Cutting-Edge Crucible Furnace: Revolutionizing Glass Production
By:Admin
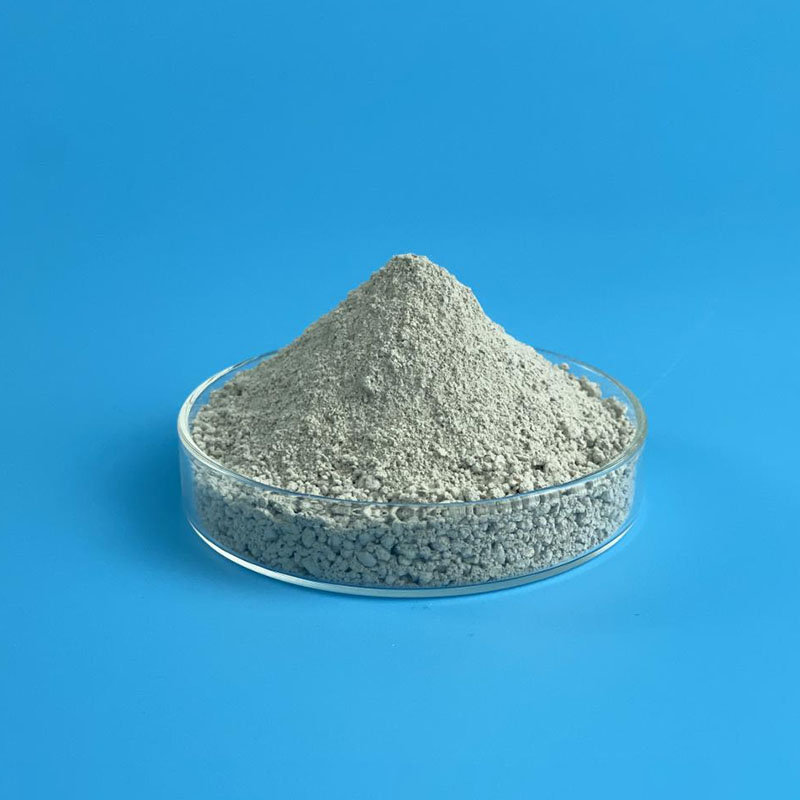
Introduction:
The glass manufacturing industry is set to witness a significant transformation with the introduction of an advanced and innovative crucible furnace. This cutting-edge technology, developed by a prominent industry player, promises to redefine glass production processes, offering improved efficiency, enhanced product quality, and reduced environmental impact. The newly unveiled furnace, designed to remove the brand name, is set to revolutionize the glass manufacturing landscape.
A Crucible Furnace Revolution:
Crucible furnaces have been an integral part of glass production for centuries. These specialized furnaces have traditionally relied on combustion systems to generate the intense heat required for melting glass raw materials. The innovative crucible furnace, developed by a leading glass manufacturing technology firm, incorporates state-of-the-art features and advancements, making it a game-changer for the industry.
Improved Efficiency and Capacity:
The new crucible furnace boasts a groundbreaking design that significantly enhances efficiency and production capacity. By employing cutting-edge insulation materials and advanced heating techniques, the furnace ensures maximum heat retention while minimizing energy consumption. This advancement leads to improved melting rates, reducing production downtime and increasing overall output.
Additionally, the new furnace's modular design allows for easy scalability, making it suitable for both small-scale and large-scale glass manufacturing operations. The enhanced capacity enables glass manufacturers to meet increasing market demands efficiently and effectively.
Enhanced Product Quality:
One of the standout features of this groundbreaking crucible furnace is its ability to produce glass with exceptional clarity and superior quality. The incorporation of precise temperature control systems ensures consistent and uniform melting, resulting in glass products free from impurities, bubbles, or defects. This significant improvement in product quality enhances the reputation of glass manufacturers while meeting the stringent standards set by the industry.
Furthermore, the new furnace minimizes variations in glass composition, resulting in enhanced color consistency and increased batch yields. These advancements not only boost the quality of glass products but also offer manufacturers a competitive edge in the market.
Reduced Environmental Impact:
Addressing environmental concerns is a priority for the glass manufacturing industry. The innovative crucible furnace demonstrates a commitment to sustainability by significantly reducing greenhouse gas emissions and energy consumption. The implementation of advanced combustion and exhaust gas treatment technologies effectively minimizes the release of harmful pollutants, reducing the furnace's environmental impact.
Moreover, the furnace's improved energy efficiency reduces the industry's reliance on fossil fuels, leading to reduced carbon emissions. By adopting this new technology, glass manufacturers can contribute to a cleaner and greener future while meeting their production targets.
