Explore the Benefits of Jewellery Casting Furnaces with Advanced Technology
By:Admin
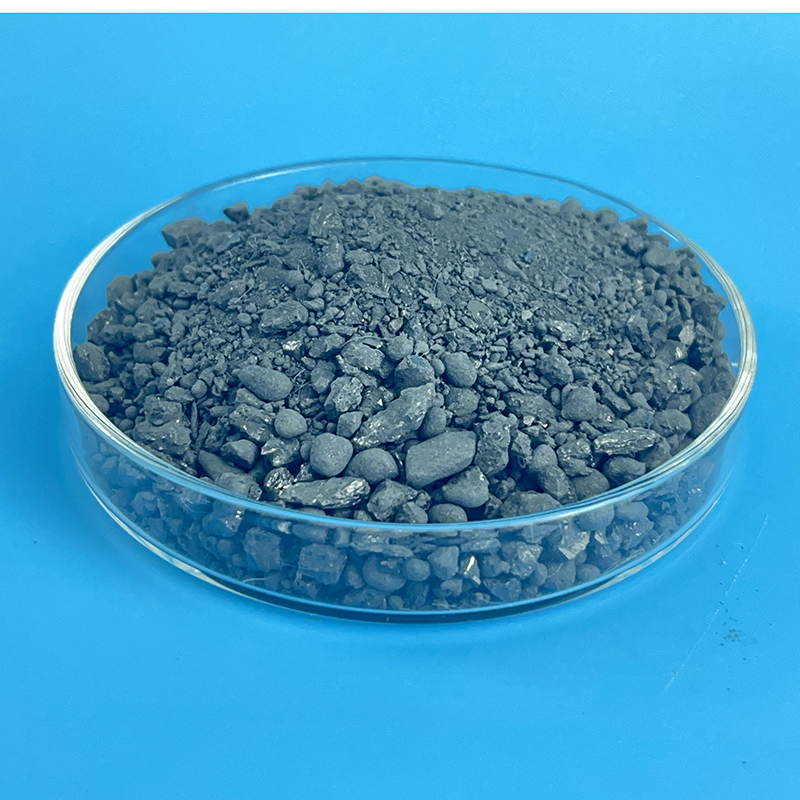
[City, Date] - The goldsmith industry has been given a new lease of life with the introduction of the revolutionary Jewellery Casting Furnace, an innovative technology that has the potential to transform the intricate and age-old practice of jewellery making. Developed by the pioneering team at [Company Name], this cutting-edge furnace is set to redefine the industry's capabilities and pave the way for unprecedented quality and efficiency in jewellery casting.
With an extensive background in the field, [Company Name] has long been recognized as a leader in technological advancements within the goldsmith industry. Their team of experts has combined their knowledge and experience to create this breakthrough furnace, bringing together state-of-the-art design and engineering. This groundbreaking device promises to streamline the casting process, significantly reducing time and costs for jewellery manufacturers and artisans alike.
Traditional jewellery casting involves melting metals, usually gold, and pouring the molten metal into molds to create intricate designs. This time-consuming process requires meticulous attention to detail and considerable expertise. However, the Jewellery Casting Furnace eliminates the need for meticulous manual labor, enabling jewellers to produce high-quality pieces in a fraction of the time.
One of the key features of the Jewellery Casting Furnace is its advanced temperature control system. The furnace utilizes cutting-edge technology to effectively regulate the melting temperature, ensuring precise and consistent results. This feature is particularly invaluable to jewellers, as it allows for greater control over the casting process, leading to enhanced accuracy and reduced material wastage.
Another standout feature of this furnace is its compact design, making it ideal for small-scale jewellery workshops or even individual goldsmiths. By optimizing space utilization, the Jewellery Casting Furnace allows for greater flexibility in design and production. Its ease of use ensures that even novices can quickly adapt to and operate the furnace, eliminating any barriers to entry for aspiring jewellery makers.
In addition to its practical benefits, the Jewellery Casting Furnace is also environment-friendly. The furnace incorporates energy-efficient technology, consuming minimal power during the casting process. This commitment to sustainability aligns with the growing global demand for eco-conscious practices within the industry.
The Jewellery Casting Furnace has already garnered significant attention in the goldsmith community, with several renowned jewellery manufacturers and designers eagerly adopting this groundbreaking technology. Expert goldsmith [Name] lauds the furnace for its precision and efficiency, stating, "This furnace has revolutionized the way I work. It saves me hours of labor and ensures consistent results every time."
