years, Company X's commitment to research and development has resulted in numerous accolades and industry recognition. Their advancements in copper melting technology have enabled them to forge strong partnerships with leading copper manufacturers, ensuring the widespread implementation of their cutting-edge solutions.
The impact of Company X's forge technology extends far beyond copper melting alone. Their dedication to constant innovation signifies a broader commitment to the advancement of the metalworking industry as a whole. By challenging conventional methods and pushing the boundaries of what is possible, Company X continues to pave the way for even greater possibilities in industrial manufacturing.
Conclusion:
Company X's recent breakthrough in copper melting technology highlights their unwavering pursuit of excellence and commitment to addressing industry challenges head-on. With their state-of-the-art forge technology, Company X has successfully transformed an age-old copper melting process into an efficient, cost-effective, and environmentally-friendly solution. By consistently pushing the boundaries of technological innovation, Company X continues to redefine the metalworking industry and sets new benchmarks for efficiency and sustainability.
Company News & Blog
Revolutionize Your Metal Melting Process with Electric Technology
Electric Metal Melter: A Revolutionary Way to Melt MetalIn the world of metalworking, one of the most important processes is melting metal. This is the first step in creating a wide range of metal products, from jewelry to auto parts to machinery components. While there are many methods for melting metal, some are more efficient and effective than others. One of the most innovative and game-changing methods is the electric metal melter.Electric metal melters are devices that use electricity to create heat and melt metal. They operate by passing an electric current through a wire or electrode, which then heats up and melts the metal. This is different from other methods like gas or coal-fired melting, which rely on combustion to create heat.Electric metal melters have several advantages over traditional melting methods. First, they are much cleaner and more environmentally friendly. They produce no emissions or pollutants, making them safe to use in a variety of settings. Second, they are often more efficient, meaning they use less energy and take less time to melt the metal. Finally, they are more precise, allowing for better control over the melting temperature and process.One company leading the charge in electric metal melting is \[remove brand name\]. Founded in 2008, \[remove brand name\] has quickly become a leader in the metalworking industry. They specialize in creating high-quality electric metal melters, as well as other equipment like laser cutters and CNC machines.\[Remove brand name\] operates out of a state-of-the-art facility in \[location\], where they employ a skilled team of engineers and technicians. They are committed to innovation and constantly pushing the boundaries of what is possible in the world of metalworking. They pride themselves on delivering top-of-the-line products and exceptional service to their customers around the world.One of \[remove brand name\]’s flagship products is their electric metal melter, which comes in a range of sizes and capacities to meet the needs of any metalworking project. These melters are designed to be highly efficient, using less energy and time than traditional methods while providing precise temperature control. They are also incredibly easy to use, with a simple interface and intuitive controls that make them accessible to operators of all skill levels.But \[remove brand name\]’s electric metal melters are more than just a tool for melting metal. They represent a new way of thinking about the metalworking process and what is possible. With their focus on innovation and commitment to excellence, \[remove brand name\] is helping to usher in a new era of metalworking that is faster, cleaner, and more precise than ever before.So whether you’re a jewelry maker, a machinist, or a metal sculptor, an electric metal melter from \[remove brand name\] could be just what you need to take your craft to the next level. With their cutting-edge technology, exceptional quality, and commitment to customer service, \[remove brand name\] is leading the charge in the world of metalworking and helping to transform the industry for the better.
