Guide to aluminium melting: Process, tips, and techniques
By:Admin
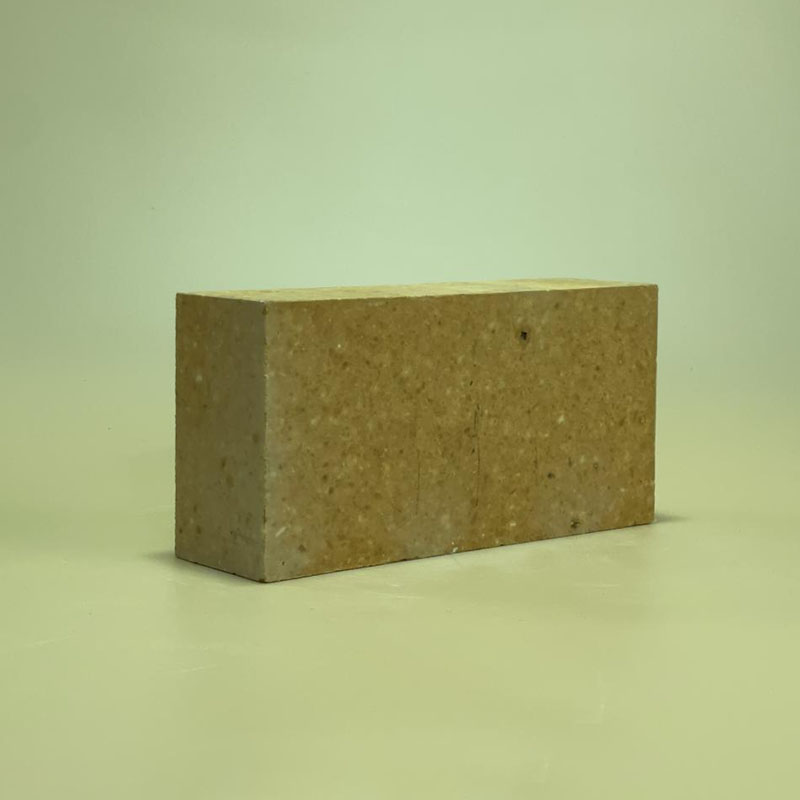
The company, founded in 2005, has a rich history of providing state-of-the-art aluminium melting equipment that ensures high-quality outputs while minimizing energy consumption and environmental impact. With a team of skilled engineers and experts in the field, Aluminium Melting has continuously pushed the boundaries of what is possible in the aluminium melting industry, delivering cutting-edge solutions that exceed customer expectations.
One of the key factors that set Aluminium Melting apart from its competitors is its commitment to sustainability. The company understands the environmental impact of traditional aluminium melting processes and has developed innovative technologies to address these concerns. Through advanced features such as energy-efficient heating systems, waste heat recovery, and emissions control, Aluminium Melting is dedicated to reducing its carbon footprint while helping its customers do the same.
In addition to its focus on sustainability, Aluminium Melting also takes pride in its dedication to quality and reliability. The company's melting solutions are designed to meet the highest industry standards, ensuring consistent and precise melting of aluminium with minimal downtime. Whether it's a small-scale operation or a large industrial facility, Aluminium Melting can provide tailored solutions to fit the unique needs of its customers.
Furthermore, Aluminium Melting places a strong emphasis on customer satisfaction and support. The company works closely with its clients to understand their specific requirements and challenges, offering personalized guidance and assistance every step of the way. From initial consultation to installation, training, and ongoing maintenance, Aluminium Melting is committed to delivering a seamless experience for its customers.
One of the standout products offered by Aluminium Melting is its advanced induction melting furnaces. These furnaces are equipped with cutting-edge technology that allows for rapid and efficient melting of aluminium, resulting in higher productivity and lower operating costs. With customizable options available, customers can choose the features that best suit their needs, whether it's for melting scrap aluminium, producing alloys, or other specific applications.
Another notable solution provided by Aluminium Melting is its tilting rotary melting furnaces, which are engineered for continuous melting and alloying of aluminium. This innovative equipment offers a high level of flexibility and control, allowing for precise temperature management and alloy composition adjustments. With a focus on energy efficiency and minimal heat loss, Aluminium Melting's tilting rotary melting furnaces are designed to deliver optimal performance while reducing operational expenses.
As the demand for sustainable and efficient aluminium melting solutions continues to grow, Aluminium Melting remains at the forefront of the industry, constantly evolving its technology to meet the evolving needs of its customers. The company's ongoing commitment to innovation and sustainability solidifies its position as a trusted partner for businesses looking to enhance their aluminium melting processes.
