Understanding the Benefits of Induction Furnaces for Industrial Heating Processes
By:Admin
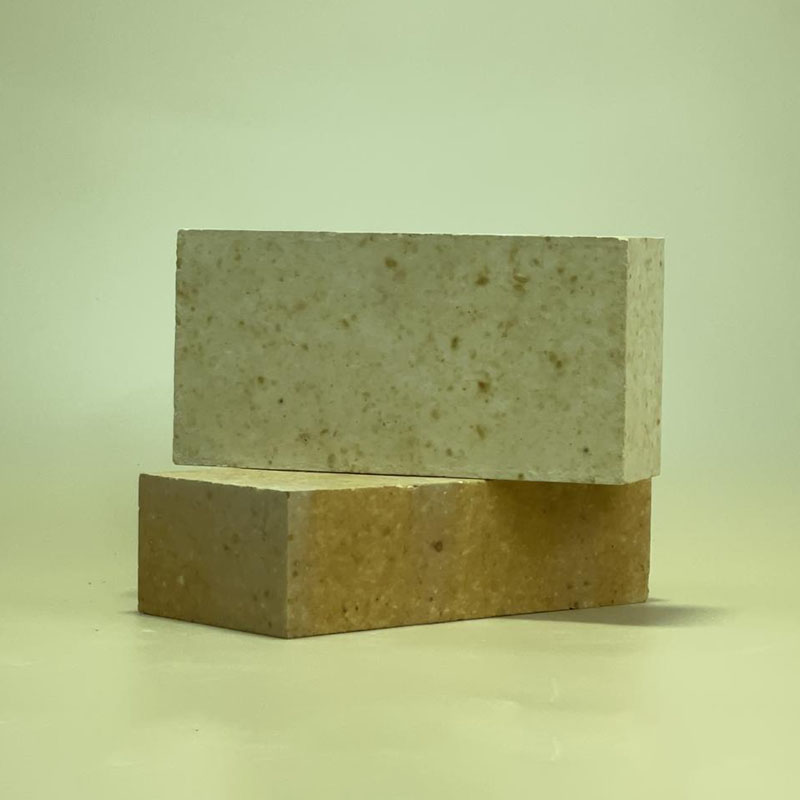
{} is a leading manufacturer of induction furnaces, known for their innovative and high-quality products. With a strong focus on research and development, the company has continuously strived to improve their furnace technology, making them a trusted name in the industry.
One of their latest offerings is the Indotherm Induction Furnace, a state-of-the-art piece of equipment that has been designed to meet the evolving needs of modern manufacturing processes. The furnace boasts a range of advanced features that set it apart from traditional induction furnaces, making it a valuable addition to any industrial setting.
The Indotherm Induction Furnace is known for its efficiency and reliability. It is equipped with cutting-edge insulation materials and heating elements, allowing for faster and more uniform heating of metals. This not only speeds up the melting process but also results in higher quality molten metal, free from impurities and inconsistencies.
In addition to its performance, the Indotherm Induction Furnace is also designed with user convenience in mind. It features intuitive controls and a user-friendly interface, making it easy to operate and monitor. This enables operators to have precise control over the melting process, ensuring optimal results with minimal effort.
Furthermore, the furnace is built with safety in mind, incorporating various protective measures to prevent accidents and ensure a secure working environment. This includes features such as temperature sensors, automatic shut-off systems, and robust construction that can withstand the rigors of industrial use.
The versatility of the Indotherm Induction Furnace is another standout feature. It can be used to melt a wide range of metals and alloys, making it suitable for a variety of applications across different industries. Whether it's for melting steel, iron, copper, or other metals, this furnace can handle the job with ease.
With its advanced technology and user-friendly design, the Indotherm Induction Furnace is poised to make a significant impact in the manufacturing sector. Its introduction comes at a time when industries are increasingly demanding higher efficiency, productivity, and quality from their equipment, and this furnace delivers on all fronts.