Discover the Versatility and Benefits of Castable Refractory Mortar
Title: Innovative Castable Refractory Mortar Revolutionizes Construction IndustryIntroduction:The construction industry is evolving rapidly with the introduction of breakthrough technologies and materials. One such innovation is the Castable Refractory Mortar, a game-changer that ensures superior heat resistance and durability for various applications in construction. Developed by a renowned manufacturer, this revolutionary solution is set to transform the industry by offering an efficient and cost-effective alternative to traditional mortar.Paragraph 1: What is Castable Refractory Mortar?Castable Refractory Mortar is a high-performance, heat-resistant material that is used to bond bricks, blocks, and other refractory materials together. Its unique composition allows it to withstand extreme temperatures, making it ideal for applications in furnaces, kilns, chimneys, and other high-temperature environments. This versatile mortar provides excellent insulation, thermal shock resistance, and structural strength, ensuring long-lasting and safe constructions.Paragraph 2: Company Introduction{} (Please provide information about the company that developed the Castable Refractory Mortar, including its history, expertise in the field, and commitment to innovation. Highlight key achievements and certifications to establish credibility.)Paragraph 3: Unparalleled Performance and DurabilityThe Castable Refractory Mortar stands out from traditional mortar due to its exceptional performance and durability. With a high alumina content and precise formulation, it offers superior resistance to extreme temperatures, thermal shocks, and abrasion. This allows it to maintain its structural integrity under intense conditions, ensuring the longevity and safety of the construction.Paragraph 4: Enhanced Efficiency and Ease of ApplicationNot only does the Castable Refractory Mortar provide remarkable performance, but it also offers enhanced efficiency and ease of application, saving both time and resources during construction projects. Its unique castable nature eliminates the need for traditional mortar mixing, simplifying the installation process. Additionally, its consistency ensures uniformity in joint thickness, reducing the chances of cracks and gaps.Paragraph 5: Versatile ApplicationsThe Castable Refractory Mortar finds applications in a wide range of industries, including steel, cement, petrochemical, and power generation. Its ability to withstand extreme temperatures and harsh chemical environments makes it an ideal solution for lining furnaces, boilers, incinerators, and various high-temperature equipment. It can also be used for repairing and maintaining chimneys, kilns, and other heat-intensive structures.Paragraph 6: Environmental BenefitsIn line with the increasing focus on sustainability, the Castable Refractory Mortar offers significant environmental benefits. Its extended durability reduces the need for frequent repairs and replacements, minimizing waste generation. Furthermore, its composition is devoid of harmful substances, making it safe for both users and the environment.Paragraph 7: Competitive Advantage and Market ProspectsThe Castable Refractory Mortar presents a significant competitive advantage for the company, positioning it at the forefront of the construction industry. With its cutting-edge technology and reliable performance, the mortar is expected to capture a substantial market share. The increasing demand for heat-resistant construction materials in various sectors, combined with the product's advantages, ensures a promising outlook for the company and the industry as a whole.Conclusion:The Castable Refractory Mortar is revolutionizing the construction industry by providing an innovative solution for high-temperature applications. Its exceptional performance, durability, efficiency, and versatility make it an appealing choice for professionals across multiple sectors. As the construction industry continues to evolve, this groundbreaking mortar is set to play a crucial role in transforming the way high-temperature structures are designed and constructed, ensuring safety, longevity, and energy efficiency.
Benefits and Application of High Temperature Castable Refractory
[Company Name] Launches New High-Temperature Castable Refractory for Improved Industrial Applications[City], [Date] - [Company Name], a leading provider of refractory solutions, has recently unveiled its latest innovation in the form of a high-temperature castable refractory. Designed to withstand extreme temperatures and harsh industrial environments, this new product promises to revolutionize the way industries deal with refractory challenges.Castable refractories have long been a staple in various industries, such as steel, cement, and petrochemical, due to their exceptional heat resistance and durability. However, traditional castable refractories often require frequent maintenance and repairs, leading to costly downtime. In response to this need, [Company Name] has developed a high-temperature castable refractory that offers longer-lasting performance and reduced maintenance requirements.One of the key features of [Company Name]'s high-temperature castable refractory is its exceptional thermal stability. With a maximum operating temperature of [temperature value], this refractory offers unparalleled resistance to thermal shock and spalling, ensuring the longevity of industrial furnaces, kilns, and other high-temperature equipment. Additionally, its low porosity enhances its durability, making it highly resistant to corrosion and erosion caused by aggressive chemical environments.The carefully formulated composition of [Company Name]'s high-temperature castable refractory