Company's Commitment to Innovation:
The development of this revolutionary crucible furnace underscores the commitment of the glass manufacturing technology firm to innovation. The company's extensive research and development efforts have resulted in a groundbreaking solution that addresses the industry's key challenges.
With a history of pioneering advancements in glass manufacturing technology, the firm is renowned for its customer-centric approach and collaborative partnerships with glass manufacturers worldwide. The unwavering focus on research and innovation has solidified their position as an industry leader, pushing the boundaries of what is possible in glass production.
Conclusion:
The unveiling of an innovative crucible furnace marks a significant turning point for the glass manufacturing industry. With improved efficiency, enhanced product quality, and reduced environmental impact, this groundbreaking technology promises to drive the industry towards a more sustainable and competitive future. As glass manufacturers embrace this revolutionary solution, they can look forward to optimized operations and increased profitability while meeting the demands of a growing market.
Company News & Blog
Essential Guide to Castable Refractory Forging and Its Applications
Title: Innovative Castable Refractory Forge Revolutionizes Industrial Processes Introduction:In an era of constant technological advancements and innovative solutions, companies worldwide are continuously striving to enhance their manufacturing and industrial processes. One such company, which aims to revolutionize the industrial realm, has developed a groundbreaking Castable Refractory Forge. By combining cutting-edge technology with their expertise in refractories, this company is set to redefine efficiency and productivity in various industries.Breaking Boundaries with the Castable Refractory Forge:The Castable Refractory Forge, developed by the company, is a state-of-the-art solution designed to withstand extreme temperatures, providing exceptional thermal resistance and durability. This cutting-edge technology is set to transform traditional industrial processes, allowing businesses to achieve greater efficiency, cost-effectiveness, and environmental sustainability.Unparalleled Heat Resistance:The exceptional heat resistance of the Castable Refractory Forge allows industries to perform high-temperature applications with utmost reliability. From metallurgical processes to petrochemical applications, this innovative solution outperforms traditional refractory materials, offering higher resistance to melting, cracking, and substrate deformation.Enhanced Productivity:By incorporating the Castable Refractory Forge, industries can significantly increase their productivity levels. The forge's advanced insulation properties minimize heat losses, ensuring optimal thermal management within the manufacturing process. This results in faster heating and cooling cycles, reducing downtime and improving overall production output, thereby enhancing profitability for businesses.Versatile Applications:The Castable Refractory Forge is adaptable to a wide range of applications, catering to various industries such as steel, aluminum, cement, glass, and petrochemicals. Its versatility allows companies to streamline their operations by using a single refractory solution, thereby reducing costs and simplifying maintenance processes.Reduced Environmental Impact:In addition to its operational advantages, the Castable Refractory Forge contributes to environmental sustainability. Its advanced insulation characteristics lead to reduced energy consumption, minimizing greenhouse gas emissions and promoting a cleaner and greener industrial footprint. By implementing this technology, industries can align their operations with global environmental commitments and regulations.Safety and Quality Assurance:The company, known for its commitment to stringent quality standards, ensures that the Castable Refractory Forge meets the highest safety requirements. Rigorous testing procedures and quality-control measures are undertaken to safeguard industrial processes against potential hazards while maintaining the utmost quality and efficiency.Collaborative Approach:As part of the company's overarching mission to provide comprehensive industrial solutions, they foster collaboration with clients to address specific requirements. By actively engaging with customers, the company aims to customize the Castable Refractory Forge to suit individual needs, ensuring seamless integration into existing infrastructure. This collaborative approach further strengthens the company's commitment to its clients' success.Driving Industrial Advancement:The introduction of the Castable Refractory Forge is a testament to the company's dedication to driving industrial advancement. By combining extensive research and development with a passion for innovation, this groundbreaking technology is set to transform industrial processes worldwide, maximizing efficiency and profitability for businesses across diverse sectors.Conclusion:In an ever-evolving industrial landscape, the company's Castable Refractory Forge emerges as a pioneering solution, revolutionizing traditional manufacturing practices. Its unrivaled heat resistance, enhanced productivity, versatile applications, reduced environmental impact, safety, and commitment to collaborative partnerships make it a trailblazer in the field of refractory technologies. As industries become increasingly reliant on cutting-edge solutions to remain competitive, the Castable Refractory Forge stands poised to lead the way towards a more efficient, sustainable, and successful industrial future.
How to Choose the Best Furnace for Iron Melting?
