- Home
- Blog
- Discover the Importance of Ceramic Fiber Blanket Density for Optimal Insulation Performance
Discover the Importance of Ceramic Fiber Blanket Density for Optimal Insulation Performance
By:Admin
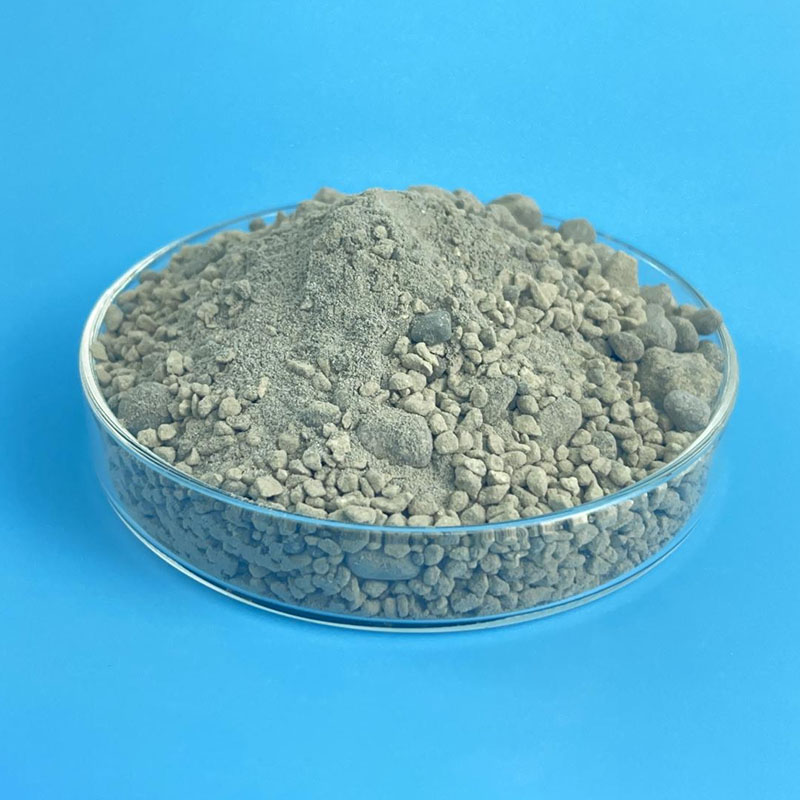
{Company Introduction}
[date]
In the dynamic and ever-evolving world of industrial insulation, Ceramic Fiber Blanket Density has emerged as a leading provider of innovative and high-quality insulation solutions. With a dedication to research and development, the company offers a diverse range of products tailored to meet the specific needs of its customers. Renowned for its commitment to excellence, Ceramic Fiber Blanket Density has become a trusted name in the industry, delivering exceptional insulation solutions that ensure maximum energy efficiency and cost-effectiveness.
At the heart of Ceramic Fiber Blanket Density's product line is their eponymous ceramic fiber blanket. Manufactured using advanced technology, this state-of-the-art insulation material boasts exceptional thermal insulation properties. Its unique density ensures superior resistance to heat, flame, and chemical corrosion, making it an ideal choice for high-temperature applications. Whether used in furnaces, kilns, or other industrial equipment, Ceramic Fiber Blanket Density's product provides unmatched thermal stability and protection.
One of the primary advantages of Ceramic Fiber Blanket Density's ceramic fiber blanket is its exceptional energy efficiency. By minimizing heat loss, this insulation material helps to reduce energy consumption, leading to significant cost savings for its users. Furthermore, the blanket's high-density composition guarantees outstanding thermal shock resistance, ensuring its longevity and reliability even under extreme temperature fluctuations. This robustness translates into reduced maintenance costs and increased equipment lifespan.
Ceramic Fiber Blanket Density goes beyond simply offering excellent insulation solutions. The company understands that every industry has unique requirements, and therefore, provides customization options to meet those specific needs. By collaborating closely with clients, their team of experts can develop tailor-made insulation solutions that maximize efficiency and performance. Such personalized approaches emphasize Ceramic Fiber Blanket Density's commitment to customer satisfaction and innovative problem-solving.
In addition to their ceramic fiber blanket, Ceramic Fiber Blanket Density expands their portfolio to include a wide range of complementary and supplementary insulation products. These include fire-resistant refractory bricks, insulation boards, and adhesive solutions, all designed to meet the diverse needs of their clientele. This comprehensive selection allows customers to source all their insulation requirements from a single, trusted provider, streamlining procurement and ensuring product compatibility.