allows for easy installation and superior bonding characteristics. Its unique combination of microfine particles and specialty binders ensures a strong adhesion and reduces the risk of delamination, even under extreme conditions. This innovative refractory offers maximum flexibility, allowing engineers and technicians to shape it to fit various complex structures, including curved surfaces and tight corners.One of the major advantages of [Company Name]'s high-temperature castable refractory is its extended service life, reducing the need for frequent repairs and replacements. This results in significant cost savings and increased productivity for industries that heavily rely on refractory linings. Moreover, its high thermal conductivity maximizes energy efficiency, leading to reduced fuel consumption and lower carbon emissions.To ensure the highest quality and performance, [Company Name] subjects its high-temperature castable refractory to rigorous quality control procedures. The refractory is manufactured in state-of-the-art facilities, using advanced production techniques and premium raw materials. Additionally, [Company Name] offers comprehensive technical support and consultation services, assisting customers in selecting the most suitable refractory solution for their specific applications.[Company Name]'s commitment to sustainability is also reflected in its high-temperature castable refractory. The product is manufactured using environmentally friendly processes, adhering to strict compliance with relevant regulations. The refractory's long service life and energy-efficient properties contribute to a greener industrial landscape, promoting resource conservation and reducing waste.With the launch of its high-temperature castable refractory, [Company Name] aims to strengthen its position as a leading provider of cutting-edge refractory solutions. This innovative product showcases the company's dedication to delivering advanced technologies that enhance the performance and reliability of industrial processes.Industries can now look forward to improved operational efficiency, extended equipment lifespan, and reduced downtime, thanks to [Company Name]'s high-temperature castable refractory. By addressing the challenges associated with traditional refractories, this new offering brings significant benefits to companies across various sectors.About [Company Name]:[Company Name] is a renowned provider of refractory solutions for a wide range of industries, including steel, cement, petrochemical, and more. With a strong focus on innovation, quality, and customer satisfaction, the company is dedicated to delivering reliable and efficient refractory products that meet the evolving needs of its clients. Its team of experts ensures a seamless implementation of refractory solutions, providing comprehensive technical support and consultation services. Through continuous research and development, [Company Name] remains at the forefront of the refractory industry, always striving to provide cutting-edge solutions that drive industry progress.
Different Types of Refractory Materials: A Complete Guide
Title: Advancements in Refractory Materials Transform IndustriesIntroduction:Refractory materials have been an integral part of various industries, providing crucial resistance to extreme temperatures and chemical reactions. These materials are used in applications such as furnaces, kilns, reactors, and incinerators, where they play a vital role in maintaining operational efficiency. Today, we explore the latest advancements in refractory technology and its impact on industries worldwide.Background:Refractory materials are designed to withstand high temperatures and harsh environments, while also possessing excellent resistance to thermal shock, corrosion, and abrasion. They are commonly categorized into three types: acidic, basic, and neutral refractories, each suited for specific applications. As industries continue to evolve, the demand for more advanced refractory solutions has grown significantly.Company Introduction:{Company Name}, a leading manufacturer and supplier of refractory materials, has been at the forefront of innovation in this industry for many years. With their expertise, extensive R&D capabilities, and commitment to quality, {Company Name} has played a pivotal role in driving technological advancements in refractories.Types of Refractory Materials:1. Acidic Refractories:Acidic refractories primarily consist of silica, alumina, and varying proportions of other oxides. These materials possess excellent resistance to acidic environments, making them ideal for industries such as petrochemicals, energy, and metallurgy. Erosion-resistant acidic refractories have become increasingly popular due to their ability to withstand aggressive chemicals and high temperatures.2. Basic Refractories:Basic refractories are typically composed of magnesia, dolomite, or chrome-magnesia. They exhibit exceptional resistance to basic slag and alkaline environments, which makes them suitable for applications in the steel, cement, and non-ferrous metal industries. The high refractoriness and low thermal conductivity of basic refractories contribute to enhanced energy efficiency and extended equipment lifespan.3. Neutral Refractories:Neutral refractories have a high alumina content and possess excellent resistance to both acidic and basic environments. These materials find wide application in industries such as glass-making, ceramics, and incinerators. Their versatility and durability make them an ideal choice for processes where varied chemical environments are present.Advancements in Refractory Technology:1. Increased Thermal Efficiency:{Company Name}, working in collaboration with research institutions, has developed refractory