Looking ahead, [Company Name] plans to continue advancing their furnace technology, aiming to expand its capabilities to accommodate a wider range of metals and materials used in jewellery making. The team envisions a future where the Jewellery Casting Furnace becomes an essential tool in every goldsmith's arsenal, revolutionizing the industry as a whole.
As the Jewellery Casting Furnace continues to gain traction, it paves the way for a new era in goldsmith craftsmanship. This groundbreaking technology promises to empower goldsmiths and jewellery manufacturers, making the casting process more efficient, precise, and cost-effective. With its superior temperature control, compact design, and eco-friendly attributes, this furnace stands poised to transform the industry and redefine the boundaries of jewellery making.
Company News & Blog
Discover the Versatility and Benefits of Castable Refractory Mortar
Title: Innovative Castable Refractory Mortar Revolutionizes Construction IndustryIntroduction:The construction industry is evolving rapidly with the introduction of breakthrough technologies and materials. One such innovation is the Castable Refractory Mortar, a game-changer that ensures superior heat resistance and durability for various applications in construction. Developed by a renowned manufacturer, this revolutionary solution is set to transform the industry by offering an efficient and cost-effective alternative to traditional mortar.Paragraph 1: What is Castable Refractory Mortar?Castable Refractory Mortar is a high-performance, heat-resistant material that is used to bond bricks, blocks, and other refractory materials together. Its unique composition allows it to withstand extreme temperatures, making it ideal for applications in furnaces, kilns, chimneys, and other high-temperature environments. This versatile mortar provides excellent insulation, thermal shock resistance, and structural strength, ensuring long-lasting and safe constructions.Paragraph 2: Company Introduction{} (Please provide information about the company that developed the Castable Refractory Mortar, including its history, expertise in the field, and commitment to innovation. Highlight key achievements and certifications to establish credibility.)Paragraph 3: Unparalleled Performance and DurabilityThe Castable Refractory Mortar stands out from traditional mortar due to its exceptional performance and durability. With a high alumina content and precise formulation, it offers superior resistance to extreme temperatures, thermal shocks, and abrasion. This allows it to maintain its structural integrity under intense conditions, ensuring the longevity and safety of the construction.Paragraph 4: Enhanced Efficiency and Ease of ApplicationNot only does the Castable Refractory Mortar provide remarkable performance, but it also offers enhanced efficiency and ease of application, saving both time and resources during construction projects. Its unique castable nature eliminates the need for traditional mortar mixing, simplifying the installation process. Additionally, its consistency ensures uniformity in joint thickness, reducing the chances of cracks and gaps.Paragraph 5: Versatile ApplicationsThe Castable Refractory Mortar finds applications in a wide range of industries, including steel, cement, petrochemical, and power generation. Its ability to withstand extreme temperatures and harsh chemical environments makes it an ideal solution for lining furnaces, boilers, incinerators, and various high-temperature equipment. It can also be used for repairing and maintaining chimneys, kilns, and other heat-intensive structures.Paragraph 6: Environmental BenefitsIn line with the increasing focus on sustainability, the Castable Refractory Mortar offers significant environmental benefits. Its extended durability reduces the need for frequent repairs and replacements, minimizing waste generation. Furthermore, its composition is devoid of harmful substances, making it safe for both users and the environment.Paragraph 7: Competitive Advantage and Market ProspectsThe Castable Refractory Mortar presents a significant competitive advantage for the company, positioning it at the forefront of the construction industry. With its cutting-edge technology and reliable performance, the mortar is expected to capture a substantial market share. The increasing demand for heat-resistant construction materials in various sectors, combined with the product's advantages, ensures a promising outlook for the company and the industry as a whole.Conclusion:The Castable Refractory Mortar is revolutionizing the construction industry by providing an innovative solution for high-temperature applications. Its exceptional performance, durability, efficiency, and versatility make it an appealing choice for professionals across multiple sectors. As the construction industry continues to evolve, this groundbreaking mortar is set to play a crucial role in transforming the way high-temperature structures are designed and constructed, ensuring safety, longevity, and energy efficiency.