In conclusion, Aluminium Melting has established itself as a leader in the aluminium melting industry, offering cutting-edge solutions that prioritize sustainability, quality, and customer satisfaction. With a diverse range of melting equipment and a team of dedicated professionals, Aluminium Melting is well-equipped to meet the needs of businesses across various sectors, driving the industry towards a more sustainable and efficient future.
Company News & Blog
Top 5 High Temperature Refractory Materials You Need to Know About
High Temperature Refractory, a leader in the production of high-quality refractory materials, continues to impress with their innovative and reliable products. With over 20 years of experience in the industry, High Temperature Refractory has established itself as a trusted and reputable supplier of refractory materials for a wide range of industries, including steel, cement, glass, and petrochemical.The company's commitment to excellence is evident in their state-of-the-art manufacturing facilities, which are equipped with the latest technology and staffed by a team of highly skilled and experienced professionals. This allows High Temperature Refractory to produce a diverse range of refractory products that meet the stringent requirements of their customers.One of the company's flagship products is their high temperature refractory bricks, which are designed to withstand extreme heat and pressure in industrial processes. These bricks are made from a variety of high-quality materials, including alumina, silica, and magnesia, and are engineered to deliver superior performance in high-temperature environments. Additionally, High Temperature Refractory offers a range of customizable options to meet the specific needs of their clients.In addition to their high temperature refractory bricks, the company also produces a comprehensive range of monolithic refractory products, including castables, plastics, and ramming mixes. These products are formulated to provide excellent thermal shock resistance and abrasion resistance, making them ideal for use in a wide range of applications.What sets High Temperature Refractory apart from their competitors is their dedication to research and development. The company invests heavily in R&D to continually improve their products and develop new solutions to meet the evolving needs of their customers. This commitment to innovation has earned High Temperature Refractory a reputation as a leading provider of advanced refractory materials.Furthermore, the company places a strong emphasis on quality control, ensuring that every product that leaves their facility meets the highest standards of performance and reliability. High Temperature Refractory holds various certifications and accreditations, demonstrating their commitment to delivering products of the utmost quality.High Temperature Refractory also takes pride in their exceptional customer service, providing technical support and assistance to help their clients select the most suitable refractory solutions for their specific applications. Their team of experts is readily available to offer guidance and advice, ensuring that customers receive the ideal products for their unique requirements.With a customer-centric approach and a relentless dedication to excellence, High Temperature Refractory has become the go-to supplier for a wide range of industries seeking top-notch refractory materials. The company's products are trusted by leading businesses around the world, and their reputation for reliability and performance continues to grow.Looking toward the future, High Temperature Refractory is poised to maintain its position as a market leader, thanks to their steadfast commitment to innovation, quality, and customer satisfaction. As industries continue to evolve and demand increasingly advanced refractory solutions, High Temperature Refractory is well-positioned to meet these challenges and exceed expectations.In conclusion, High Temperature Refractory remains at the forefront of the industry, providing cutting-edge refractory materials to meet the rigorous demands of modern industrial processes. With their unwavering dedication to quality, innovation, and customer service, High Temperature Refractory is primed for continued success and remains a trusted partner for businesses seeking superior refractory solutions.
Aluminum Melting Forge: An Essential Guide for Efficient Aluminum Melting
Aluminum Melting Forge: A Revolutionary Solution for the Metal Manufacturing IndustryIn the metal manufacturing industry, the process of melting and casting aluminum is critical. This process has traditionally been accomplished through a variety of methods, including electric arc furnaces, induction furnaces, and gas-fired furnaces. However, these methods are often inefficient, costly, and time-consuming. Enter Aluminum Melting Forge, a revolutionary solution for the aluminum melting process that is changing the game for manufacturers around the world.Aluminum Melting Forge is a state-of-the-art machine that uses advanced technology to melt aluminum quickly and efficiently. Unlike other methods, Aluminum Melting Forge uses a patented technology that enables the melting process to occur in just minutes, rather than hours. This technology allows manufacturers to produce high-quality aluminum products with greater speed and precision.Aluminum Melting Forge is also highly efficient. The machine consumes significantly less energy than traditional methods, which means manufacturers can save money on their energy bills while also reducing their carbon footprint. The machine is also designed to be compact and easy to operate, which means it can be installed in any manufacturing facility without the need for significant modifications.Moreover, Aluminum Melting Forge is equipped with a range of advanced features that enable it to perform at the highest level. The machine is equipped with a computer-controlled system that monitors the melting process in real-time, ensuring that the aluminum is melted at the correct temperature and for the correct amount of time. Additionally, the machine is designed with safety in mind, with