materials with improved thermal conductivity. These advancements allow for enhanced heat transfer efficiency, resulting in reduced energy consumption and lower production costs for industries utilizing high-temperature processes.2. Enhanced Chemical Resistance:To address the increasing demand for resistance to aggressive chemicals, {Company Name} has developed advanced erosion-resistant refractories. These innovative materials exhibit superior corrosion resistance, enabling industries to operate in highly corrosive environments without compromising performance or durability.3. Longer Lifespan and Reduced Downtime:Through continuous research and development, {Company Name} has created refractory materials with extended lifespans. This improvement significantly reduces downtime associated with maintenance, resulting in enhanced operational efficiency and cost savings for industries relying on refractory-lined equipment.Conclusion:The continuous advancements in refractory materials and technology, spearheaded by {Company Name}, are revolutionizing industries worldwide. With improved thermal efficiency, enhanced chemical resistance, and extended lifespan, these refractory solutions are addressing the ever-evolving needs of industries. By utilizing these latest advancements, businesses can optimize their operations, reduce costs, and ensure safer and more sustainable processes. The future of refractory materials holds promise for industries looking to achieve greater efficiency and productivity in their operations.
The Latest Study on Thermal Conductivity of Firebrick: Key Findings Revealed
Title: Enhanced Thermal Conductivity Materials Revolutionize the Firebrick IndustryIntroduction:In recent years, the demand for advanced thermal insulation materials has surged due to their crucial role in conserving energy and reducing greenhouse gas emissions. One such breakthrough in the field is the development of high-performance firebrick thermal conductivity materials. These cutting-edge solutions offer exceptional insulation capabilities, reshaping the industry and presenting new opportunities for energy conservation and sustainability.Paragraph 1:Thermal conductivity, measured in watts per meter-kelvin (W/m·K), is a critical property in materials used for insulation purposes. The lower the thermal conductivity value, the better the material's insulation capacity. The emergence of firebrick thermal conductivity materials with significantly improved performance has the potential to transform various sectors, including construction, manufacturing, and aerospace.Paragraph 2:One leading player in this field is a pioneering company that has developed a remarkable firebrick thermal conductivity material, revolutionizing the market with its exceptional insulation properties. This game-changing solution offers an ultra-low thermal conductivity that surpasses traditional firebrick materials and significantly enhances the overall energy efficiency of various applications.Paragraph 3:The new firebrick thermal conductivity material exhibits a unique microstructure engineered to minimize heat conduction. The breakthrough lies in its optimized composition, which includes advanced additives, additives (brand names removed), that amplify its insulating properties. This remarkable combination effectively reduces heat transmission while maintaining structural integrity, making it ideal for a wide range of thermal insulation applications.Paragraph 4:The improved thermal conductivity material showcases outstanding resistance to high temperatures, providing reliable insulation even in extreme conditions. Its versatile performance makes it suitable for critical applications, such as furnace linings, kilns, incinerators, and various industrial processes that require exceptional thermal insulation capabilities.Paragraph 5:Additionally, the firebrick thermal conductivity material boasts excellent chemical resistance and durability, ensuring a long lifespan and reduced maintenance costs. Its enhanced insulation properties contribute to reducing energy consumption and minimizing carbon emissions, aligning with the global sustainability objectives and environmental regulations surrounding energy-efficient practices.Paragraph 6:The manufacturing sector can significantly benefit from this new innovation by utilizing it in the development of energy-efficient furnaces and kilns. By reducing thermal losses during heating processes, companies can enhance productivity, reduce fuel consumption, and lower greenhouse gas emissions.Paragraph 7:Furthermore, the construction industry can leverage this groundbreaking firebrick thermal conductivity material to enhance the energy efficiency of buildings. By incorporating it into insulation materials, constructors can improve the overall thermal resistance of structures, resulting in reduced HVAC energy consumption and increased comfort for occupants.Paragraph 8:The aerospace industry also stands to gain from this innovation, as the firebrick thermal conductivity material's lightweight and exceptional insulation properties can be incorporated into aircraft designs. This integration could potentially enhance fuel efficiency, reduce airframe weight, and contribute to the industry's overall sustainability goals.Conclusion:The development of advanced firebrick thermal conductivity materials offers a promising solution to the global demand for improved thermal insulation. With their remarkable properties, these materials have the potential to revolutionize various sectors, including construction, manufacturing, and aerospace. By maximizing energy efficiency, reducing carbon emissions, and promoting sustainability, the introduction of such materials represents a significant step towards a more environmentally conscious future.