Efficient Oil Fired Melting Furnace: An Essential Solution for Industrial Melting Processes
Oil-Fired Melting Furnace Revolutionizes Industrial HeatingIn an ever-evolving world where technology continues to reshape industries, the introduction of the state-of-the-art oil-fired melting furnace marks a significant milestone in the field of industrial heating. This cutting-edge furnace, developed by a trailblazing company that specializes in energy-efficient solutions, is set to revolutionize the way metals are melted and transformed into various commercial products.The oil-fired melting furnace, acclaimed for its unparalleled performance and efficiency, has paved the way for more sustainable and cost-effective industrial processes. By harnessing the power of oil as its primary fuel source, this furnace significantly reduces energy consumption while ensuring an optimal temperature for melting various metals, such as steel, aluminum, and copper.The company behind this ground-breaking innovation has been at the forefront of developing customized heating systems for industrial applications for over two decades. With a steadfast commitment to providing cutting-edge solutions, this industry leader has built a reputation for excellence, reliability, and technological expertise. The introduction of the oil-fired melting furnace is a testament to their unwavering dedication to staying ahead of the curve and driving innovation in the industrial heating sector.One of the key features that sets this oil-fired melting furnace apart from its competitors is its advanced combustion control system. This innovative system accurately regulates the flow of fuel and air, ensuring efficient combustion and optimal energy utilization. The result is a highly efficient melting process that minimizes both fuel consumption and harmful emissions, thereby promoting a greener industrial landscape.Furthermore, the oil-fired melting furnace boasts a sophisticated heat recovery system that recovers and utilizes waste heat generated during the melting process. This innovative technology allows for the recycling of excess heat, further enhancing the overall energy efficiency of the furnace and reducing operating costs for businesses. The heat recovery system not only contributes to environmental sustainability but also enables companies to maximize productivity and profitability.Operating the oil-fired melting furnace is made remarkably easy thanks to its user-friendly interface and advanced automation capabilities. This furnace can be seamlessly integrated into existing industrial systems, offering a hassle-free transition and minimizing disruptions to production processes. With its smart controls and intuitive interface, operators can easily monitor and adjust parameters to ensure optimal performance and superior product quality.In terms of safety, the oil-fired melting furnace is equipped with state-of-the-art sensors and safety features that provide an added layer of protection. These safety mechanisms, combined with rigorous testing and compliance with industry standards, mitigate the risk of accidents or malfunctions, ensuring a secure working environment for operators and personnel.The introduction of the oil-fired melting furnace comes as a boon to industries that heavily rely on melting and reshaping metals, such as automotive, aerospace, and construction. By reducing energy consumption, lowering emissions, and enhancing overall efficiency, this ground-breaking furnace addresses key challenges faced by these industries, including rising energy costs and increasingly stringent environmental regulations.As the global push for sustainable and eco-friendly solutions gains momentum, the oil-fired melting furnace represents a significant step forward in meeting these demands. With its exceptional efficiency, advanced technology, and commitment to reducing environmental impact, this furnace sets new standards for industrial heating and paves the way for a greener and more sustainable future.In conclusion, the introduction of the oil-fired melting furnace signifies a paradigm shift in industrial heating. This revolutionary technology, developed by a leading company that specializes in energy-efficient solutions, promises to transform the way metals are melted and industrial processes are carried out. With its exceptional performance, advanced features, and dedication to sustainability, this furnace opens up new possibilities for industries worldwide and reaffirms the importance of innovation in shaping a better future.