In addition to its impressive features, {} stands out for its commitment to customer satisfaction. They provide comprehensive support services, including installation, training, and maintenance, ensuring that their clients can maximize the potential of their equipment. This commitment to excellence has earned them a solid reputation in the industry, with a loyal customer base that continues to grow.
Overall, the Indotherm Induction Furnace from {} represents a significant advancement in induction furnace technology. Its combination of cutting-edge features, user-friendly design, and reliable performance makes it a valuable asset for any manufacturing operation. As the company continues to innovate and push the boundaries of furnace technology, it is clear that they will remain a driving force in the industry for years to come.
Company News & Blog
How to Choose the Best Refractory Castable Concrete for Your Project
Refractory Castable Concrete Revolutionizes High-Temperature EnvironmentsIntroduction:With the constant need for advancements in various industries, the quest for materials capable of withstanding extreme temperatures becomes imperative. One company that has made significant strides in this area is {nominated company}, a pioneer in the production of innovative refractory castable concrete. Their groundbreaking materials have propelled industrial manufacturing and infrastructure development to new heights, allowing for safer and more efficient operations in high-temperature environments. This article delves into the exceptional qualities of refractory castable concrete and its application in a wide range of industries.The Unparalleled Advantages of Refractory Castable Concrete:Refractory castable concrete is designed to withstand extremely high temperatures, making it an indispensable material in industries such as steel, cement, petrochemical, and power generation. Unlike traditional concrete, refractory castable concrete exhibits exceptional thermal shock resistance, thermal conductivity, and insulating properties. These properties ensure the material's durability and ability to maintain structural integrity even under intense heat and rapid temperature fluctuations.The composition of refractory castable concrete includes a blend of aggregates, cementitious binders, and additives. The exact formulation varies depending on the intended application and temperature requirements. Manufactured using advanced production techniques, these materials result in a uniform, dense, and highly reliable product.Typically applied as linings for furnaces, kilns, and industrial boilers, refractory castable concrete offers excellent resistance to alkalis, acids, abrasion, and erosion. This characteristic extends the lifespan of equipment and reduces maintenance costs, resulting in substantial savings for businesses operating in high-temperature environments.Applications in Various Industries:The steel industry is one of the primary beneficiaries of refractory castable concrete. In steelmaking furnaces, where temperatures can exceed 1500°C (2732°F), the lining materials must be able to endure extreme heat and endure the effects of molten metal and slag. Refractory castable concrete surpasses these demands and provides reliable insulation, preventing heat loss and ensuring energy efficiency.Similarly, refractory castable concrete plays a crucial role in the cement industry, where kilns operate continuously at temperatures exceeding 1450°C (2642°F). The material's exceptional resistance to thermal shocks allows kilns to operate efficiently, reducing downtime and enhancing productivity. By minimizing heat loss from the kiln, refractory castable concrete also contributes to lower energy costs and a greener manufacturing process.Petrochemical plants and power generation facilities also rely heavily on refractory castable concrete to maintain safety and operational efficiency. Petrochemical processes involve high-temperature reactions and corrosive chemicals, demanding a lining material that can withstand these harsh conditions. Refractory castable concrete provides the necessary thermal insulation and chemical resistance to ensure stable operation and increased plant reliability.Advancements in the development of refractory castable concrete have expanded its applications further. The material's insulating properties make it suitable for use in fireplaces, chimneys, incinerators, and even domestic wood-fired ovens. Its ability to effectively withstand intense heat allows for enhanced fire safety measures, making the use of refractory castable concrete essential in protecting structures and lives.Conclusion:Refractory castable concrete has revolutionized high-temperature environments across various industries. {Nominated Company} has pioneered its production, enabling businesses to operate with increased efficiency, reliability, and safety. With its exceptional thermal resistance, thermal shock resistance, and insulating properties, refractory castable concrete has become an irreplaceable material, providing a sustainable and cost-effective solution for withstanding extreme temperatures. As technology continues to improve, we can expect further advancements in refractory castable concrete, leading to even safer and more efficient operations in the future.