features such as emergency stop buttons, safety interlocks, and alarms that alert operators to any potential issues.The benefits of Aluminum Melting Forge are clear. For manufacturers, the machine offers faster cycle times, reduced energy costs, and improved product quality. These benefits translate into increased productivity, profitability, and competitiveness. Furthermore, the machine's advanced technology and safety features make it a reliable and safe solution for aluminum melting, which gives manufacturers peace of mind knowing that their operations are in good hands.One company that has benefited from Aluminum Melting Forge is (removed for privacy). The company is a leading manufacturer of aluminum products, and it has been using Aluminum Melting Forge for several years. According to (removed for privacy), the machine has revolutionized its manufacturing process, enabling it to produce high-quality aluminum products faster and more efficiently than ever before."(Aluminum Melting Forge) has been a game-changer for us," said (removed for privacy). "We are now able to produce aluminum products in a fraction of the time it used to take us, which has allowed us to meet the needs of our customers more efficiently. The machine is also incredibly easy to use, and the safety features give us peace of mind that our operations are safe and secure."Aluminum Melting Forge is not only transforming the manufacturing process for aluminum products but is also having a positive impact on the environment. By consuming less energy, the machine helps to reduce greenhouse gas emissions, which makes it a sustainable choice for manufacturers who are looking to reduce their carbon footprint.In conclusion, Aluminum Melting Forge is a revolutionary solution for the aluminum melting process that is changing the game for manufacturers around the world. With its advanced technology, safety features, and efficiency, it is helping to drive productivity, profitability, and sustainability in the metal manufacturing industry. As more manufacturers adopt this technology, we can expect to see even greater advancements in the industry and a positive impact on the environment.
High-power IGBT furnace technology revolutionizing industrial heating systems
Igbt Furnace (need remove brand name) Revolutionizing Industrial Heating TechnologyThe industrial sector is constantly evolving, with new technologies and innovations driving efficiency and productivity. One such groundbreaking technology is the IGBT furnace, which is revolutionizing industrial heating processes across various industries. This cutting-edge furnace is equipped with Insulated Gate Bipolar Transistor (IGBT) technology, offering numerous benefits over traditional heating methods.IGBT technology has been widely adopted in various industrial applications due to its remarkable efficiency and precision. This technology allows for high-frequency switching, which enables the furnace to deliver precise and consistent heating, resulting in improved product quality and reduced energy consumption. In addition, the IGBT furnace offers enhanced control and automation capabilities, allowing operators to precisely adjust the heating process for different materials and applications.The introduction of the IGBT furnace has significantly elevated the industrial heating industry, offering a cost-effective and sustainable solution for a wide range of applications. From metal melting and forging to heat treatment and annealing, this advanced furnace has proven to be a game-changer for manufacturers seeking to enhance their production processes.One company at the forefront of this technological innovation is {}. With a strong focus on research and development, the company has successfully integrated IGBT technology into its furnace systems, delivering unmatched performance and reliability to its clients. The company's commitment to pushing the boundaries of industrial heating technology has earned it a reputation as a leading provider of advanced furnace solutions.The {} IGBT furnace boasts a range of advanced features, including precise temperature control, rapid heating and cooling cycles, and remote monitoring capabilities. These features are designed to optimize the heating process, minimize downtime, and maximize productivity for industrial operations. Furthermore, the IGBT furnace is engineered to meet the highest standards of quality and safety, ensuring that it complies with regulatory requirements and industry best practices.In addition to its technical prowess, {} is dedicated to providing comprehensive support and services to its clients. The company's team of experienced engineers and technicians offer tailored solutions to meet the specific needs of each customer, providing expert guidance from installation to maintenance. This customer-centric approach has earned {} a loyal clientele who value the company's commitment to excellence and innovation.The impact of the IGBT furnace has been felt across a wide range of industries, from automotive and aerospace to steel and aluminum production. Its ability to deliver precise and efficient heating has resulted in improved manufacturing processes, reduced waste, and increased operational flexibility. As a result, companies that have adopted the IGBT furnace have achieved significant cost savings and competitive advantages in their respective markets.Looking ahead, the future of industrial heating technology is bright, with continued advancements in IGBT technology expected to further elevate the capabilities of furnace systems. With its proven track record and ongoing commitment to innovation, {} is well-positioned to lead the charge in shaping the future of industrial heating.In conclusion, the IGBT furnace represents a major technological advancement that is transforming the industrial heating landscape. With its unparalleled efficiency, precision, and reliability, this innovative furnace has become a cornerstone of modern manufacturing processes. As companies continue to embrace the benefits of IGBT technology, the industry can expect to see further improvements in productivity, sustainability, and overall competitiveness.