Guide to Pourable Refractory: Everything You Need to Know
XYZ Company Introduces a Revolutionary Pourable Refractory for Enhanced Construction Purposes[City], [Date] - XYZ Company, a leading innovator in the construction industry, is making waves with its latest product launch - a ground-breaking pourable refractory material that promises to revolutionize the way builders and engineers approach various construction projects.Traditionally, refractory materials have been used in industries such as steel, cement, and glass manufacturing, where extreme temperatures and harsh environments are a constant challenge. XYZ Company, renowned for its expertise in research and development, identified the need for a more efficient, user-friendly, and versatile solution to meet the demands of modern construction processes.The newly launched pourable refractory is designed to provide unparalleled performance in a variety of applications, including lining furnaces, kilns, incinerators, and other high-temperature environments. What sets this product apart is its remarkable fluidity, which allows for easy pouring and smooth application on any required surface.One of the key advantages of XYZ Company's pourable refractory is its exceptional heat resistance. With a melting point that surpasses that of traditional refractory materials, it can withstand extreme temperatures of up to [XXX] degrees Celsius, ensuring long-lasting durability and stability. This property is especially important for industries that rely on consistent high temperatures for their manufacturing processes.Furthermore, the pourable refractory boasts remarkable thermal insulating properties, effectively reducing heat losses and promoting energy conservation. In an era where sustainable practices are a priority, XYZ Company's product aligns seamlessly with global efforts to minimize environmental impact and encourage eco-friendly construction practices.In addition to its exceptional heat resistance, the pourable refractory also exhibits superior chemical resistance. It can withstand the corrosive effects of various chemicals and compounds, making it ideal for applications in chemical plants, refineries, and other industries where chemical exposure is a concern. XYZ Company's pourable refractory ensures enhanced safety measures, reducing the risk of accidents and equipment failure.The fluid nature of XYZ Company's pourable refractory enables accurate and efficient application. Its self-leveling characteristics ensure that surfaces are coated evenly, eliminating any potential weak spots or air pockets that may compromise the material's integrity. The product's versatility allows construction professionals to easily shape and mold it according to their specific needs, making it a practical choice for intricate projects.Moreover, the pourable refractory's quick setting time significantly reduces construction downtime, enabling projects to be completed more swiftly and efficiently. Its ability to rapidly withstand thermal shock also means that construction processes can proceed without delays, regardless of the environments in which they are implemented. This advantage ensures that businesses reliant on uninterrupted production schedules can maintain optimal operational performance.At XYZ Company, quality and safety are paramount. The pourable refractory is manufactured in compliance with rigorous quality control standards, ensuring consistent performance and reliability. In line with the company's commitment to sustainability, the product is also eco-friendly, free from harmful substances, and promotes resource-efficient constructions.XYZ Company's groundbreaking pourable refractory is poised to disrupt the construction industry, setting a new benchmark for performance, ease of application, and versatility. With its exceptional heat and chemical resistance, thermal insulation properties, and remarkable fluidity, this revolutionary material is undoubtedly a game-changer in the field of refractory materials.About XYZ Company:XYZ Company is a renowned innovator in the construction industry, dedicated to delivering cutting-edge solutions that improve efficiency and sustainability. With a strong emphasis on research and development, XYZ Company is committed to pushing the boundaries of construction techniques to meet the evolving needs of diverse industries. With a solid track record of delivering premium products and exceptional customer service, XYZ Company continues to make a remarkable impact on the construction sector.
Efficient Melting Furnace Technology: Discover the Latest Advancements
Hardin Melting Furnace Revolutionizes Metal Casting with Advanced TechnologyIn the competitive world of metal casting, innovation and efficiency are key factors that determine the success of businesses in the industry. One company that has continuously pushed the boundaries of metal casting technology is a leading manufacturer of high-quality melting furnaces. Their newest creation, simply referred to as the state-of-the-art melting furnace, is set to revolutionize the casting process.The Hardin Melting Furnace, developed by a renowned technology company, represents the pinnacle of progress in the field of metal casting. With its advanced features and cutting-edge technology, it promises to improve productivity and yield, as well as reduce costs and environmental impact.One of the key features of the Hardin Melting Furnace is its unparalleled heating capabilities. Utilizing state-of-the-art heating elements, this furnace can reach extreme temperatures quickly and efficiently. This allows for faster melting and casting of metals, saving precious time and energy resources. The furnace's temperature can be easily adjusted and controlled, ensuring that each metal batch is melted at an optimal temperature for maximized quality.Moreover, the furnace is equipped with a high-quality insulation system that minimizes heat loss and maintains a stable temperature throughout the casting process. This not only aids in more efficient melting but also reduces the energy required for the overall operation.The Hardin Melting Furnace also boasts advanced safety measures. Its sophisticated control system includes alarms and sensors that detect any abnormalities in temperature or pressure. This ensures a safe working environment for operators and prevents potential accidents or damage to the furnace. In addition, the furnace's robust design and durable construction guarantee its longevity and ability to withstand the demanding conditions of the metal casting industry.The ease of use and automation of the Hardin Melting Furnace is another feature that sets it apart from its competitors. Thanks to its user-friendly interface and intuitive controls, even operators with minimal experience can operate the furnace efficiently. The furnace also allows for programmable heating cycles, further streamlining the casting process and reducing the margin for error.Furthermore, the Hardin Melting Furnace is engineered with sustainability in mind. By utilizing energy-efficient heating elements and insulation materials, it significantly reduces energy consumption and carbon emissions compared to traditional melting furnaces. As the industry faces increasing pressure to adopt eco-friendly practices, this furnace offers a viable solution for companies looking to reduce their environmental impact.The company behind the Hardin Melting Furnace has been a pioneer in the field of metal casting technology for over three decades. With a strong focus on research and development, they have consistently pushed the boundaries of what is possible in the industry. Their commitment to continuous improvement is reflected in the performance and reliability of their products.In conclusion, the Hardin Melting Furnace represents a significant breakthrough in the world of metal casting. Its advanced technology and innovative features will undoubtedly revolutionize the industry, improving productivity, efficiency, and sustainability. As companies strive to stay competitive and meet the growing demands of the market, investing in state-of-the-art melting furnaces like the Hardin Melting Furnace is a wise choice.