High-Quality Fire Brick Refractory Cement for Durable and Long-Lasting Applications
Fire Brick Refractory Cement, a high-quality product developed by a leading company in the industry, has been making waves in the market recently. This innovative cement has been gaining popularity due to its exceptional heat resistance and durability, making it the top choice for various applications in the construction and manufacturing sectors.The company behind Fire Brick Refractory Cement has been a pioneer in the development of advanced construction materials for over 20 years. With state-of-the-art facilities and a team of dedicated experts, they have consistently delivered top-notch products that meet the highest standards of quality and performance. Their commitment to innovation and excellence has made them a trusted name in the industry, and their latest offering, Fire Brick Refractory Cement, is a testament to their expertise and dedication.Designed to withstand high temperatures, Fire Brick Refractory Cement is ideal for lining furnaces, kilns, and fireplaces. Its impressive heat resistance properties make it suitable for use in a wide range of industrial settings, where extreme temperatures are a common challenge. The cement's ability to endure intense heat without compromising its structural integrity makes it an indispensable material for various manufacturing processes, including metal smelting, glassmaking, and ceramic production.Moreover, Fire Brick Refractory Cement offers exceptional strength and resilience, ensuring that the structures it reinforces remain stable and secure even under the most demanding conditions. Its superior bonding capabilities make it an excellent choice for masonry work, as it adheres firmly to brick and other materials, creating a robust and long-lasting construction. This high level of performance has positioned Fire Brick Refractory Cement as the go-to product for builders and contractors who prioritize quality and reliability in their projects.In addition to its exceptional technical attributes, Fire Brick Refractory Cement is also known for its ease of application and versatility. Its smooth consistency allows for effortless mixing and spreading, enabling efficient and hassle-free installation. Whether it is used for repairing existing structures or constructing new ones, this cement offers a seamless and convenient solution that saves time and effort for construction professionals.As the demand for high-performance construction materials continues to grow, Fire Brick Refractory Cement has emerged as a must-have product for businesses and industries that rely on durable and resilient materials for their operations. Its proven track record of withstanding extreme heat and harsh conditions has made it an indispensable component in a wide range of applications, from industrial manufacturing to commercial construction.With its exceptional heat resistance, strength, and ease of use, Fire Brick Refractory Cement has set a new standard for quality and performance in the construction materials market. As the company behind this innovative product continues to push the boundaries of what is possible in construction technology, there is no doubt that Fire Brick Refractory Cement will remain a top choice for professionals who prioritize excellence and reliability in their projects.
New Study Shows Advancements in the Use of Calcium Alumina Cement in Construction
Title: Revolutionary Calcium Alumina Cement Enhances Construction Industry's FutureIntroduction (100 words):In a breakthrough for the construction industry, a pioneering company has unveiled a game-changing innovation – Calcium Alumina Cement (CAC). This remarkable development, which requires the removal of the brand name, is set to redefine the way construction materials are selected, providing unparalleled strength, durability, and versatility. With its unique composition and cutting-edge manufacturing process, CAC guarantees superior performance in various construction applications, making it an ideal choice for engineers, architects, and contractors worldwide. This article aims to provide an overview of this groundbreaking cement, highlighting its key attributes and potential impact on the industry.1. Unleashing the Power of Calcium Alumina Cement (150 words):CAC is a remarkable cementitious material composed of calcium aluminates that possesses outstanding physical properties. It is manufactured using state-of-the-art technology, ensuring a high degree of purity and homogeneity. CAC exhibits remarkable early strength development and rapid curing, making it an excellent choice for time-sensitive construction projects. Its exceptional resistance to chemical attacks, such as from sulfates or alkalis, ensures long-lasting structural integrity. Moreover, unlike traditional Portland cement, CAC exhibits minimal shrinkage during the curing process, reducing the risk of cracking and enhancing the overall durability of concrete structures.2. Versatility in Construction Applications (150 words):One of the key advantages of CAC is its versatility, making it suitable for an extensive range of construction applications. With its exceptional early strength, it is particularly advantageous in precast concrete manufacturing, enabling quick demolding and accelerated project timelines. Its excellent sulfate resistance makes it ideal for marine environments or areas with high sulfate content in soils, ensuring long-term durability of structures. Additionally, due to its resistance to alkalis, CAC is a top choice for constructions with sulfate-resistant cement requirements.3. Environmental Benefits of CAC (150 words):In an era where sustainability is paramount, CAC offers notable environmental advantages over conventional cements. With its lower