In today’s world, the use of metal alloys and pure metals is becoming increasingly important for use in various industries. Metal alloys and pure metals serve as building blocks for a vast array of equipment and structures from vehicles to buildings. To utilize these metals optimally, they need to be melted, and a furnace is the best tool for that job. That is where our company, who has been in the industry for several years, comes in. Our furnace for iron melting equipment is perfect for melting iron alloys and pure iron.Iron melting is a process that requires a lot of precision and care, which is why our company creates top-quality furnaces that are tailored for this purpose. Our furnaces are designed to make the iron melting process easy and efficient, making them the go-to choice for many companies in multiple industries which use iron.Our furnaces are designed with safety in mind, incorporating multiple features for a safe and efficient melting process. Our furnaces come with built-in thermocouples and other sensors that monitor the temperature and pressure of the furnace and automatically adjust it to prevent any accidents.In addition, our furnaces are most efficient, and you will love the quality and speed of the melting process. We can guarantee that our furnace for iron melting is the most efficient on the market. Our furnaces are designed with energy efficiency and cost-effectiveness in mind, making them affordable for any company looking to invest in iron melting.Using our furnace for iron melting, you can melt 50 kg of iron or more at a time. This makes it easy to melt large quantities of iron in a short amount of time, which is necessary for many construction and manufacturing projects.Our furnace is also customizable to perfectly fit the needs of each customer. We understand that every company has unique needs when it comes to melting iron. Therefore, we offer custom solutions to meet those needs. We can adjust the temperature range, melting speed, and other factors of your furnace to suit your requirements.The furnace for iron melting is perfect for a wide variety of industries, including construction, machinery manufacturing, and automotive manufacturing, making it among the most versatile on the market. Our reliable furnace allows you to melt iron at your own pace without sacrificing the quality of the end product.The furnace for iron melting that our company produces is the perfect choice for companies that require speedy and efficient iron melting. Our company has years of experience in the manufacturing of industrial equipment and knows what it takes to create a top-quality product. Our furnaces are made from top-quality materials that are designed to withstand the wear and tear of heavy use.Our company takes pride in delivering the highest-quality products to our customers. We understand that delivering high-quality equipment is essential to the success of our customers. That is why we work hard to ensure that each of our products meets the highest standards of quality.In conclusion, our furnace for iron melting is the perfect choice for companies seeking an efficient and economical solution to melting iron alloys and pure iron. Our furnaces are designed to be safe, efficient, and customizable to meet the needs of each customer. Our company has years of experience creating top-quality industrial equipment and knows what it takes to create a product that is reliable and capable of handling heavy usage. Contact us today to find out more about our furnace for iron melting and how they can improve your company’s efficiency.
How Fire Bricks are Made and Their Applications
Fire Bricks Are Made From Natural Materials, Revolutionizing the Construction IndustryIn today's rapidly evolving world, the construction industry is constantly seeking innovative and sustainable solutions. One such groundbreaking invention is the production of fire bricks, which are revolutionizing the way buildings are constructed. These revolutionary bricks are manufactured using natural materials and have proven to be highly durable, making them an ideal choice for a wide range of applications.Fire bricks are primarily made from high-quality clay, combined with other natural materials such as silica, alumina, and magnesia. These ingredients are carefully selected for their thermal resistance and ability to withstand high temperatures, making fire bricks an excellent choice for insulation and fireproofing applications. Due to their unique composition, fire bricks have gained significant popularity in various industries, including manufacturing, construction, and even aerospace.The production process of fire bricks begins with the careful selection and preparation of the raw materials. The selected clay is mixed with the other components, forming a homogeneous mixture. This mixture is then shaped into bricks using a molding machine or by hand, depending on the desired size and shape. The bricks are then subjected to a high-temperature firing process, allowing them to acquire their exceptional thermal resistance properties. Once the firing process is complete, the fire bricks are ready to be used in construction projects.One of the leading manufacturers in the field of fire bricks is a company specializing in the production of high-quality construction materials. With a strong commitment to innovation and sustainability, this company has revolutionized the construction industry by introducing fire bricks as a superior alternative to traditional building materials. The company's dedication to research and development has resulted in the creation of fire bricks with unprecedented durability and thermal resistance.The unique properties of fire bricks make them highly versatile and suitable for a wide range of applications. They are commonly used as lining materials in furnaces, kilns, and fireplaces, where they provide excellent insulation and prevent heat loss. Their use in these high-temperature environments not only ensures the safety and stability of the structures but also increases energy efficiency by reducing heat transfer. Additionally, fire bricks find applications in industrial chimneys, incinerators, and even in the construction of rocket engines, where their ability to withstand extreme temperatures is of utmost importance.One