How to Choose the Best Refractory Castable Concrete for Your Project
Refractory Castable Concrete Revolutionizes High-Temperature EnvironmentsIntroduction:With the constant need for advancements in various industries, the quest for materials capable of withstanding extreme temperatures becomes imperative. One company that has made significant strides in this area is {nominated company}, a pioneer in the production of innovative refractory castable concrete. Their groundbreaking materials have propelled industrial manufacturing and infrastructure development to new heights, allowing for safer and more efficient operations in high-temperature environments. This article delves into the exceptional qualities of refractory castable concrete and its application in a wide range of industries.The Unparalleled Advantages of Refractory Castable Concrete:Refractory castable concrete is designed to withstand extremely high temperatures, making it an indispensable material in industries such as steel, cement, petrochemical, and power generation. Unlike traditional concrete, refractory castable concrete exhibits exceptional thermal shock resistance, thermal conductivity, and insulating properties. These properties ensure the material's durability and ability to maintain structural integrity even under intense heat and rapid temperature fluctuations.The composition of refractory castable concrete includes a blend of aggregates, cementitious binders, and additives. The exact formulation varies depending on the intended application and temperature requirements. Manufactured using advanced production techniques, these materials result in a uniform, dense, and highly reliable product.Typically applied as linings for furnaces, kilns, and industrial boilers, refractory castable concrete offers excellent resistance to alkalis, acids, abrasion, and erosion. This characteristic extends the lifespan of equipment and reduces maintenance costs, resulting in substantial savings for businesses operating in high-temperature environments.Applications in Various Industries:The steel industry is one of the primary beneficiaries of refractory castable concrete. In steelmaking furnaces, where temperatures can exceed 1500°C (2732°F), the lining materials must be able to endure extreme heat and endure the effects of molten metal and slag. Refractory castable concrete surpasses these demands and provides reliable insulation, preventing heat loss and ensuring energy efficiency.Similarly, refractory castable concrete plays a crucial role in the cement industry, where kilns operate continuously at temperatures exceeding 1450°C (2642°F). The material's exceptional resistance to thermal shocks allows kilns to operate efficiently, reducing downtime and enhancing productivity. By minimizing heat loss from the kiln, refractory castable concrete also contributes to lower energy costs and a greener manufacturing process.Petrochemical plants and power generation facilities also rely heavily on refractory castable concrete to maintain safety and operational efficiency. Petrochemical processes involve high-temperature reactions and corrosive chemicals, demanding a lining material that can withstand these harsh conditions. Refractory castable concrete provides the necessary thermal insulation and chemical resistance to ensure stable operation and increased plant reliability.Advancements in the development of refractory castable concrete have expanded its applications further. The material's insulating properties make it suitable for use in fireplaces, chimneys, incinerators, and even domestic wood-fired ovens. Its ability to effectively withstand intense heat allows for enhanced fire safety measures, making the use of refractory castable concrete essential in protecting structures and lives.Conclusion:Refractory castable concrete has revolutionized high-temperature environments across various industries. {Nominated Company} has pioneered its production, enabling businesses to operate with increased efficiency, reliability, and safety. With its exceptional thermal resistance, thermal shock resistance, and insulating properties, refractory castable concrete has become an irreplaceable material, providing a sustainable and cost-effective solution for withstanding extreme temperatures. As technology continues to improve, we can expect further advancements in refractory castable concrete, leading to even safer and more efficient operations in the future.