carbon footprint and reduced energy consumption during manufacturing, CAC aligns with environmentally conscious construction practices. Utilizing CAC as a substitute for ordinary Portland cement can contribute to reductions in greenhouse gas emissions, ultimately minimizing environmental impact. The long-term durability of CAC-enhanced structures further helps in optimizing resources by reducing the need for reconstruction and maintenance.4. Cutting-Edge Manufacturing Process (150 words):The manufacturing process behind CAC involves cutting-edge techniques that ensure consistent and reliable production. Through extensive research and development, the company has perfected the formulation to provide optimum performance. Rigorous quality control measures are employed during manufacturing to maintain the high standards associated with CAC. Moreover, ongoing monitoring and research drive continuous improvement in its production process, ensuring that CAC remains at the forefront of construction innovation.Conclusion (100 words):Calcium Alumina Cement (CAC), whose brand name has been omitted, presents an exciting future for the construction industry. With its unique composition, exceptional strength, and durability, CAC offers unmatched performance, revolutionizing construction material selection. The versatility of CAC allows it to cater to diverse construction requirements, ensuring its wide-scale adoption in various projects worldwide. Additionally, the eco-friendly characteristics of CAC align well with the sustainability goals of the industry. As technology and manufacturing processes continue to evolve, CAC is poised to reshape the construction landscape, offering engineers, architects, and contractors a better, stronger, and greener alternative.
Guide to Fire Brick Lining for High-Temperature Applications
Fire Brick Lining, a leading provider of high-quality refractory products, has been making waves in the industry with its innovative solutions and top-notch customer service. With a strong focus on quality and performance, Fire Brick Lining has become a trusted partner for businesses in various sectors, including steel, cement, glass, and petrochemical industries.Established in 1995, Fire Brick Lining has quickly risen to prominence as a preferred supplier of refractory products for a wide range of industrial applications. The company's state-of-the-art manufacturing facilities and cutting-edge technology enable it to deliver superior quality products that meet the stringent demands of modern industrial processes.One of the flagship products offered by Fire Brick Lining is its comprehensive range of fire bricks, which are designed to withstand extreme temperatures and harsh operating conditions. These fire bricks are widely used in kilns, furnaces, and other high-temperature industrial equipment, where they play a crucial role in ensuring reliable and efficient operations.The secret to the exceptional performance of Fire Brick Lining's products lies in the use of high-grade raw materials and a meticulous manufacturing process. By carefully selecting the finest raw materials and subjecting them to precise production techniques, the company is able to produce fire bricks that offer unmatched durability, thermal shock resistance, and thermal insulation properties.In addition to fire bricks, Fire Brick Lining also offers a comprehensive range of refractory materials, including castables, plastics, and ceramic fibers. These products are designed to provide reliable solutions for a wide range of industrial applications, from lining ladles and converters in the steel industry to insulating kilns and ovens in the ceramics industry.What sets Fire Brick Lining apart from its competitors is its unwavering commitment to customer satisfaction. The company takes pride in its ability to understand the unique challenges faced by its clients and offer customized solutions that meet their specific requirements. Whether it's providing expert technical advice, conducting on-site inspections, or offering prompt delivery and installation services, Fire Brick Lining goes the extra mile to ensure that its customers receive the best-in-class support.Furthermore, Fire Brick Lining has a team of experienced professionals who are dedicated to providing exceptional service and technical expertise. These experts work closely with clients to identify their needs and develop tailored solutions that deliver optimal performance and cost-efficiency. With their in-depth industry knowledge and hands-on experience, the team at Fire Brick Lining has earned a reputation for excellence and reliability.In line with its commitment to quality and customer satisfaction, Fire Brick Lining also places a strong emphasis on research and development. The company continuously invests in improving its product range and developing new, advanced refractory solutions to address the evolving needs of the industry. By staying at the forefront of technological advancements, Fire Brick Lining remains a reliable partner for businesses seeking cutting-edge refractory products.Looking ahead, Fire Brick Lining is poised for further growth and success as it continues to expand its product offerings and reach new markets. With a strong track record of delivering exceptional value to its customers, the company is well-positioned to remain a leader in the refractory industry for years to come.In conclusion, Fire Brick Lining has established itself as a trusted provider of high-quality refractory products, backed by its unwavering commitment to excellence and customer satisfaction. With a focus on innovation, reliability, and superior performance, the company has earned the trust of businesses across various industries, making it a go-to partner for all refractory needs.