of the main advantages of fire bricks is their exceptional thermal resistance. Unlike traditional bricks, fire bricks can withstand temperatures of up to 3000°C (5400°F), making them ideal for applications requiring high levels of heat insulation. This makes them particularly useful in industries where the containment and control of high temperatures are critical, such as steel production and glass manufacturing.Furthermore, fire bricks offer superior durability and longevity compared to conventional building materials. Their resistance to thermal shock and chemical erosion ensures their longevity, reducing the need for frequent repairs and replacements. This not only saves costs but also minimizes environmental impact by reducing waste generation.With the increasing focus on sustainability and environmental responsibility, fire bricks have emerged as a significant player in the construction industry. Made from natural materials and boasting exceptional durability, fire bricks contribute to the overall green initiative by minimizing the depletion of natural resources. Additionally, their thermal insulation properties help reduce energy consumption and lower greenhouse gas emissions, further promoting a sustainable approach to construction.The introduction of fire bricks to the construction industry has garnered significant attention, leading to their increasing adoption in various applications worldwide. Construction professionals have recognized the immense benefits offered by fire bricks, including their thermal resistance, longevity, and environmental sustainability. As a result, the demand for fire bricks is expected to continue to rise, making them a key ingredient in the future of construction.In conclusion, fire bricks are a revolutionary and sustainable alternative to traditional building materials. Made from natural ingredients, these bricks offer exceptional thermal resistance and durability, making them suitable for various high-temperature applications. The advent of fire bricks has significantly transformed the construction industry, providing builders with a reliable and eco-friendly solution. As the demand for sustainable construction practices increases, fire bricks are set to play a vital role in shaping the buildings of the future.
Advancements in Continuous Casting Furnace Technology for Enhanced Industrial Efficiency
[Company Introduction]{Insert Company Name} is a renowned leader in the manufacturing sector, known for its cutting-edge technologies and innovative solutions. With a global footprint and an extensive portfolio of products, the company has established its presence across various industries, including the metals industry.[News Content]Continuous Casting Furnace Revolutionizes the Metals Industry{City, Date} - In a bid to redefine the way metal products are manufactured, {Insert Company Name}, a pioneer in industrial technologies, has unveiled its latest breakthrough in the field of metal casting - the state-of-the-art Continuous Casting Furnace (CCF). This revolutionary furnace is set to transform the metals industry, offering unmatched efficiency, precision, and sustainability.Traditionally, metal casting processes have relied on batch production, which involved melting large quantities of metal to create discrete batches of products. However, the Continuous Casting Furnace, developed by {Insert Company Name}, eliminates the need for batch production, leading to significant improvements in productivity and product quality.The Continuous Casting Furnace incorporates advanced technologies that allow for the continuous production of metal products, such as steel billets, slabs, and blooms. This continuous process ensures a constant flow of output, minimizing downtime and maximizing overall throughput. With this innovative furnace, manufacturers can achieve higher production volumes, reducing lead times and meeting the ever-increasing demands of the market.One of the standout features of the Continuous Casting Furnace is its ability to enhance product quality and consistency. By maintaining a steady, controlled flow of molten metal, the furnace ensures uniformity in the casting process, resulting in products with fewer defects, improved dimensional accuracy, and enhanced surface finishes. This translates into superior end products that meet the stringent quality standards of various industries.In addition to its efficiency and product quality benefits, the Continuous Casting Furnace also offers remarkable sustainability advantages. The furnace utilizes advanced energy management systems that optimize energy consumption and decrease environmental impact. By streamlining the casting process, manufacturers can significantly reduce energy usage and minimize waste generated during production. This ensures a more sustainable approach to manufacturing, aligning with global efforts to reduce carbon emissions and promote eco-friendly practices.{Insert Company Name} has invested significant resources in research and development to bring the Continuous Casting Furnace to market. The company’s team of highly skilled engineers and metallurgical experts have collaborated to design a furnace that delivers exceptional performance across various industries, including automotive, construction, and manufacturing."The introduction of our Continuous Casting Furnace represents a major milestone in the metals industry. This cutting-edge technology will revolutionize the way metal products are manufactured, offering transformative benefits to our customers," said {Spokesperson Name}, {Job Title} at {Insert Company Name}.This breakthrough innovation is a testament to {Insert Company Name}'s commitment to pushing the boundaries of what is possible in industrial manufacturing. The company's dedication to research, development, and technological advancements has solidified its position as a global leader, continuously delivering solutions that address the evolving needs of industries worldwide.As the metals industry embraces the Continuous Casting Furnace, manufacturers can expect increased productivity, improved product quality, and a reduced environmental footprint. This game-changing technology is set to shape the future of metal casting, offering a more efficient, sustainable, and competitive approach to manufacturing.