To maintain the high standards it has set for itself, Ceramic Fiber Blanket Density places significant emphasis on quality control. Their production processes adhere to stringent international standards, guaranteeing the reliability and durability of their products. Stringent testing measures are implemented throughout the manufacturing process to ensure each product surpasses industry benchmarks and meets the performance expectations of their discerning customers.
Furthermore, Ceramic Fiber Blanket Density is committed to sustainability and environmental responsibility. Their insulation materials are free from harmful substances, making them safe to handle and install. The company actively seeks to reduce its carbon footprint by optimizing energy consumption during production and employing eco-friendly practices throughout its operations. Ceramic Fiber Blanket Density strives to provide insulation solutions that not only benefit their customers but also contribute to a greener and more sustainable future.
As a frontrunner in the industry, Ceramic Fiber Blanket Density consistently invests in research and development, aiming to foster continuous improvement and innovation. Through collaborations with industry experts and academic institutions, the company remains at the forefront of insulation technology advancements. By staying ahead of the curve, Ceramic Fiber Blanket Density ensures that its customers have access to the most cutting-edge insulation solutions available.
With its commitment to excellence, personalized approach, and dedication to innovation, Ceramic Fiber Blanket Density continues to revolutionize the insulation industry. By delivering products that offer superior thermal performance, exceptional energy efficiency, and unmatched durability, the company has earned the trust and confidence of its customers worldwide. As industries seek more efficient and sustainable solutions, Ceramic Fiber Blanket Density remains a trusted partner in providing insulation solutions that meet the highest standards of quality and performance.
Company News & Blog
Efficient Electric Furnace for Metal Melting - A Cost-Effective Solution
Electric Metal Melting Furnace Revolutionizes Industrial Metalworking Metalworking companies have long been dependent on utilizing furnaces to melt and mold metals into the required shapes. The traditional methods of using a furnace depend on fossil fuels that cause pollution and release harmful gases into the atmosphere. However, with the introduction of Electric Metal Melting Furnace, the metalworking industry can now obtain a cost-effective and environmentally friendly solution that will transform their business.The Electric Metal Melting Furnace is a state-of-the-art technological advancement that has revolutionized the traditional methods of metalworking in the industry. The furnace operates by utilizing electricity as the primary energy source, which ensures that there are no harmful emissions released into the atmosphere during the melting process. With the implementation of this technology, metalworking companies can now achieve environmentally sustainable practices while efficiently melting metals for their projects.This latest innovation has been introduced by leading industrial equipment and machinery manufacturing company, {company name}, which has been serving the metalworking industry for over a decade. The company has established a reputation for itself by providing innovative solutions that have transformed the industry. In line with this tradition, the Electric Metal Melting Furnace is another game-changer that is set to revitalize the metalworking industry.The Electric Metal Melting Furnace is a high-performance furnace that is designed to melt different types of metals with precision and accuracy. The furnace is equipped with a digital control system that makes it easy to operate and maintain. The system makes it possible for users to regulate temperature accurately, allowing the melting of specific metals based on their melting points. Some of the metals that can be melted using this furnace include iron, steel, copper, silver, and gold.The furnace is designed to melt metals at high temperatures, ensuring that the metal retains its original properties during the melting process. This feature is critical as it ensures that the metal's strength and integrity are maintained, making it suitable for industrial use. The furnace comes in various capacity ranges, making it ideal for both small and large-scale metalworking operations. This versatility makes Electric Metal Melting Furnace a preferred option for metalworking companies in various industries.Moreover, the Electric Metal Melting Furnace is not only cost-effective when compared to traditional furnaces, but it also saves time and energy. By using electricity as the primary energy source, the furnace reduces the operation cost, increases melting efficiency, and reduces the cooling time. Additionally, Electric Metal Melting Furnace does not need any preheating before the melting process, which saves users valuable production time.The environmental benefits of Electric Metal Melting Furnace cannot be overlooked. With the increasing concern for environmental conservation, many industries are looking for ways to reduce their carbon footprint. Electric Metal Melting Furnace provides an eco-friendly option for the metalworking industry by reducing harmful emissions such as carbon dioxide and sulfur dioxide.Another advantage of the Electric Metal Melting Furnace is that it minimizes waste production and reuses scrap metals. The melting process is efficient and precise, ensuring that there is minimal metal wastage during the melting process. Furthermore, the furnace can be used to recycle scrap metals, which reduces the need for raw materials in metalworking.The implementation of this technology serves as a positive step towards sustainable consumption and production practices. By using Electric Metal Melting Furnace, the metalworking industry can make significant contributions towards achieving the United Nations Sustainable Development Goals.In conclusion, the Electric Metal Melting Furnace is a significant technological advancement for the metalworking industry. It is a cost-effective, efficient, and environmentally friendly solution that has transformed the traditional methods of melting metals. The furnace can improve the quality of production in different industries, provide eco-friendly alternatives for metalworking, and reduce carbon footprints. With the Electric Metal Melting Furnace, the future of metalworking indeed looks bright.