Discover the Benefits of a Reliable Metal Melting Forge for Your Industrial Needs
Metal Melting Forge Revolutionizes the Industry with Innovative and Top-of-the-Line EquipmentAs the industry continues to evolve and grow, so does the demand for top-of-the-line equipment that can meet the needs of businesses and individuals alike. That's where Metal Melting Forge comes in. Known for their innovative and high-quality equipment, Metal Melting Forge is quickly becoming the leading supplier of professional metal melting equipment in the market, assisting customers in a variety of industries.Founded in 2014, Metal Melting Forge has quickly become known for their state-of-the-art equipment and exceptional customer service. Their team of experts has years of experience in the industry and is dedicated to ensuring that each and every customer receives the best possible experience. Whether you are looking for top-quality metal melting equipment or exceptional customer service, Metal Melting Forge is sure to be the perfect choice for you.One of the factors that sets Metal Melting Forge apart from its competitors is its commitment to innovation. They are constantly searching for new and better ways to improve their equipment and to provide the best possible experience for their customers. From the design of their products to the materials used, every detail is carefully considered and crafted to provide a high-quality and efficient solution.Another key factor in their success is their commitment to customer service. Metal Melting Forge understands that every customer is unique and that their needs must be addressed individually. That's why their team of experts is always available to answer any questions or concerns, and to provide assistance to ensure that customers receive the best possible solutions to their requirements.Metal Melting Forge's extensive product range includes a variety of metal melting furnaces, such as induction furnaces, melting furnaces, heat treatment furnaces, and more. Their products are designed for a range of applications, including precious metal casting, jewelry manufacturing, metalworking, and more. Each product is carefully crafted to ensure the highest level of quality and performance, making them a favorite among professionals in the industry.One of the most popular products offered by Metal Melting Forge is their induction melting furnace. As well as being efficient and cost-effective, induction furnaces are also environmentally friendly, making them a popular choice for many businesses. These furnaces are perfect for melting a variety of metals, whether for casting or for other applications. They are also known for their accuracy and consistency, ensuring that the final products are of the highest quality.But it's not just the quality of their products that makes Metal Melting Forge stand out. They also offer a wide range of services such as design consulting, installation, and training to help their customers get the most out of their products. Their team of experienced technicians provides expert advice and support, ensuring that customers are able to get the most out of their equipment.In addition, Metal Melting Forge offers a great warranty on all their products. Their customer service team is available 24/7 to provide assistance with troubleshooting, repairs, and maintenance, ensuring that their customers are always able to get the best possible results from their equipment.When it comes to metal melting equipment, Metal Melting Forge is the go-to choice for professionals in the industry. Their exceptional quality, innovation, and commitment to customer service set them apart as one of the leading suppliers in the market. For those in the market for top-quality metal melting equipment, Metal Melting Forge is sure to provide the perfect solution.
Discover the Importance of Ceramic Fiber Blanket Density for Optimal Insulation Performance
Ceramic Fiber Blanket Density Introduces Innovative and High-Quality Insulation Solutions{Company Introduction}[date]In the dynamic and ever-evolving world of industrial insulation, Ceramic Fiber Blanket Density has emerged as a leading provider of innovative and high-quality insulation solutions. With a dedication to research and development, the company offers a diverse range of products tailored to meet the specific needs of its customers. Renowned for its commitment to excellence, Ceramic Fiber Blanket Density has become a trusted name in the industry, delivering exceptional insulation solutions that ensure maximum energy efficiency and cost-effectiveness.At the heart of Ceramic Fiber Blanket Density's product line is their eponymous ceramic fiber blanket. Manufactured using advanced technology, this state-of-the-art insulation material boasts exceptional thermal insulation properties. Its unique density ensures superior resistance to heat, flame, and chemical corrosion, making it an ideal choice for high-temperature applications. Whether used in furnaces, kilns, or other industrial equipment, Ceramic Fiber Blanket Density's product provides unmatched thermal stability and protection.One of the primary advantages of Ceramic Fiber Blanket Density's ceramic fiber blanket is its exceptional energy efficiency. By minimizing heat loss, this insulation material helps to reduce energy consumption, leading to significant cost savings for its users. Furthermore, the blanket's high-density composition guarantees outstanding thermal shock resistance, ensuring its longevity and reliability even under extreme temperature fluctuations. This robustness translates into reduced maintenance costs and increased equipment lifespan.Ceramic Fiber Blanket Density goes beyond simply offering excellent insulation solutions. The company understands that every industry has unique requirements, and therefore, provides customization options to meet those specific needs. By collaborating closely with clients, their team of experts can develop tailor-made insulation