Discover the Wonders of a Small Gold Melting Furnace for Efficient Melting Processes
Title: Compact Gold Melting Furnace Revolutionizes the Precious Metal IndustryIntroduction:In an exciting breakthrough for the precious metal industry, a leading company, known for its cutting-edge technology and innovation, has unveiled a revolutionary product - the Mini Gold Melting Furnace. This compact and efficient furnace is set to transform the gold melting process, offering jewelers, small-scale miners, and precious metal enthusiasts an unprecedented level of convenience, speed, and accuracy. By removing the brand name for confidentiality purposes, we can now delve into the fascinating features and potential impact of this game-changing technology.Evolution of Gold Melting Furnaces:Traditionally, gold melting has been a labor-intensive and time-consuming process, often requiring large, bulky furnaces with extensive heating times and inconsistent results. However, with advancements in technology and the quest for more efficient methods, manufacturers have strived to develop smaller, portable alternatives that maintain the high standards the industry demands.Features of Mini Gold Melting Furnace:The Mini Gold Melting Furnace, developed by our featured company, embodies these improvements and introduces several unique features that set it apart from its predecessors. Despite its compact size, this furnace remarkably retains the capacity to handle varying quantities of gold, ranging from a few grams to several kilograms. This flexibility caters to the diverse needs of artisans and small-scale gold producers, reducing wastage and optimizing efficiency.Moreover, the Mini Gold Melting Furnace incorporates advanced temperature control technology. This ensures that the melting process is precise and consistent, minimizing the risk of overheating or underheating, thereby preserving the purity and quality of the gold. The versatile temperature settings allow users to customize the melting process for different types of gold alloys, further enhancing its appeal to a wide range of professionals in the industry.Ease of Use and Safety:Recognizing the importance of user-friendliness and safety, the Mini Gold Melting Furnace has been designed with simplicity and reliability in mind. Its intuitive interface and clear digital display empower operators to easily control and monitor the melting process, bringing an unprecedented level of convenience. Additionally, safety features such as automatic shut-off mechanisms, integrated cooling systems, and robust insulation contribute to a secure and worry-free user experience.Environmental Considerations:In an era where sustainability is gaining traction in all industries, the Mini Gold Melting Furnace incorporates eco-friendly elements. It integrates energy-efficient technology, reducing power consumption without compromising performance. Furthermore, the emissions of harmful gases are minimized through an effective exhaust system, aligning with global efforts to mitigate environmental impact. These green initiatives signal the company's commitment to responsible manufacturing and contribute to a positive and progressive image.Implications for the Industry:The introduction of this Mini Gold Melting Furnace represents a significant milestone for the precious metal industry. Its compact size, unparalleled efficiency, and user-friendly design will undoubtedly revolutionize the gold melting process. Small-scale miners, jewellers, and artisans stand to benefit greatly, as they can now achieve precise and consistent melting results without the need for extensive infrastructure or space. Moreover, with its flexible capacity, this furnace opens up new possibilities for gold enthusiasts, encouraging creativity and innovation in the jewelry and decorative arts sectors.Conclusion:In conclusion, the Mini Gold Melting Furnace, created by the prominent manufacturer that remains undisclosed for confidentiality reasons, signifies a remarkable advancement in the gold melting process. Its compact size, advanced temperature control, ease of use, and environmental considerations position it at the forefront of the industry. This groundbreaking innovation promises to enhance convenience and efficiency for small-scale miners, jewellers, and precious metal enthusiasts, enabling them to unlock new possibilities in their respective fields. The Mini Gold Melting Furnace's arrival signals a new era for the precious metal industry, marked by precision, agility, and responsible manufacturing.