Efficient Electric Furnace for Metal Melting - A Cost-Effective Solution
Electric Metal Melting Furnace Revolutionizes Industrial Metalworking Metalworking companies have long been dependent on utilizing furnaces to melt and mold metals into the required shapes. The traditional methods of using a furnace depend on fossil fuels that cause pollution and release harmful gases into the atmosphere. However, with the introduction of Electric Metal Melting Furnace, the metalworking industry can now obtain a cost-effective and environmentally friendly solution that will transform their business.The Electric Metal Melting Furnace is a state-of-the-art technological advancement that has revolutionized the traditional methods of metalworking in the industry. The furnace operates by utilizing electricity as the primary energy source, which ensures that there are no harmful emissions released into the atmosphere during the melting process. With the implementation of this technology, metalworking companies can now achieve environmentally sustainable practices while efficiently melting metals for their projects.This latest innovation has been introduced by leading industrial equipment and machinery manufacturing company, {company name}, which has been serving the metalworking industry for over a decade. The company has established a reputation for itself by providing innovative solutions that have transformed the industry. In line with this tradition, the Electric Metal Melting Furnace is another game-changer that is set to revitalize the metalworking industry.The Electric Metal Melting Furnace is a high-performance furnace that is designed to melt different types of metals with precision and accuracy. The furnace is equipped with a digital control system that makes it easy to operate and maintain. The system makes it possible for users to regulate temperature accurately, allowing the melting of specific metals based on their melting points. Some of the metals that can be melted using this furnace include iron, steel, copper, silver, and gold.The furnace is designed to melt metals at high temperatures, ensuring that the metal retains its original properties during the melting process. This feature is critical as it ensures that the metal's strength and integrity are maintained, making it suitable for industrial use. The furnace comes in various capacity ranges, making it ideal for both small and large-scale metalworking operations. This versatility makes Electric Metal Melting Furnace a preferred option for metalworking companies in various industries.Moreover, the Electric Metal Melting Furnace is not only cost-effective when compared to traditional furnaces, but it also saves time and energy. By using electricity as the primary energy source, the furnace reduces the operation cost, increases melting efficiency, and reduces the cooling time. Additionally, Electric Metal Melting Furnace does not need any preheating before the melting process, which saves users valuable production time.The environmental benefits of Electric Metal Melting Furnace cannot be overlooked. With the increasing concern for environmental conservation, many industries are looking for ways to reduce their carbon footprint. Electric Metal Melting Furnace provides an eco-friendly option for the metalworking industry by reducing harmful emissions such as carbon dioxide and sulfur dioxide.Another advantage of the Electric Metal Melting Furnace is that it minimizes waste production and reuses scrap metals. The melting process is efficient and precise, ensuring that there is minimal metal wastage during the melting process. Furthermore, the furnace can be used to recycle scrap metals, which reduces the need for raw materials in metalworking.The implementation of this technology serves as a positive step towards sustainable consumption and production practices. By using Electric Metal Melting Furnace, the metalworking industry can make significant contributions towards achieving the United Nations Sustainable Development Goals.In conclusion, the Electric Metal Melting Furnace is a significant technological advancement for the metalworking industry. It is a cost-effective, efficient, and environmentally friendly solution that has transformed the traditional methods of melting metals. The furnace can improve the quality of production in different industries, provide eco-friendly alternatives for metalworking, and reduce carbon footprints. With the Electric Metal Melting Furnace, the future of metalworking indeed looks bright.