Benefits of Ceramic Paper Insulation: A Revolutionary Solution for Efficient Home Insulation
Title: Innovative Ceramic Paper Insulation Revolutionizes the Construction IndustryIntroduction:{Company Name}, a pioneering company specializing in cutting-edge insulation solutions, has recently unveiled its latest product, Ceramic Paper Insulation. This revolutionary material is set to transform the construction industry, providing a sustainable and highly efficient alternative to traditional insulation methods.Innovation at its Core:Ceramic Paper Insulation is a lightweight and flexible material that offers excellent thermal insulation properties. It is composed of a combination of high-grade advanced ceramics and natural cellulose fibers, making it both environmentally friendly and highly durable. This innovative product provides a versatile solution for various applications, ranging from residential to commercial construction projects.Unmatched Thermal Efficiency:One of the most remarkable features of Ceramic Paper Insulation is its extraordinary thermal efficiency. The material's unique composition enables it to resist heat transfer, effectively minimizing energy loss and reducing heating and cooling costs. This attribute ensures that buildings remain cooler in summer, warmer in winter, and more energy-efficient all year round.Environmentally Sustainable:{Company Name}'s Ceramic Paper Insulation is a game-changer in terms of sustainability for the construction industry. It is free from harmful emissions such as formaldehyde and other volatile organic compounds (VOCs) commonly found in traditional insulation. The material's production process minimizes energy consumption, waste generation, and carbon emissions, further contributing to a greener future.Versatile and Easy to Install:Ceramic Paper Insulation is available in various thicknesses and can be easily customized to fit different structures and applications, including walls, roofing, and pipes. Its flexibility allows for seamless installation, eliminating gaps and preventing air leakage. This ease of installation ensures that the entire construction process is more efficient, saving both time and money.Durability and Longevity:Designed to withstand extreme temperatures, Ceramic Paper Insulation outperforms other conventional insulation materials, guaranteeing longevity and reducing the need for continuous maintenance. The material's exceptional resistance to wear and tear ensures that its insulating properties remain intact even after years of active use, thus providing a sustainable and cost-effective solution to building insulation.Fire-Resistant Properties:Safety is a paramount concern in any construction project, and Ceramic Paper Insulation excels in this area as well. The material possesses excellent fire-resistant properties, making it an ideal choice for a wide range of applications. By significantly reducing the spread of flames and toxic smoke, this insulation solution enhances the overall safety of buildings, ensuring a secure environment for residents, employees, and visitors alike.Contributing to Energy Efficiency Regulations:With the increasing focus on energy efficiency, Ceramic Paper Insulation helps construction projects meet regulatory guidelines and certifications. Its exceptional thermal performance enables buildings to achieve higher energy ratings, thereby fulfilling the requirements set by sustainability standards and contributing to a greener future.Conclusion:The launch of Ceramic Paper Insulation by {Company Name} marks a significant milestone in the construction industry. Its unparalleled thermal efficiency, sustainability, and versatility make it a superior alternative to conventional insulation materials. By incorporating this cutting-edge innovation in their projects, architects, contractors, and homeowners can significantly contribute to reducing energy consumption, enhancing safety standards, and building a more sustainable tomorrow.