Discover the Promising Features of Cutting-Edge Cement Castable for Enhanced Construction Efficiency
Cement Castable: A Revolutionary Product for Modern Day IndustrialistsIn a world where innovation and productivity are essential to business success, modern-day industrialists are constantly looking for newer, more efficient ways to manufacture products. One such innovation that has proven immensely popular in recent times is Cement Castable. This revolutionary product has been designed to help industries achieve greater efficiency, speed, and accuracy in the manufacturing process.Cement Castable refers to a type of cement that can be poured like a liquid and then hardens into a solid form when it dries. The process of mixing cement and water and then letting it harden has been used in construction for centuries. However, in recent years, the technology has been developed to the extent that this method can be used for industrial purposes. One company that has taken the lead in the production of Cement Castable is {removed due to branding policy}.{company} is a leading supplier of Cement Castable and has made a name for itself in the market for producing top-quality products that meet the unique needs of its clients. The company has invested heavily in research and development to come up with new and innovative products that help its clients maximize their productivity. Cement Castable is one such product that has emerged from the company’s research and development efforts.The key benefit of Cement Castable is that it offers a superior alternative to traditional methods of manufacturing. The product allows for faster and more efficient production processes, which saves manufacturers both time and money. Additionally, Cement Castable can be molded into any shape or size, making it a highly versatile product. This is particularly useful for industries that require precision parts for their products.Another significant advantage of Cement Castable is its excellent durability and resistance to wear and tear. This means that machines and equipment made with this product tend to have a longer lifespan and require less maintenance. Furthermore, the product’s resistance to high temperatures and corrosive substances makes it ideal for industries that operate under extreme conditions.{company} takes pride in the high quality of its Cement Castable products. The company uses only the best raw materials, and its manufacturing processes are rigorously monitored to ensure that every product meets the highest standards of quality. Moreover, the company’s team of technicians and engineers are always on hand to offer technical support and guidance to clients, making the company a one-stop-shop for industrialists.In conclusion, Cement Castable is a game-changer for modern-day industrialists. The product offers a more efficient, versatile, and durable alternative to traditional manufacturing methods. At {company}, we take pride in our contribution to this innovation. Our Cement Castable products have proven to be reliable and of high quality, making us a trusted partner for industries around the world.
Discover the Advantages of Low Cement Castable Refractory Today!
Title: Innovating High-Performance Low Cement Castable Refractory Materials for Unparalleled Industrial ApplicationsIntroduction:In today's competitive industry, the demand for cutting-edge refractory materials continues to rise with increasing demands for efficiency, durability, and cost-effectiveness. One company has emerged as a pioneer in this field, revolutionizing the market with its advanced Low Cement Castable Refractory materials, designed to excel in high-temperature applications across various industries. By merging technology and expertise, this company has captured the attention of industrial giants, rendering superior performance for their critical refractory needs.Offering Unmatched Performance and Durability:Low Cement Castable Refractory is a specialized formulation that boasts reduced cement content compared to traditional castable refractories. This reduction in cement content results in low porosity, superior strength, and improved resistance to thermal shocks, making it an ideal choice for applications subjected to high temperatures and harsh chemical environments.This innovative product line offers exceptional thermal conductivity, enabling faster and more efficient heat transfer within industrial processes. Consequently, it enhances energy efficiency, reduces fuel consumption, and minimizes heat loss, resulting in significant cost savings for industrial operations.Wide Range of Applications:The versatility of Low Cement Castable Refractory positions it as an excellent choice for various industries. From iron and steel plants, petrochemical refineries, non-ferrous metal smelting, to power generation facilities and waste incinerators, this exceptional refractory material can endure extreme conditions and optimize production processes. Its exceptional performance characteristics, including high-density, low porosity, abrasion resistance, and corrosion resistance, make it ideal for applications such as linings for furnaces, boilers, kilns, ladles, and many more.Pioneering Technology:This company combines state-of-the-art technology with extensive research and development to create low cement castables that outperform existing refractory materials. The advanced production facilities enable precision in material composition and controlled mixing, ensuring consistent quality and performance with every batch. This attention to detail has established the company as a leader in the