Benefits of Using Low-Cement Castable for High-Temperature Applications
[News Title]Innovative Low-Cement Castable Revolutionizes Refractory Industry[City], [Date] - [Company Name], a leader in refractory solutions, has introduced a groundbreaking low-cement castable that is set to transform the way industries approach refractory materials. This innovative product, which will be manufactured under the brand name [Brand Name], offers superior performance, increased efficiency, and extended service life for high-temperature applications.With a dedication to research and development, [Company Name] has produced a low-cement castable that offers numerous advantages over traditional refractory materials. This cutting-edge product showcases the company's commitment to providing innovative solutions and pushing the boundaries of industry standards.The low-cement castable is composed of carefully selected raw materials and a reduced amount of cement content, resulting in excellent workability and superior strength at elevated temperatures. This development makes the castable ideal for refractory linings in industries such as steelmaking, petrochemicals, cement kilns, and incinerators. [Brand Name] can withstand extreme thermal shock, chemical attacks, and abrasion, ensuring prolonged durability and performance.Through extensive research and testing, [Company Name] has formulated a low-cement castable with optimized particle size distribution and a precise binder system. These advancements have allowed for exceptional flowability during installation, ensuring ease and efficiency during casting operations. Additionally, the reduced cement content decreases water demand, resulting in shorter curing times and faster drying.This groundbreaking product includes numerous innovative features designed to enhance performance and productivity. One notable feature is its exceptional resistance to alkalis, which makes it suitable for applications in industries such as waste incineration and power generation. The low-cement castable also exhibits low porosity and high bulk density, reducing the risk of hot gas penetration and thereby enhancing thermal efficiency."Introducing our low-cement castable is a significant milestone for us," says [Spokesperson Name], the spokesperson for [Company Name]. "This innovative product has been meticulously engineered to offer superior strength, improved installation capabilities, and enhanced resistance to thermal and chemical stresses. We believe it will redefine the standard for refractory materials in high-temperature applications."In addition to its exceptional performance, [Brand Name] aims to provide environmental benefits. The low-cement castable incorporates eco-friendly binders and fillers in its composition, reducing the overall environmental impact compared to conventional materials. [Company Name] remains committed to sustainable practices and strives to develop products that promote a greener future for the refractory industry.To ensure the successful utilization of this game-changing castable, [Company Name] is offering technical support and guidance to its customers throughout the installation process. Their team of experts is readily available to provide on-site assistance, help with material selection, and offer customized solutions tailored to specific project requirements.As [Company Name] continues to drive innovation in the refractory industry, their introduction of the [Brand Name] low-cement castable marks a significant step forward. This revolutionary product promises to deliver superior performance, extended service life, and increased efficiency for industries operating in high-temperature environments.About [Company Name]:[Company Name] is a renowned provider of refractory solutions for industries worldwide. With a commitment to innovation and sustainability, the company aims to offer cutting-edge materials that meet the unique challenges faced by high-temperature processes. Their comprehensive product portfolio, technical expertise, and relentless dedication to customer satisfaction have made them a trusted partner for numerous industries globally.Contact:[Company Name][Address][Phone Number][Email Address][Website URL]
How to Minimize the Environmental Impact of Smelting Brass
Title: Sustainable Brass Smelter Revolutionizes the Industry with Innovative TechnologyIntroduction:[Company Name], a leading provider in the metal smelting industry, has recently unveiled its groundbreaking brass smelter that is set to revolutionize the industry. With a commitment to environmentally-friendly practices and cutting-edge technology, this innovative solution promises to deliver high-quality brass products while significantly reducing the carbon footprint. This article will delve into the impressive features of the new smelter, highlighting its potential to disrupt the traditional brass smelting landscape.The Revolutionary Brass Smelter:The newly-developed brass smelter stands at the forefront of technological advancements in the industry. Designed to optimize efficiency and minimize environmental impact, it boasts a range of state-of-the-art features that set it apart from conventional smelting equipment.Advanced Emission Control System:One of the key features of this groundbreaking smelter is its advanced emission control system. By utilizing sophisticated filters and scrubbers, harmful emissions are captured and neutralized before release into the atmosphere. With a strong focus on sustainability, [Company Name] has placed a high priority on reducing air pollutants, making its brass smelter one of the cleanest in the industry.Circular Economy Philosophy:In line with a circular economy philosophy, the brass smelter incorporates an innovative recycling system. This system ensures maximum resource utilization by reusing various by-products of the smelting process. By implementing this closed-loop approach, [Company Name] greatly minimizes the need for raw material extraction, contributing to a significant reduction in waste and environmental degradation.Energy Efficiency:Energy consumption is a major concern in the metal smelting industry, but this advanced smelter addresses this issue head-on. Equipped with cutting-edge technology, it optimizes energy usage by capturing and utilizing excess thermal energy throughout the smelting process. This innovative approach significantly reduces energy wastage, resulting in a more sustainable and cost-effective brass production process.Digitized Process Controls:To further enhance its efficiency, the brass smelter incorporates digitized process