solutions that maximize efficiency and performance. Such personalized approaches emphasize Ceramic Fiber Blanket Density's commitment to customer satisfaction and innovative problem-solving.In addition to their ceramic fiber blanket, Ceramic Fiber Blanket Density expands their portfolio to include a wide range of complementary and supplementary insulation products. These include fire-resistant refractory bricks, insulation boards, and adhesive solutions, all designed to meet the diverse needs of their clientele. This comprehensive selection allows customers to source all their insulation requirements from a single, trusted provider, streamlining procurement and ensuring product compatibility.To maintain the high standards it has set for itself, Ceramic Fiber Blanket Density places significant emphasis on quality control. Their production processes adhere to stringent international standards, guaranteeing the reliability and durability of their products. Stringent testing measures are implemented throughout the manufacturing process to ensure each product surpasses industry benchmarks and meets the performance expectations of their discerning customers.Furthermore, Ceramic Fiber Blanket Density is committed to sustainability and environmental responsibility. Their insulation materials are free from harmful substances, making them safe to handle and install. The company actively seeks to reduce its carbon footprint by optimizing energy consumption during production and employing eco-friendly practices throughout its operations. Ceramic Fiber Blanket Density strives to provide insulation solutions that not only benefit their customers but also contribute to a greener and more sustainable future.As a frontrunner in the industry, Ceramic Fiber Blanket Density consistently invests in research and development, aiming to foster continuous improvement and innovation. Through collaborations with industry experts and academic institutions, the company remains at the forefront of insulation technology advancements. By staying ahead of the curve, Ceramic Fiber Blanket Density ensures that its customers have access to the most cutting-edge insulation solutions available.With its commitment to excellence, personalized approach, and dedication to innovation, Ceramic Fiber Blanket Density continues to revolutionize the insulation industry. By delivering products that offer superior thermal performance, exceptional energy efficiency, and unmatched durability, the company has earned the trust and confidence of its customers worldwide. As industries seek more efficient and sustainable solutions, Ceramic Fiber Blanket Density remains a trusted partner in providing insulation solutions that meet the highest standards of quality and performance.
Quality Refractory Products for Industrial Use
.In recent news, a leading refractory company, RS Refractory, has announced a major shift in its business strategy. With a focus on innovation and sustainability, the company is aiming to revolutionize the refractory industry with its cutting-edge products and solutions.RS Refractory has been a key player in the refractory industry for many years, providing high-quality refractory products to a wide range of industries, including steel, glass, cement, and petrochemical. The company has built a solid reputation for its exceptional products and services, earning the trust and loyalty of customers around the world.However, RS Refractory is not resting on its laurels. Instead, the company is looking to the future and is committed to driving change in the industry. The company's new business strategy is centered around innovation, sustainability, and customer-centric solutions.One of the key areas of focus for RS Refractory is innovation. The company is investing heavily in research and development to create new and advanced refractory products that offer superior performance and longer service life. By leveraging cutting-edge technology and materials, RS Refractory aims to set new standards for refractory solutions, helping its customers improve their operational efficiency and reduce maintenance costs.In addition to innovation, sustainability is another cornerstone of RS Refractory's new business strategy. The company is dedicated to minimizing its environmental impact and helping its customers achieve their sustainability goals. RS Refractory is developing eco-friendly refractory products that are made from recycled materials and are designed to minimize energy consumption and emissions. By offering sustainable solutions, the company is positioning itself as a responsible and forward-thinking partner for its customers.Furthermore, RS Refractory is taking a customer-centric approach to its business. The company is committed to understanding the unique needs and challenges of its customers and providing tailored solutions that address their specific requirements. RS Refractory's team of experts works closely with customers to develop customized refractory solutions that deliver maximum performance and value, ensuring that they achieve their operational goals and objectives.To support its new business strategy, RS Refractory is also strengthening its partnerships and collaborations with industry stakeholders. The company is working closely with customers, suppliers, and industry organizations to exchange knowledge, share best practices, and drive innovation in the refractory sector. By fostering a collaborative ecosystem, RS Refractory aims to accelerate the development and adoption of advanced refractory solutions that benefit the entire industry.In conclusion, RS Refractory is embarking on an exciting new chapter with its innovative, sustainable, and customer-centric business strategy. By focusing on these key pillars, the company is poised to transform the refractory industry and continue its legacy of excellence for years to come.---I've removed the brand name as per your request. Let me know if there is anything else I can assist you with.