Ceramic Fiber Products: Unveiling the Latest Innovations in Heat Insulation
Title: Enhanced Insulation Solution: Isowool Introduces Groundbreaking Ceramic Fiber TechnologyIntroduction (150 words):Isowool, a leading innovator in insulation solutions, has announced a groundbreaking technology in the field of ceramic fibers. Built upon decades of research and development, the new product aims to revolutionize insulation systems across industries with enhanced thermal performance, durability, and energy efficiency. This cutting-edge ceramic fiber, devoid of hazarous materials, offers a sustainable solution while fulfilling the stringent safety standards that are mandated across various sectors. Isowool's commitment to delivering superior insulation products, combined with their extensive expertise in thermal insulation, make them well-positioned to address the increasing market demands for sustainable, durable, and high-performance thermal management solutions.Body:1. Advancements in Ceramic Fiber Technology: Meeting Industry Demands (200 words)Isowool's latest ceramic fiber technology represents a significant leap in the field of insulation solutions. This revolutionary offering combines superior thermal insulation properties with sustainable and environmentally friendly aspects, placing it at the forefront of the industry. Isowool's product emerges as a reliable solution that promises to drive energy efficiency, reduce carbon footprint, and improve productivity across various sectors, from manufacturing to construction.The use of advanced materials and cutting-edge manufacturing processes ensures the durability and longevity of the ceramic fiber. Isowool's ceramic fiber is capable of withstanding high temperatures and resisting chemical or mechanical stresses, making it an ideal choice for challenging and demanding applications. The product's superior thermal properties contribute to energy conservation and cost-effectiveness, thereby making it an attractive solution for businesses across diverse industries. 2. Applications Across Industries: Versatility and Adaptability (200 words)One of the key advantages of Isowool's ceramic fiber is its versatility and adaptability to various industrial applications. Its high-temperature resistance and ability to withstand harsh environments make it an ideal choice for industries such as metal processing, power generation, automotive, aerospace, and more. In metal processing, where high-temperature furnaces and kilns are utilized, Isowool's ceramic fiber provides excellent insulation, ensuring energy efficiency and cost savings. The automotive and aerospace sectors benefit from the product's lightweight nature and exceptional thermal insulation, enhancing both fuel efficiency and passenger comfort.Furthermore, Isowool's ceramic fiber finds extensive use in the construction industry, addressing insulation needs across commercial, residential, and infrastructure development projects. By providing a high level of fire resistance and thermal insulation, the product helps in promoting sustainable and energy-efficient construction practices.3. Sustainability and Safety: Complying with Environmental Norms (200 words)In line with global sustainability goals, Isowool's ceramic fiber technology stands as a testament to their commitment to environmental consciousness. Unlike traditional insulation materials, Isowool's solution is free from hazardous substances such as asbestos, reducing health risks for both installers and end-users.Additionally, Isowool's streamlined manufacturing processes prioritize energy efficiency and low waste generation, thereby minimizing the company's carbon footprint. Incorporating this environmentally friendly insulation product can contribute significantly to meeting energy consumption reduction targets and building eco-friendly infrastructures.Moreover, the elimination of hazardous materials complies with strict industry safety standards, ensuring a safer working environment for employees and reducing the risk of occupational health issues. Isowool's focus on sustainable and safe products sets a benchmark for the industry, urging other insulation manufacturers to follow suit and prioritize environmentally responsible solutions.Conclusion (150 words):Isowool's introduction of their innovative ceramic fiber technology propels the insulation industry toward sustainable and energy-efficient practices. With its enhanced thermal properties, adaptability across diverse industries, and commitment to sustainability and safety, Isowool's ceramic fiber is set to redefine the status quo of thermal insulation systems. This groundbreaking product caters to the demands of numerous sectors, from manufacturing to construction, providing them with a reliable, durable, and high-performance solution that contributes to a greener tomorrow. As their cutting-edge insulation solution continues to gain traction, Isowool stands as a vanguard of technological progress, propelling various industries toward a more sustainable and energy-efficient future.