Discover the Latest Innovation in Firebricks in South Africa
Firebricks in South Africa: Revolutionizing the Construction IndustrySouth Africa has long been known for its diverse landscape and rich mineral resources, but now the country is making waves in the construction industry with the introduction of innovative firebricks. These bricks are set to revolutionize the way buildings are designed and constructed, offering unparalleled durability and fire resistance.Firebricks South Africa, a pioneering company in the field, has been at the forefront of this groundbreaking technology. They have developed a range of firebricks that are not only aesthetically pleasing but also offer superior structural integrity when compared to traditional bricks. This is achieved by incorporating advanced materials and engineering techniques, ensuring that these firebricks are built to withstand the harshest conditions.One of the key advantages of using firebricks is their exceptional fire resistance. Traditional bricks can crack or crumble when exposed to high temperatures, compromising the structural integrity of buildings and posing a significant safety risk. However, firebricks have been specifically engineered to withstand intense heat without compromising their strength. This makes them ideal for use in fire-prone areas such as industrial complexes, warehouses, and even residential homes.In addition to their superior fire resistance, firebricks offer excellent insulation properties. This means that buildings constructed with these bricks can retain heat more effectively, helping to reduce energy consumption and lower heating costs. This is particularly important in South Africa, where extreme temperatures can be challenging to manage. The insulation provided by firebricks also ensures a more comfortable living or working environment, as the temperature remains stable and consistent.Furthermore, firebricks are incredibly durable, capable of withstanding the test of time. Traditional bricks are prone to erosion and degradation over time, especially when exposed to harsh weather conditions. Firebricks, on the other hand, are less susceptible to such wear and tear, preserving the structural integrity of buildings for decades to come. This makes them an excellent long-term investment for developers and homeowners alike.Firebricks South Africa offers a wide range of firebrick options to cater to various construction needs. From standard-sized bricks to customized shapes and sizes, they have a solution for every project. Their team of industry experts works closely with architects, engineers, and contractors to understand specific requirements and provide tailored solutions. This collaborative approach ensures that each project is executed seamlessly, meeting and exceeding client expectations.The company takes pride in its commitment to sustainability. Firebricks South Africa uses environmentally friendly manufacturing processes, minimizing waste generation, and reducing carbon emissions. By employing sustainable practices, they contribute to a greener future while providing high-quality construction materials.Firebricks South Africa has quickly gained recognition for its cutting-edge technology and exceptional customer service. Their growing client base includes major construction companies, architectural firms, and individual homeowners. The positive feedback and testimonials from satisfied clients further cement the company's reputation as a leader in the firebrick industry.As South Africa continues to grow and develop, the demand for innovative construction materials is on the rise. Firebricks, with their unparalleled fire resistance, insulation properties, and durability, are transforming the construction landscape. Firebricks South Africa remains at the forefront of this revolution, constantly pushing the boundaries of what is possible in the construction industry. With their commitment to quality, sustainability, and client satisfaction, they are well on their way to becoming a household name in the field.