Efficient and Reliable Propane Casting Furnace for Your Casting Needs
Propane Casting Furnace: The Perfect Solution for Melting MetalsMelting and casting of metals can be a daunting task, especially when you do not have the right equipment. This is why the {company name} has introduced the Propane Casting Furnace. With this advanced piece of machinery, you can increase your productivity and efficiency in metal melting.The {company name} is a leading supplier of casting equipment and supplies. Their state-of-the-art Propane Casting Furnace is designed to meet the unique needs of metal casting customers. This furnace is made using high-quality materials that make it durable and reliable. It is a perfect solution for melting and casting metals in small to medium-sized foundries and workshops.The Propane Casting Furnace is a safe, efficient, and clean way of melting metals. It has a maximum temperature rating of 2,400 degrees Fahrenheit and can melt a variety of metals such as copper alloys, aluminum, and zinc. The furnace has a capacity of melting up to 100 pounds of metal at a time.One of the unique features of this furnace is its patented burner system. The furnace is equipped with a high-pressure air-propane mixing burner that provides a stable flame, which leads to a cleaner and more efficient burn. The combination of the high-pressure air and propane ensures that every inch of the furnace is heated, which leads to a more uniform temperature.Another feature of the Propane Casting Furnace is its digital temperature controller. This controller enables operators to set the desired temperature and monitor the melting process. It is user-friendly and provides accurate temperature readings, which leads to precise control of the melting process.The Propane Casting Furnace is also designed with safety in mind. It has an advanced safety system that includes a pressure regulator, safety valve, and thermocouple safety shut off. These safety features ensure that operators are protected from any hazardous situations that may arise during the melting process.The furnace is easy to operate and maintain. It has a removable crucible that makes it easy to clean and replace. The furnace also has a durable and corrosion-resistant refractory lining that is designed to withstand the high temperatures and the corrosive nature of the melting process.The Propane Casting Furnace is a versatile piece of machinery that can be used in a variety of applications. It is ideal for melting metals for jewelry making, small-scale blacksmithing, hobby casting, and prototype casting. It is also perfect for small businesses that are involved in metal melting and casting.The {company name} offers a range of services that include furnace installation, training, maintenance, and repair. Their team of experts is always on hand to provide technical support and advice to customers. They also offer a range of accessories and supplies such as crucibles, tongs, and safety gear.In conclusion, the Propane Casting Furnace is a game-changer in the world of metal melting and casting. Its advanced features and safety system make it an ideal solution for small to medium-scale foundries and workshops. The furnace is a testament to the {company name}'s commitment to innovation and customer satisfaction. So if you are looking for an efficient, safe, and reliable way of melting and casting metals, the Propane Casting Furnace is the perfect solution for you.
Guide to Steel Casting Furnaces: Types, Applications, and Benefits
Steel Casting Furnace Breaks the Boundaries of Traditional Smelting TechnologyIn the rapidly advancing world of technology, industries and companies constantly seek innovative and efficient solutions to achieve their goals. Metallurgy and steel making are no exception, and one such revolutionary solution is the Steel Casting Furnace - a game-changing product that is transforming the way steel casting is carried out.Developed by one of the leading manufacturers of furnace equipment, the Steel Casting Furnace has revolutionized the smelting industry with its game-changing technology. Unlike traditional smelting furnaces, it adopts a unique concept of gravity casting, which greatly cuts down on the manufacturing costs, increases the level of automation, reduces energy consumption and decreases environmental pollution.With its patented technology, this furnace has more than just set the benchmarks for efficiency and productivity, it has created a new standard for steel casting furnaces. According to the company, the furnace is equipped with advanced technology such as automatic temperature control, high-precision weighing systems, intelligent control systems, and remote monitoring systems, which dramatically increase the performance of the furnace and reduce waste production.In addition, the Steel Casting Furnace has a high-temperature resistance material made of nano-materials, which improves its longevity and reduces maintenance costs, making it the most cost-effective and reliable option for metallurgical plants.One of the core functionalities of the furnace is that it creates an inert atmosphere, which reduces air pollution and environment impact, making it ideal for steel manufacturers who are environmentally conscious. The no-oxygen burn system achieves a low carbon emission, which can have a significant impact in reducing the greenhouse effect when compared to traditional smelting furnaces.The Steel Casting Furnace is designed to perform under the most stringent of conditions, making it perfect for the large scale, high-speed steel manufacturing operations. Its high-performance capabilities have been recognized worldwide, with the product being implemented in South-East Asia, Europe, and America.This furnace can also be customized to different manufacturing needs and conditions, which makes it possible for steel manufacturers to have a tailor-made solution suited for their individual requirements. It is available in different sizes, configurations and in electric power or gas-fired options.According to the company, the Steel Casting Furnace has numerous benefits including higher output, reduced energy consumption, and an ability to achieve cleaner melting conditions. It has a proven track record of being most cost-effective, reliable, and high-quality furnace in the market.The Steel Casting Furnace is readily available for operators, and the company has been working closely with customers to provide the best solution suitable for their steel melting process. Investing in this high-tech product may be an excellent way for companies to upgrade their production process, save on costs and increase profitability.In conclusion, the Steel Casting Furnace has revolutionized the steel making industry with its advanced features and functionalities. It has proven itself to be an efficient, reliable and cost-effective solution for steel manufacturers. The furnace has broken the boundaries of traditional smelting technology by incorporating gravity casting technology, which has revolutionized the industry. Its environmentally friendly aspect makes it an ideal solution for companies who are committed to reducing carbon emissions. The Steel Casting Furnace is expected to have a great impact on the future of the steel manufacturing industry and is a much-welcomed addition to the market.