Efficient Aluminum Crucible Furnaces: A Game-Changer in the Industry
Aluminum Crucible Furnace: A Revolutionary Solution for Melting MetalsIn today's fast-paced world, the demand for precision and speed is higher than ever before. Every industry aims to be more efficient and productive to stay ahead of the competition and meet the demands of their customers. One such industry is the metallurgical industry that requires melting metals to create alloys and other derivatives. Understanding the need for efficiency and speed, {Company Name} has introduced an innovative solution, the Aluminum Crucible Furnace, which provides a revolutionary way of melting metals.The Aluminum Crucible Furnace is a unique concept that is designed for melting and casting all types of alloys and metals with the utmost precision and accuracy. The furnace is extremely energy-efficient and reduces energy consumption by up to 50% compared to the traditional furnaces. It is also an eco-friendly option that reduces greenhouse gas emissions and thus helps to preserve the environment.The Aluminum Crucible Furnace is built using the latest technological advancements and is a fully automated system that is easy to operate. The furnace is equipped with state-of-the-art sensors that help to regulate the temperature and maintain a consistent melt quality. The furnace has an ergonomic design that reduces operator fatigue, and it is built to withstand the harsh working conditions of a metallurgical environment.The furnace has a capacity of up to 2000 kg and can operate for extended periods without the need for frequent maintenance. The Aluminum Crucible Furnace is a safe and reliable option for melting and casting alloys and metals, and it can help to boost productivity, reduce costs, and improve the quality of the final product.{Company Name} is a leading manufacturer of metallurgical equipment and has been providing innovative solutions to the industry for over a decade. The company is committed to providing the best quality products and services to its customers and has a reputation for excellence in the market. {Company Name} has a team of experts who are dedicated to researching and developing new solutions that cater to the changing needs of the industry.The introduction of the Aluminum Crucible Furnace is a testament to the company's commitment to innovation and excellence. The furnace is already gaining popularity in the industry, and many customers have reported significant improvements in their productivity and efficiency after switching to this new technology.In summary, the Aluminum Crucible Furnace is a revolutionary solution that offers significant benefits over traditional furnaces. It is energy-efficient, eco-friendly, and easy to operate, making it an ideal choice for melting and casting alloys and metals. {Company Name}'s commitment to innovation and quality has made it a leader in the metallurgical equipment industry, and the Aluminum Crucible Furnace is another feather in its cap.
Fireclay Properties: A Closer Look at the Latest Developments in the Real Estate Sector
article covering their recent achievements and future plans.Fireclay Properties Achieves Major Success in the Real Estate MarketFireclay Properties is a real estate development company that has been creating stunning custom-built properties for clients all over the world. With a commitment to delivering high-quality, bespoke homes that are tailored to the unique needs of each client, Fireclay Properties has quickly established itself as a leader in the industry.The company's philosophy is based on the belief that a home should not just be a place to live, but a reflection of the owner's personality and lifestyle. To achieve this, the team at Fireclay Properties works closely with each client to understand their vision and create a home that surpasses their expectations.Recently, Fireclay Properties has achieved a number of major successes in the real estate market. In particular, the company has broken new ground in the area of sustainable construction, with a focus on using eco-friendly materials and innovative design techniques to create homes that are both beautiful and environmentally responsible.One of the key projects that highlights Fireclay Properties' commitment to sustainability is the recently completed 203k renovation of a historic property in the heart of a San Francisco neighborhood. This project involved a comprehensive renovation of a turn-of-the-century building that had fallen into disrepair, transforming it into an energy-efficient, modern dwelling that retains its historic charm.The renovation involved a number of innovative sustainable design features, including natural ventilation, radiant heating and cooling, and high-efficiency lighting and appliances. The result is a home that is not only beautiful and functional, but also environmentally responsible and energy-efficient.Another area in which Fireclay Properties has achieved notable success is in the development of luxury rental properties. Unlike many property developers who focus primarily on building homes for sale, Fireclay Properties has recognized the growing demand for high-end rental properties, particularly among younger professionals who value flexibility and convenience.One of the company's recent projects in this area is a luxury apartment building located in San Francisco's trendy Mission district. Designed with the needs of modern renters in mind, this building features spacious, light-filled units with high-end finishes and amenities like on-site fitness centers and rooftop lounges.Looking to the future, Fireclay Properties has ambitious plans to continue to innovate and push the boundaries of sustainable design and luxury construction. The company is focused on expanding its reach and taking on new projects in a variety of markets, from urban apartments to rural estates.One exciting project currently in development is a set of off-grid, self-sustaining homes that will be designed to blend seamlessly into their natural environments. These homes will be powered by solar and wind energy, and will be built using locally sourced, eco-friendly materials.Overall, Fireclay Properties is a company that is making waves in the real estate market. With a focus on sustainable design and a commitment to delivering exceptional homes that are tailored to the unique needs of each client, this company is sure to remain a leader in the industry for years to come.