Discover the Advantages of Refractory Clay Bricks for Enhanced Performance
Refractory Clay Bricks Prove to Be a Game-Changer for the Construction IndustryThe construction industry has seen significant growth in the past decade, with the need for new infrastructure and residential buildings on the rise. However, with this growth come challenges, and one of the most significant challenges faced by the industry is finding the right materials to withstand high temperatures and harsh conditions. Luckily, the development of refractory clay bricks has proven to be a game-changer.Refractory clay bricks are specially designed to withstand high temperatures and have a higher level of resistance to heat than standard bricks. They are used in kilns, furnaces, blast furnaces, and other high-temperature processing units. The construction industry has been quick to adopt this new technology, as it has significantly enhanced the durability and longevity of structures.One of the prominent companies in the industry that produces high-quality refractory clay bricks is located in China. Refractory clay bricks produced by this company are made of high-quality raw materials and have a high level of sintering strength. They are widely used in industries such as metallurgy, chemical engineering, building materials, and electric power.The manufacturing process of these refractory clay bricks is environmentally friendly, and the quality control process is rigorous. The company has invested in state-of-art-production lines, advanced testing equipment, and cutting-edge technology to ensure that their products meet international standards.The company offers a wide range of refractory clay bricks, including high-alumina bricks, fireclay bricks, silica bricks, magnesia bricks, and many more. These bricks are made to suit different industries and applications, making them versatile and adaptable.The high-alumina bricks have excellent heat resistance, making them suitable for lining furnace walls, roofs, and bottoms. The fireclay bricks are used in metallurgy, building materials, and machinery manufacturing industries. They have a high level of wear resistance, making them suitable for lining the walls of kilns and furnaces. Silica bricks are used in glass-making industries and have good thermal shock resistance. Magnesia bricks are used in metallurgy industries and have high thermal conductivity, excellent thermal shock resistance, and high refractoriness.The company has experienced significant growth over the years due to the quality of their products and their commitment to customer satisfaction. They have a team of experts who can offer technical support to their clients and provide solutions to their refractory-related problems. They also have a vast distribution network, ensuring that their products reach their clients in a timely and efficient manner.In conclusion, the development of refractory clay bricks has proven to be a game-changer for the construction industry. The high level of resistance to heat and other environmental factors has made these bricks a preferred choice for many industries. The company in China has distinguished themselves in this industry, and their commitment to quality and customer satisfaction has earned them a reputation as a leading producer of high-quality refractory clay bricks. With the growing demand for durable and high-performance materials in the construction and industrial sectors, the future looks bright for companies such as this.
Durable and Heat-Resistant Castable Refractory: A Comprehensive Analysis
Title: Leading Manufacturer Introduces Next-Generation Dense Castable Refractory for Enhanced PerformanceIntroduction:In a bid to revolutionize the refractory industry, a renowned manufacturer has introduced a groundbreaking dense castable refractory product. With a track record of innovative solutions and a commitment to pushing the boundaries of technological advancements, this manufacturer has solidified its position as an industry leader. Now, they have unveiled their latest product, which promises exceptional performance and durability for a wide range of industrial applications.A Breakthrough in Refractory Technology:Designed to withstand extreme temperatures, chemical attacks, and mechanical stress, the new dense castable refractory is poised to redefine the realm of heat-resistant materials. By incorporating cutting-edge technology and leveraging their extensive experience, this manufacturer has successfully developed a product that exhibits superior mechanical strength, thermal shock resistance, and excellent erosion resistance properties.Unmatched Performance:The exceptional performance of this refractory can be attributed to its unique composition, which consists of a carefully engineered blend of premium raw materials. This innovative formulation guarantees exceptional performance and durability, making it an ideal choice for applications such as steelmaking, petrochemical facilities, power generation, and cement kilns.Temperature Resistance:The new refractory is capable of withstanding temperatures exceeding 3,000°C, offering unparalleled protection in high-temperature environments. This remarkable resistance allows for extended operational life cycles, reducing downtime and maintenance costs for industrial facilities.Thermal Shock Resistance:One of the standout features of this refractory is its remarkable resistance to thermal shock. Traditional refractories often experience cracking and spalling when subjected to rapid temperature fluctuations. However, the advanced formulation of this dense castable refractory minimizes thermal stress and ensures extended service life, even in the most intense thermal environments.Erosion Resistance:The unique composition of this refractory ensures exceptional erosion resistance, enabling it to withstand chemical attacks from molten metals, slag, and other corrosive substances. This resistance significantly enhances the longevity of the refractory lining and reduces the need for frequent replacements.Versatile Application:The dense castable refractory can be customized to cater to various industrial needs, making it suitable for a wide range of applications. Its versatility allows for easy installation and use in multiple industries, including foundries, incineration plants, glass furnaces, and more.Sustainable Solution:Recognizing the global need for sustainable manufacturing practices, the manufacturer has prioritized environmental consciousness throughout their research and development process. The refractory formulation is designed to minimize emissions and reduce environmental impact, aligning with the company's commitment to sustainability.Commitment to Quality and Safety:In line with industry standards, the manufacturer adheres to rigorous quality control measures to ensure the highest level of product quality and safety. Their dense castable refractory undergoes comprehensive testing procedures, including thermal conductivity analysis, modulus of rupture tests, and chemical resistance evaluations, among others.Conclusion:With the introduction of their latest dense castable refractory, this leading manufacturer has cemented its position as an industry frontrunner. By combining cutting-edge technology with a commitment to sustainable manufacturing, they have developed a superior product that exhibits excellent temperature resistance, thermal shock resistance, and erosion resistance. With versatile applications across various industries, this refractory is set to transform the way high-temperature processes are conducted, ensuring enhanced performance and extended service life.