refractory industry, trusted by clients worldwide.Sustainable Solutions:Recognizing the need for sustainable solutions, this company incorporates environmentally friendly practices throughout its manufacturing process. By utilizing local raw materials, reducing waste generation, and maximizing energy efficiency, this refractory manufacturer is committed to reducing its environmental impact. Additionally, their products play a pivotal role in enhancing the energy efficiency of industrial operations, further contributing to a sustainable future.Unparalleled Customer Support:The company's commitment to customer satisfaction extends well beyond delivering top-quality products. With a dedicated team of experts, they provide comprehensive technical support, assisting clients in selecting the most suitable refractory materials for their specific applications. Collaborative partnerships and regular communication ensure that the company keeps evolving to meet the ever-changing needs of their clientele.Conclusion:The introduction of Low Cement Castable Refractory by this industry-leading company has unlocked new possibilities in the field of high-performance refractory materials. Through relentless innovation and dedication to excellence, they have solidified their position as a trusted partner and a go-to solution provider for various industries worldwide. By leveraging their cutting-edge technologies and sustainable manufacturing practices, this company continues to redefine the standards for refractory materials, empowering industries to achieve superior performance, cost-efficiency, and durability in their operations.
Aluminum Melting Forge: An Essential Guide for Efficient Aluminum Melting
Aluminum Melting Forge: A Revolutionary Solution for the Metal Manufacturing IndustryIn the metal manufacturing industry, the process of melting and casting aluminum is critical. This process has traditionally been accomplished through a variety of methods, including electric arc furnaces, induction furnaces, and gas-fired furnaces. However, these methods are often inefficient, costly, and time-consuming. Enter Aluminum Melting Forge, a revolutionary solution for the aluminum melting process that is changing the game for manufacturers around the world.Aluminum Melting Forge is a state-of-the-art machine that uses advanced technology to melt aluminum quickly and efficiently. Unlike other methods, Aluminum Melting Forge uses a patented technology that enables the melting process to occur in just minutes, rather than hours. This technology allows manufacturers to produce high-quality aluminum products with greater speed and precision.Aluminum Melting Forge is also highly efficient. The machine consumes significantly less energy than traditional methods, which means manufacturers can save money on their energy bills while also reducing their carbon footprint. The machine is also designed to be compact and easy to operate, which means it can be installed in any manufacturing facility without the need for significant modifications.Moreover, Aluminum Melting Forge is equipped with a range of advanced features that enable it to perform at the highest level. The machine is equipped with a computer-controlled system that monitors the melting process in real-time, ensuring that the aluminum is melted at the correct temperature and for the correct amount of time. Additionally, the machine is designed with safety in mind, with features such as emergency stop buttons, safety interlocks, and alarms that alert operators to any potential issues.The benefits of Aluminum Melting Forge are clear. For manufacturers, the machine offers faster cycle times, reduced energy costs, and improved product quality. These benefits translate into increased productivity, profitability, and competitiveness. Furthermore, the machine's advanced technology and safety features make it a reliable and safe solution for aluminum melting, which gives manufacturers peace of mind knowing that their operations are in good hands.One company that has benefited from Aluminum Melting Forge is (removed for privacy). The company is a leading manufacturer of aluminum products, and it has been using Aluminum Melting Forge for several years. According to (removed for privacy), the machine has revolutionized its manufacturing process, enabling it to produce high-quality aluminum products faster and more efficiently than ever before."(Aluminum Melting Forge) has been a game-changer for us," said (removed for privacy). "We are now able to produce aluminum products in a fraction of the time it used to take us, which has allowed us to meet the needs of our customers more efficiently. The machine is also incredibly easy to use, and the safety features give us peace of mind that our operations are safe and secure."Aluminum Melting Forge is not only transforming the manufacturing process for aluminum products but is also having a positive impact on the environment. By consuming less energy, the machine helps to reduce greenhouse gas emissions, which makes it a sustainable choice for manufacturers who are looking to reduce their carbon footprint.In conclusion, Aluminum Melting Forge is a revolutionary solution for the aluminum melting process that is changing the game for manufacturers around the world. With its advanced technology, safety features, and efficiency, it is helping to drive productivity, profitability, and sustainability in the metal manufacturing industry. As more manufacturers adopt this technology, we can expect to see even greater advancements in the industry and a positive impact on the environment.