Efficient and Eco-Friendly Melting Furnace: Revolutionizing Industrial Metal Manufacturing
Al Melting Furnace revolutionizes the Metal IndustryThe metal industry is one of the oldest and most important industries in the world, and it’s constantly evolving alongside the technological developments of modern times. One of the most important pieces of machinery in the industry is the melting furnace, which plays a critical role in the manufacturing of metal products. The latest innovation in this field is the Al Melting Furnace, which is setting new standards for efficiency, effectiveness, and safety. According to the company behind the Al Melting Furnace (need remove brand name), this equipment is designed to help businesses in the metal industry achieve superior results in terms of productivity, quality, and profitability. The Al Melting Furnace is built on the latest technology, which makes it capable of handling a wide range of materials, from iron to aluminum, while minimizing energy consumption, reducing emissions, and ensuring the purity of the end product. What makes the Al Melting Furnace stand out is its versatility. With its advanced features and customizable options, the Al Melting Furnace can be tailored to fit the needs of different businesses and industries. It comes in various sizes and capacities, with options for fuel types, controls, and automation. This flexibility enables businesses to optimize their operations, reduce costs, and improve safety and environmental standards. In addition to its performance capabilities, the Al Melting Furnace is also praised for its user-friendliness. The control panel is intuitive and easy to operate, with clear instructions and real-time data feedback. The furnace is also designed with safety in mind, featuring automatic shut-off functions, emergency stop buttons, and protection against overloading or overheating. These safety features ensure that the furnace operates efficiently and effectively without posing a risk to the operators or the environment. The Al Melting Furnace is not only a game-changer for the industry in terms of its technical capabilities, but also its environmental impact. As sustainability becomes a growing concern for businesses across all sectors, the Al Melting Furnace comes as a welcome solution to reducing emissions and waste. The furnace utilizes state-of-the-art technologies that minimize carbon footprint, conserve energy, and reduce water consumption. It also generates fewer emissions than traditional furnaces, meeting and exceeding industry standards and regulations. As businesses look to invest in advanced technology to gain a competitive edge in the market, the Al Melting Furnace proves to be a wise choice in terms of its return on investment. By optimizing operations and reducing costs, businesses can increase their profitability while also improving their environmental footprint. The Al Melting Furnace offers a long-term solution that enhances productivity, quality, and safety for businesses across the metal industry. In conclusion, Al Melting Furnace is an innovative and versatile piece of machinery that is revolutionizing the metal industry. Its advanced technology and user-friendly features make it an attractive option for businesses looking to optimize their operations and reduce their environmental impact. As the industry continues to evolve, the Al Melting Furnace is well-positioned to meet the changing needs and expectations of businesses across the metal sector. It’s no wonder why this technology is taking the industry by storm.
Refractory Brick Lining: A Guide to Enhanced Furnace Protection
Title: Industry-Leading Refractory Brick Lining: Enhancing Durability and Efficiency in High-Temperature EnvironmentsIntroduction:In a world where industries heavily rely on high-temperature environments to carry out their operations, the demand for durable and efficient refractory brick lining has seen significant growth. With a keen understanding of this market need, our company has introduced a cutting-edge refractory brick lining (brand name omitted), to provide exceptional insulation and protection in extreme heat conditions. Designed to withstand the harshest industrial processes, our refractory brick lining has quickly gained recognition as an industry-leading solution.Understanding the Importance of Refractory Brick Lining:Refractory brick lining is used extensively across industries such as steel, cement, glass, and petrochemical to create reliable insulation and protection against extreme temperatures. These linings act as a barrier between high-temperature environments and the structural elements of industrial furnaces, kilns, reactors, and other high-temperature vessels, ensuring their longevity and safe operation.Features and Benefits of our Refractory Brick Lining:1. Exceptional Thermal Insulation:Our refractory brick lining is manufactured using high-quality materials, carefully formulated to deliver outstanding thermal insulation. This feature helps minimize heat loss, enhancing energy efficiency and reducing overall operating costs.2. Superior Resistance to High Temperatures:The refractory brick lining excels in maintaining structural integrity even under extreme heat conditions. This resistance to high temperatures ensures the longevity of industrial furnaces and other heat-intensive units, minimizing downtime and production interruption.3. Enhanced Anti-Spalling Properties:The specialized formulation of our refractory brick lining provides remarkable resistance against spalling, which can occur due to rapid temperature fluctuations. This feature significantly prolongs the lining's lifespan while ensuring a safer operating environment.4. Chemical and Corrosion Resistance:Our refractory brick lining is engineered to withstand harsh chemical environments, effectively protecting the structural elements from corrosive agents such as acids, alkalis, and