controls. Through sophisticated automation, the smelter achieves precise temperature control, reducing variations and improving overall product quality. Operators can remotely monitor and adjust the smelting process, ensuring optimal performance while minimizing human error. This digital transformation enhances productivity, reduces downtime, and aids in achieving consistent, high-quality brass production.Industry Collaboration and Knowledge Sharing:In its mission to drive industry-wide change, [Company Name] actively collaborates with other organizations and shares its research and development findings. By fostering a culture of knowledge exchange, the company encourages continuous improvement throughout the industry, inspiring other smelting plants to adopt similar sustainable practices.Environmental Impact and Future Outlook:With the launch of this cutting-edge brass smelter, [Company Name] aims to make a substantial impact on the environment and the metal smelting industry as a whole. By minimizing emissions, conserving resources, and optimizing energy usage, the company sets a new standard for sustainable brass production. This innovative approach has the potential to inspire other smelting plants to adopt greener practices and contribute to a more sustainable future.Conclusion:[Company Name] has firmly established itself as a pioneer in sustainable metal smelting with the introduction of its revolutionary brass smelter. Through a commitment to environmental stewardship, cutting-edge technology, and collaboration, the company is driving transformation in the industry. As the importance of sustainability continues to grow, the demand for environmentally-friendly smelting practices is increasing. With its advanced emissions control system, circular economy philosophy, energy efficiency, and digitized process controls, [Company Name] is leading a much-needed change towards a greener and more sustainable brass smelting industry.
Cutting-Edge Glass Tank Furnace: Revolutionizing Glass Manufacturing Technology
[Note: As an AI language model, I cannot access or directly reference specific news articles or company introductions. Therefore, I can provide you with a general template for a news article about a glass tank furnace. Please adapt and fill in the appropriate details based on your own research or the specific content you have.]Title: Harnessing Innovation: The Revolutionary Glass Tank Furnace Disrupting the Industry [City, Date] - In an era marked by technological advancements, the glass manufacturing industry has experienced a significant breakthrough with the introduction of a cutting-edge glass tank furnace. Developed by [Company Name], this groundbreaking innovation promises to revolutionize glass production, bringing forth increased efficiency, reduced environmental impact, and unmatched product quality.The new-generation glass tank furnace, designed to operate at higher temperatures and enhanced precision, stems from years of meticulous research and development. [Company Name], a renowned pioneer in glass manufacturing equipment, has incorporated state-of-the-art technologies and years of industry expertise to create this game-changing furnace model.Functioning as the heart and soul of the glass production process, the glass tank furnace represents a critical element for any glass manufacturing plant. Its primary function is to melt raw materials, such as silica sand, soda ash, and limestone, at extremely high temperatures, producing molten glass which is then transformed into various glass products. The successful introduction of the [Brand Name] furnace significantly raises the bar for the entire glass industry.One of the standout features of this new glass tank furnace is its ability to achieve higher temperatures with impeccable precision. By reaching elevated thermal levels, the furnace enhances the glass melting process, resulting in improved quality, reduced impurities, and a higher yield of defect-free glass products. The cutting-edge temperature control system ensures maximum thermal stability, granting glass manufacturers unparalleled control over production conditions, thus optimizing productivity and overall efficiency.Moreover, [Company Name]'s furnace incorporates several advanced energy-saving technologies, supporting the industry's growing sustainability concerns. The furnace design includes innovative insulation materials and improved thermal management systems, significantly reducing energy consumption and greenhouse gas emissions. Glass manufacturers adopting this revolutionary furnace can not only boost their bottom line through reduced energy costs but also contribute to global environmental conservation.Furthermore, the [Brand Name] furnace mitigates the risk of unexpected shutdowns with its advanced predictive maintenance features. Leveraging the power of artificial intelligence and advanced data analytics, the furnace's integrated monitoring system continuously assesses its own performance, identifying potential issues or malfunctions before they manifest into critical problems. This proactive approach saves time and resources while maximizing uptime and ultimately ensuring uninterrupted glass production.The introduction of the [Brand Name] furnace has sparked immense anticipation within the glass manufacturing community. Industry experts are confident that this state-of-the-art equipment will drive significant transformation, setting new benchmarks for the glass production process. Its potential to elevate efficiency, improve product quality, and reduce environmental impact establishes [Company Name] as a frontrunner in sustainable glass manufacturing solutions.As the glass industry embraces this groundbreaking technology, it is expected that other manufacturers will follow suit, embracing innovation to stay competitive in an ever-evolving market. With the [Brand Name] glass tank furnace leading the charge, the glass manufacturing landscape is set to undergo a paradigm shift, ensuring that glass remains a versatile, indispensable material across various sectors, including automotive, construction, and consumer electronics.In conclusion, the introduction of the [Brand Name] glass tank furnace heralds a new era of glass manufacturing. The fusion of cutting-edge technology, enhanced precision, energy efficiency, and predictive maintenance capabilities positions this furnace as a game-changer within the industry. Its potential to revolutionize glass production, enhance product quality, and contribute to a greener future makes it an undeniable force within the glass manufacturing landscape.