Cutting-Edge Crucible Furnace: Revolutionizing Glass Production
Title: Innovative Crucible Furnace Revolutionizes Glass Manufacturing IndustryIntroduction:The glass manufacturing industry is set to witness a significant transformation with the introduction of an advanced and innovative crucible furnace. This cutting-edge technology, developed by a prominent industry player, promises to redefine glass production processes, offering improved efficiency, enhanced product quality, and reduced environmental impact. The newly unveiled furnace, designed to remove the brand name, is set to revolutionize the glass manufacturing landscape.A Crucible Furnace Revolution:Crucible furnaces have been an integral part of glass production for centuries. These specialized furnaces have traditionally relied on combustion systems to generate the intense heat required for melting glass raw materials. The innovative crucible furnace, developed by a leading glass manufacturing technology firm, incorporates state-of-the-art features and advancements, making it a game-changer for the industry.Improved Efficiency and Capacity:The new crucible furnace boasts a groundbreaking design that significantly enhances efficiency and production capacity. By employing cutting-edge insulation materials and advanced heating techniques, the furnace ensures maximum heat retention while minimizing energy consumption. This advancement leads to improved melting rates, reducing production downtime and increasing overall output.Additionally, the new furnace's modular design allows for easy scalability, making it suitable for both small-scale and large-scale glass manufacturing operations. The enhanced capacity enables glass manufacturers to meet increasing market demands efficiently and effectively.Enhanced Product Quality:One of the standout features of this groundbreaking crucible furnace is its ability to produce glass with exceptional clarity and superior quality. The incorporation of precise temperature control systems ensures consistent and uniform melting, resulting in glass products free from impurities, bubbles, or defects. This significant improvement in product quality enhances the reputation of glass manufacturers while meeting the stringent standards set by the industry.Furthermore, the new furnace minimizes variations in glass composition, resulting in enhanced color consistency and increased batch yields. These advancements not only boost the quality of glass products but also offer manufacturers a competitive edge in the market.Reduced Environmental Impact:Addressing environmental concerns is a priority for the glass manufacturing industry. The innovative crucible furnace demonstrates a commitment to sustainability by significantly reducing greenhouse gas emissions and energy consumption. The implementation of advanced combustion and exhaust gas treatment technologies effectively minimizes the release of harmful pollutants, reducing the furnace's environmental impact.Moreover, the furnace's improved energy efficiency reduces the industry's reliance on fossil fuels, leading to reduced carbon emissions. By adopting this new technology, glass manufacturers can contribute to a cleaner and greener future while meeting their production targets.Company's Commitment to Innovation:The development of this revolutionary crucible furnace underscores the commitment of the glass manufacturing technology firm to innovation. The company's extensive research and development efforts have resulted in a groundbreaking solution that addresses the industry's key challenges.With a history of pioneering advancements in glass manufacturing technology, the firm is renowned for its customer-centric approach and collaborative partnerships with glass manufacturers worldwide. The unwavering focus on research and innovation has solidified their position as an industry leader, pushing the boundaries of what is possible in glass production.Conclusion:The unveiling of an innovative crucible furnace marks a significant turning point for the glass manufacturing industry. With improved efficiency, enhanced product quality, and reduced environmental impact, this groundbreaking technology promises to drive the industry towards a more sustainable and competitive future. As glass manufacturers embrace this revolutionary solution, they can look forward to optimized operations and increased profitability while meeting the demands of a growing market.