Advancements in Continuous Casting Furnace Technology for Enhanced Industrial Efficiency
[Company Introduction]{Insert Company Name} is a renowned leader in the manufacturing sector, known for its cutting-edge technologies and innovative solutions. With a global footprint and an extensive portfolio of products, the company has established its presence across various industries, including the metals industry.[News Content]Continuous Casting Furnace Revolutionizes the Metals Industry{City, Date} - In a bid to redefine the way metal products are manufactured, {Insert Company Name}, a pioneer in industrial technologies, has unveiled its latest breakthrough in the field of metal casting - the state-of-the-art Continuous Casting Furnace (CCF). This revolutionary furnace is set to transform the metals industry, offering unmatched efficiency, precision, and sustainability.Traditionally, metal casting processes have relied on batch production, which involved melting large quantities of metal to create discrete batches of products. However, the Continuous Casting Furnace, developed by {Insert Company Name}, eliminates the need for batch production, leading to significant improvements in productivity and product quality.The Continuous Casting Furnace incorporates advanced technologies that allow for the continuous production of metal products, such as steel billets, slabs, and blooms. This continuous process ensures a constant flow of output, minimizing downtime and maximizing overall throughput. With this innovative furnace, manufacturers can achieve higher production volumes, reducing lead times and meeting the ever-increasing demands of the market.One of the standout features of the Continuous Casting Furnace is its ability to enhance product quality and consistency. By maintaining a steady, controlled flow of molten metal, the furnace ensures uniformity in the casting process, resulting in products with fewer defects, improved dimensional accuracy, and enhanced surface finishes. This translates into superior end products that meet the stringent quality standards of various industries.In addition to its efficiency and product quality benefits, the Continuous Casting Furnace also offers remarkable sustainability advantages. The furnace utilizes advanced energy management systems that optimize energy consumption and decrease environmental impact. By streamlining the casting process, manufacturers can significantly reduce energy usage and minimize waste generated during production. This ensures a more sustainable approach to manufacturing, aligning with global efforts to reduce carbon emissions and promote eco-friendly practices.{Insert Company Name} has invested significant resources in research and development to bring the Continuous Casting Furnace to market. The company’s team of highly skilled engineers and metallurgical experts have collaborated to design a furnace that delivers exceptional performance across various industries, including automotive, construction, and manufacturing."The introduction of our Continuous Casting Furnace represents a major milestone in the metals industry. This cutting-edge technology will revolutionize the way metal products are manufactured, offering transformative benefits to our customers," said {Spokesperson Name}, {Job Title} at {Insert Company Name}.This breakthrough innovation is a testament to {Insert Company Name}'s commitment to pushing the boundaries of what is possible in industrial manufacturing. The company's dedication to research, development, and technological advancements has solidified its position as a global leader, continuously delivering solutions that address the evolving needs of industries worldwide.As the metals industry embraces the Continuous Casting Furnace, manufacturers can expect increased productivity, improved product quality, and a reduced environmental footprint. This game-changing technology is set to shape the future of metal casting, offering a more efficient, sustainable, and competitive approach to manufacturing.