molten metals. This durability is crucial for industries where such aggressive substances are commonly employed.5. Increased Mechanical Strength:To withstand the mechanical stress arising from thermal cycling and material movements within the high-temperature environment, our refractory brick lining is designed with improved mechanical strength. This ensures long-term stability and reduces the need for frequent maintenance or replacements.Application Areas:The versatility and superior performance of our refractory brick lining make it suitable for a wide range of applications within industries. Some key areas where our lining finds application include:1. Steel Manufacturing:Steel production involves extremely high temperatures, demanding durable and efficient lining solutions. Our refractory brick lining provides excellent resistance to heat, chemical attack, and mechanical stress, enhancing safety and productivity in steel plants.2. Cement Production:In cement kilns, our refractory brick lining acts as a barrier against extreme temperatures, ensuring the long-lasting operation of these crucial components. Its chemical and corrosion resistance makes it ideal for resisting the aggressive chemical reactions that occur during cement production.3. Glass Manufacturing:Glass production relies heavily on uniform heating throughout the process. Our refractory brick lining helps maintain consistent high temperatures in glass furnaces, enabling flawless production and reducing energy consumption.4. Petrochemical Industry:In the petrochemical industry, where processes involve handling corrosive chemicals, our refractory brick lining serves as a protective layer, guarding against chemical attacks and high-temperature conditions. This extends the lifespan of reactors and other equipment, resulting in enhanced operational efficiency.Conclusion:As industries continue to operate in high-temperature environments, the importance of reliable refractory brick lining cannot be understated. Our refractory brick lining (brand name omitted) offers exceptional thermal insulation, resistance to high temperatures, anti-spalling properties, and chemical resistance, making it the ideal solution for various industrial settings. By incorporating our advanced lining technology, businesses can enhance the durability, efficiency, and safety of their operations, resulting in improved productivity and reduced operational costs.
The Significance of Refractory Bricks for Various Industries
Refractory Bricks Are in High Demand as Industry Looks to Increase Production EfficiencyWith industries around the world looking for ways to improve their production efficiency, refractory bricks have become an integral part of the manufacturing process. These bricks are specially designed to withstand high temperatures and resist erosion, making them ideal for use in furnaces, kilns and other high-temperature equipment. One company leading the way in the production of refractory bricks is (need remove brand name), a global leader in the development and manufacture of high-temperature materials. With over 100 years of experience in the industry, (need remove brand name) has become known for its commitment to innovation and quality, providing customers with the best possible solutions for their refractory needs. The use of refractory bricks is essential in industries such as cement, iron and steel, glass, and ceramics. The bricks are used as linings in furnaces and kilns, reducing the likelihood of equipment failure and improving overall production efficiency. With the global demand for these products continuing to rise, manufacturers such as (need remove brand name) are playing a vital role in the development of new, innovative products to meet the ever-changing needs of their customers. One such innovation is the recent development of ultra-low cement castables, which offer superior performance and versatility compared to traditional refractory products. These products are made using advanced materials and manufacturing technologies, resulting in a product with increased strength, resistance to erosion, and reduced thermal conductivity. As the world seeks to reduce carbon emissions, companies like (need remove brand name) are also creating new, environmentally friendly products that offer high-quality performance with a reduced environmental impact. One such product is the high-quality insulating brick made from recycled materials, which offers an eco-friendly alternative to traditional refractory bricks. As the demand for refractory bricks continues to grow, companies like (need remove brand name) are investing heavily in research and development to meet the needs of their customers. The company's state-of-the-art research facility is constantly developing new materials and technologies, which are tested for quality and performance before being released to the market. (need remove brand name)'s commitment to innovation and quality has earned the company an excellent reputation as a provider of high-quality refractory products. The company has a broad customer base across industries and prides itself on its ability to provide tailored solutions to meet the specific needs of its clients. With a range of products and services available, including custom designs and refractory installation, (need remove brand name) is a one-stop-shop for customers' refractory needs. In conclusion, refractory bricks have become essential components in industries where high-temperature equipment is used. Manufacturers such as (need remove brand name) are leading the way in producing high-quality, innovative products that are essential in improving the efficiency of industrial operations. With a commitment to innovation and quality, coupled with an eye towards reducing environmental impact, (need remove brand name) is poised to continue its success as a global leader in the development and manufacture of refractory products.