Benefits of Ceramic Paper Insulation: A Revolutionary Solution for Efficient Home Insulation
Title: Innovative Ceramic Paper Insulation Revolutionizes the Construction IndustryIntroduction:{Company Name}, a pioneering company specializing in cutting-edge insulation solutions, has recently unveiled its latest product, Ceramic Paper Insulation. This revolutionary material is set to transform the construction industry, providing a sustainable and highly efficient alternative to traditional insulation methods.Innovation at its Core:Ceramic Paper Insulation is a lightweight and flexible material that offers excellent thermal insulation properties. It is composed of a combination of high-grade advanced ceramics and natural cellulose fibers, making it both environmentally friendly and highly durable. This innovative product provides a versatile solution for various applications, ranging from residential to commercial construction projects.Unmatched Thermal Efficiency:One of the most remarkable features of Ceramic Paper Insulation is its extraordinary thermal efficiency. The material's unique composition enables it to resist heat transfer, effectively minimizing energy loss and reducing heating and cooling costs. This attribute ensures that buildings remain cooler in summer, warmer in winter, and more energy-efficient all year round.Environmentally Sustainable:{Company Name}'s Ceramic Paper Insulation is a game-changer in terms of sustainability for the construction industry. It is free from harmful emissions such as formaldehyde and other volatile organic compounds (VOCs) commonly found in traditional insulation. The material's production process minimizes energy consumption, waste generation, and carbon emissions, further contributing to a greener future.Versatile and Easy to Install:Ceramic Paper Insulation is available in various thicknesses and can be easily customized to fit different structures and applications, including walls, roofing, and pipes. Its flexibility allows for seamless installation, eliminating gaps and preventing air leakage. This ease of installation ensures that the entire construction process is more efficient, saving both time and money.Durability and Longevity:Designed to withstand extreme temperatures, Ceramic Paper Insulation outperforms other conventional insulation materials, guaranteeing longevity and reducing the need for continuous maintenance. The material's exceptional resistance to wear and tear ensures that its insulating properties remain intact even after years of active use, thus providing a sustainable and cost-effective solution to building insulation.Fire-Resistant Properties:Safety is a paramount concern in any construction project, and Ceramic Paper Insulation excels in this area as well. The material possesses excellent fire-resistant properties, making it an ideal choice for a wide range of applications. By significantly reducing the spread of flames and toxic smoke, this insulation solution enhances the overall safety of buildings, ensuring a secure environment for residents, employees, and visitors alike.Contributing to Energy Efficiency Regulations:With the increasing focus on energy efficiency, Ceramic Paper Insulation helps construction projects meet regulatory guidelines and certifications. Its exceptional thermal performance enables buildings to achieve higher energy ratings, thereby fulfilling the requirements set by sustainability standards and contributing to a greener future.Conclusion:The launch of Ceramic Paper Insulation by {Company Name} marks a significant milestone in the construction industry. Its unparalleled thermal efficiency, sustainability, and versatility make it a superior alternative to conventional insulation materials. By incorporating this cutting-edge innovation in their projects, architects, contractors, and homeowners can significantly contribute to reducing energy consumption, enhancing safety standards, and building a more sustainable tomorrow.