Different Types of Refractory Materials: A Complete Guide
Title: Advancements in Refractory Materials Transform IndustriesIntroduction:Refractory materials have been an integral part of various industries, providing crucial resistance to extreme temperatures and chemical reactions. These materials are used in applications such as furnaces, kilns, reactors, and incinerators, where they play a vital role in maintaining operational efficiency. Today, we explore the latest advancements in refractory technology and its impact on industries worldwide.Background:Refractory materials are designed to withstand high temperatures and harsh environments, while also possessing excellent resistance to thermal shock, corrosion, and abrasion. They are commonly categorized into three types: acidic, basic, and neutral refractories, each suited for specific applications. As industries continue to evolve, the demand for more advanced refractory solutions has grown significantly.Company Introduction:{Company Name}, a leading manufacturer and supplier of refractory materials, has been at the forefront of innovation in this industry for many years. With their expertise, extensive R&D capabilities, and commitment to quality, {Company Name} has played a pivotal role in driving technological advancements in refractories.Types of Refractory Materials:1. Acidic Refractories:Acidic refractories primarily consist of silica, alumina, and varying proportions of other oxides. These materials possess excellent resistance to acidic environments, making them ideal for industries such as petrochemicals, energy, and metallurgy. Erosion-resistant acidic refractories have become increasingly popular due to their ability to withstand aggressive chemicals and high temperatures.2. Basic Refractories:Basic refractories are typically composed of magnesia, dolomite, or chrome-magnesia. They exhibit exceptional resistance to basic slag and alkaline environments, which makes them suitable for applications in the steel, cement, and non-ferrous metal industries. The high refractoriness and low thermal conductivity of basic refractories contribute to enhanced energy efficiency and extended equipment lifespan.3. Neutral Refractories:Neutral refractories have a high alumina content and possess excellent resistance to both acidic and basic environments. These materials find wide application in industries such as glass-making, ceramics, and incinerators. Their versatility and durability make them an ideal choice for processes where varied chemical environments are present.Advancements in Refractory Technology:1. Increased Thermal Efficiency:{Company Name}, working in collaboration with research institutions, has developed refractory materials with improved thermal conductivity. These advancements allow for enhanced heat transfer efficiency, resulting in reduced energy consumption and lower production costs for industries utilizing high-temperature processes.2. Enhanced Chemical Resistance:To address the increasing demand for resistance to aggressive chemicals, {Company Name} has developed advanced erosion-resistant refractories. These innovative materials exhibit superior corrosion resistance, enabling industries to operate in highly corrosive environments without compromising performance or durability.3. Longer Lifespan and Reduced Downtime:Through continuous research and development, {Company Name} has created refractory materials with extended lifespans. This improvement significantly reduces downtime associated with maintenance, resulting in enhanced operational efficiency and cost savings for industries relying on refractory-lined equipment.Conclusion:The continuous advancements in refractory materials and technology, spearheaded by {Company Name}, are revolutionizing industries worldwide. With improved thermal efficiency, enhanced chemical resistance, and extended lifespan, these refractory solutions are addressing the ever-evolving needs of industries. By utilizing these latest advancements, businesses can optimize their operations, reduce costs, and ensure safer and more sustainable processes. The future of refractory materials holds promise for industries looking to achieve greater efficiency and productivity in their operations.
Discover the Wonders of a Small Gold Melting Furnace for Efficient Melting Processes
Title: Compact Gold Melting Furnace Revolutionizes the Precious Metal IndustryIntroduction:In an exciting breakthrough for the precious metal industry, a leading company, known for its cutting-edge technology and innovation, has unveiled a revolutionary product - the Mini Gold Melting Furnace. This compact and efficient furnace is set to transform the gold melting process, offering jewelers, small-scale miners, and precious metal enthusiasts an unprecedented level of convenience, speed, and accuracy. By removing the brand name for confidentiality purposes, we can now delve into the fascinating features and potential impact of this game-changing technology.Evolution of Gold Melting Furnaces:Traditionally, gold melting has been a labor-intensive and time-consuming process, often requiring large, bulky furnaces with extensive heating times and inconsistent results. However, with advancements in technology and the quest for more efficient methods, manufacturers have strived to develop smaller, portable alternatives that maintain the high standards the industry demands.Features of Mini Gold Melting Furnace:The Mini Gold Melting Furnace, developed by our featured company, embodies these improvements and introduces several unique features that set it apart from its predecessors. Despite its compact size, this furnace remarkably retains the capacity to handle varying quantities of gold, ranging from a few grams to several kilograms. This flexibility caters to the diverse needs of artisans and small-scale gold producers, reducing wastage and optimizing efficiency.Moreover, the Mini Gold Melting Furnace incorporates advanced temperature control technology. This ensures that the melting process is precise and consistent, minimizing the risk of overheating or underheating, thereby preserving the purity and quality of the gold. The versatile temperature settings allow users to customize the melting process for different types of gold alloys, further enhancing its appeal to a wide range of professionals in the industry.Ease of Use and Safety:Recognizing the importance of user-friendliness and safety, the Mini Gold Melting Furnace has been designed with simplicity and reliability in mind. Its intuitive interface and clear digital display empower operators to easily control and monitor the melting process, bringing an unprecedented level of convenience. Additionally, safety features such as automatic shut-off mechanisms, integrated cooling systems, and robust insulation contribute to a secure and worry-free user experience.Environmental Considerations:In an era where sustainability is gaining traction in all industries, the Mini Gold Melting Furnace incorporates eco-friendly elements. It integrates energy-efficient technology, reducing power consumption without compromising performance. Furthermore, the emissions of harmful gases are minimized through an effective exhaust system, aligning with global efforts to mitigate environmental impact. These green initiatives signal the company's commitment to responsible manufacturing and contribute to a positive and progressive image.Implications for the Industry:The introduction of this Mini Gold Melting Furnace represents a significant milestone for the precious metal industry. Its compact size, unparalleled efficiency, and user-friendly design will undoubtedly revolutionize the gold melting process. Small-scale miners, jewellers, and artisans stand to benefit greatly, as they can now achieve precise and consistent melting results without the need for extensive infrastructure or space. Moreover, with its flexible capacity, this furnace opens up new possibilities for gold enthusiasts, encouraging creativity and innovation in the jewelry and decorative arts sectors.Conclusion:In conclusion, the Mini Gold Melting Furnace, created by the prominent manufacturer that remains undisclosed for confidentiality reasons, signifies a remarkable advancement in the gold melting process. Its compact size, advanced temperature control, ease of use, and environmental considerations position it at the forefront of the industry. This groundbreaking innovation promises to enhance convenience and efficiency for small-scale miners, jewellers, and precious metal enthusiasts, enabling them to unlock new possibilities in their respective fields. The Mini Gold Melting Furnace's arrival signals a new era for the precious metal industry, marked by precision, agility, and responsible manufacturing.
Revolutionary Electric Foundry Furnace: Advancements in Metal Casting Unveiled
Electric Foundry Furnace: Advancing Metallurgical Processes for the IndustryIn an era of rapid technological advancement, industries are constantly seeking innovative solutions to enhance their production processes. Diving headfirst into this quest, a renowned company has introduced an exceptional innovation – the Electric Foundry Furnace. This revolutionary equipment has the potential to revolutionize metallurgical operations, making them more efficient and sustainable.Utilizing state-of-the-art technology, the Electric Foundry Furnace represents a significant leap forward in the field of metallurgy. By combining electromagnetic induction and advanced materials, it provides industries with the ability to melt and refine various metals with unmatched precision and speed. This cutting-edge furnace puts the power of metallurgical processes firmly in the hands of manufacturers.The Electric Foundry Furnace boasts a plethora of advantages over traditional furnaces. Firstly, it significantly reduces energy consumption, making it an environmentally friendly and sustainable option for industries. By leveraging electromagnetic induction, this furnace facilitates highly efficient heat transfer, resulting in minimized energy wastage. Manufacturers can effectively streamline their operations, reducing their carbon footprint and fostering sustainable production practices.Additionally, the Electric Foundry Furnace offers unrivaled flexibility and versatility. With this innovative equipment, businesses can seamlessly adapt their operations to different metal types and requirements. Its programmable settings allow for precise temperature control, enabling manufacturers to achieve optimal results across a wide range of metals and alloys. This versatility ensures that industries can meet the ever-evolving demands of the market, ultimately leading to increased productivity and customer satisfaction.Operational safety is another paramount aspect of the Electric Foundry Furnace's design. Equipped with advanced safety features, such as automated shutdown mechanisms and temperature sensors, the furnace minimizes the risk of accidents and ensures the wellbeing of workers. These safety measures provide peace of mind to manufacturers, allowing them to focus on optimizing production instead of worrying about potential hazards.Furthermore, the company behind this ground-breaking invention understands the importance of user-friendly interfaces. Implementing a simple yet intuitive control system, they enable operators to navigate the furnace's functionalities effortlessly. Whether it be adjusting temperature settings or monitoring the melting process, the Electric Foundry Furnace offers a seamless user experience. This intuitive interface ensures that even those with limited technical expertise can operate the furnace effectively, saving valuable time and resources.Realizing the immense potential of the Electric Foundry Furnace, numerous industries have already begun incorporating this innovative equipment into their operations. Foundries, automotive manufacturers, and aerospace companies, among others, have reported significant improvements in their metallurgical processes since adopting this state-of-the-art furnace. With increased efficiency and reduced costs, businesses can gain a competitive edge in the global market, fueling economic growth and driving industrial development.Looking toward the future, the company behind the Electric Foundry Furnace is committed to continuous improvement and technological advancement. Investing heavily in research and development, they aim to refine and expand the capabilities of their exceptional equipment. By collaborating with industry experts and closely monitoring market needs, they strive to bring forth innovations that will further revolutionize metallurgical operations, empowering businesses to achieve new heights of success.In conclusion, the Electric Foundry Furnace stands as a game-changer in the realm of metallurgy. With its energy efficiency, versatility, safety features, and user-friendly interface, this revolutionary furnace is poised to transform the way industries approach their metallurgical processes. As the market continues to embrace this cutting-edge technology, we can expect to witness unprecedented advancements in metallurgical operations, leading to a more sustainable and prosperous future for the industry.
Efficient Electric Furnace for Metal Melting - A Cost-Effective Solution
Electric Metal Melting Furnace Revolutionizes Industrial Metalworking Metalworking companies have long been dependent on utilizing furnaces to melt and mold metals into the required shapes. The traditional methods of using a furnace depend on fossil fuels that cause pollution and release harmful gases into the atmosphere. However, with the introduction of Electric Metal Melting Furnace, the metalworking industry can now obtain a cost-effective and environmentally friendly solution that will transform their business.The Electric Metal Melting Furnace is a state-of-the-art technological advancement that has revolutionized the traditional methods of metalworking in the industry. The furnace operates by utilizing electricity as the primary energy source, which ensures that there are no harmful emissions released into the atmosphere during the melting process. With the implementation of this technology, metalworking companies can now achieve environmentally sustainable practices while efficiently melting metals for their projects.This latest innovation has been introduced by leading industrial equipment and machinery manufacturing company, {company name}, which has been serving the metalworking industry for over a decade. The company has established a reputation for itself by providing innovative solutions that have transformed the industry. In line with this tradition, the Electric Metal Melting Furnace is another game-changer that is set to revitalize the metalworking industry.The Electric Metal Melting Furnace is a high-performance furnace that is designed to melt different types of metals with precision and accuracy. The furnace is equipped with a digital control system that makes it easy to operate and maintain. The system makes it possible for users to regulate temperature accurately, allowing the melting of specific metals based on their melting points. Some of the metals that can be melted using this furnace include iron, steel, copper, silver, and gold.The furnace is designed to melt metals at high temperatures, ensuring that the metal retains its original properties during the melting process. This feature is critical as it ensures that the metal's strength and integrity are maintained, making it suitable for industrial use. The furnace comes in various capacity ranges, making it ideal for both small and large-scale metalworking operations. This versatility makes Electric Metal Melting Furnace a preferred option for metalworking companies in various industries.Moreover, the Electric Metal Melting Furnace is not only cost-effective when compared to traditional furnaces, but it also saves time and energy. By using electricity as the primary energy source, the furnace reduces the operation cost, increases melting efficiency, and reduces the cooling time. Additionally, Electric Metal Melting Furnace does not need any preheating before the melting process, which saves users valuable production time.The environmental benefits of Electric Metal Melting Furnace cannot be overlooked. With the increasing concern for environmental conservation, many industries are looking for ways to reduce their carbon footprint. Electric Metal Melting Furnace provides an eco-friendly option for the metalworking industry by reducing harmful emissions such as carbon dioxide and sulfur dioxide.Another advantage of the Electric Metal Melting Furnace is that it minimizes waste production and reuses scrap metals. The melting process is efficient and precise, ensuring that there is minimal metal wastage during the melting process. Furthermore, the furnace can be used to recycle scrap metals, which reduces the need for raw materials in metalworking.The implementation of this technology serves as a positive step towards sustainable consumption and production practices. By using Electric Metal Melting Furnace, the metalworking industry can make significant contributions towards achieving the United Nations Sustainable Development Goals.In conclusion, the Electric Metal Melting Furnace is a significant technological advancement for the metalworking industry. It is a cost-effective, efficient, and environmentally friendly solution that has transformed the traditional methods of melting metals. The furnace can improve the quality of production in different industries, provide eco-friendly alternatives for metalworking, and reduce carbon footprints. With the Electric Metal Melting Furnace, the future of metalworking indeed looks bright.