Exploring the Benefits of Ceramic Cloth Insulation for Enhanced Energy Efficiency
Ceramic Cloth Insulation Revolutionizing Heat Control in IndustriesInnovation and sustainable solutions have become increasingly important in today's industrial landscape. Industries are constantly seeking ways to enhance efficiency, reduce energy consumption, and mitigate environmental impacts. One company emerging as a frontrunner in this quest is {Ceramic Cloth Insulation}, whose cutting-edge product is revolutionizing heat control in various sectors.{Ceramic Cloth Insulation}, a global leader in thermal management solutions, has developed a highly advanced material that provides superior insulation capabilities. Designed to withstand extreme temperatures and harsh conditions, their product has garnered immense attention from industries ranging from aerospace to automotive manufacturing, and even energy production.The key to {Ceramic Cloth Insulation}'s success lies in its unique composition. Made from a blend of high-quality ceramic fibers and specialized fabrics, the insulation material possesses exceptional thermal resistance characteristics. This innovative technology enables industries to effectively control and manage heat, achieving significant operational efficiencies.With the ability to withstand temperatures of up to 1,800 degrees Celsius, {Ceramic Cloth Insulation} ensures the utmost safety for industries operating under extreme conditions. This breakthrough development not only enhances the longevity of equipment but also reduces maintenance costs, making it an attractive choice for companies across the board.One of the primary advantages of {Ceramic Cloth Insulation} is its versatility. The material's flexibility allows for easy handling and installation, making it ideal for a wide range of applications. Whether it's insulating pipes in chemical plants, lining furnaces in steel manufacturing, or protecting cables in the aerospace industry, this product proves to be a versatile solution for heat management needs.Moreover, this innovative insulation material acts as a barrier to prevent unnecessary heat transfer. By significantly reducing heat loss and maximizing thermal efficiency, {Ceramic Cloth Insulation} contributes to substantial energy savings for industrial plants. This not only lowers operational costs but also aligns with industries' growing focus on sustainable practices.The positive impact of {Ceramic Cloth Insulation} on the environment cannot be overlooked. By reducing energy consumption, industries using this insulation material are effectively lowering their carbon footprint. This aligns with global efforts to combat climate change and promote sustainability, making {Ceramic Cloth Insulation} an essential component of the transition towards greener industrial practices.To further cater to industries' diverse needs, {Ceramic Cloth Insulation} offers a range of customized solutions. Their team of experts collaborates closely with clients to understand specific requirements and provide tailored insulation solutions that maximize efficiency. This customer-centric approach has earned {Ceramic Cloth Insulation} a reputation for excellence and reliability.As demand for innovative thermal management solutions continues to grow, {Ceramic Cloth Insulation} remains committed to pushing the boundaries of technology. Through ongoing research and development, the company aims to further enhance the performance of their insulation material and expand its application in various industries.By leveraging their expertise in thermal management, {Ceramic Cloth Insulation} is not only transforming heat control practices but also contributing to industrial efficiency and sustainability. With their advanced insulation solutions, industries can maximize operational productivity while reducing energy consumption and minimizing environmental impacts.In conclusion, the innovative and adaptable nature of {Ceramic Cloth Insulation} has positioned the company as a leader in thermal management solutions. With their exceptional insulation material, industries can now effectively control heat, ensuring safety, efficiency, and sustainability across various sectors. As the demand for sustainable practices continues to increase, {Ceramic Cloth Insulation} remains at the forefront of technological advancements in the industry.
Discover the Promising Features of Cutting-Edge Cement Castable for Enhanced Construction Efficiency
Cement Castable: A Revolutionary Product for Modern Day IndustrialistsIn a world where innovation and productivity are essential to business success, modern-day industrialists are constantly looking for newer, more efficient ways to manufacture products. One such innovation that has proven immensely popular in recent times is Cement Castable. This revolutionary product has been designed to help industries achieve greater efficiency, speed, and accuracy in the manufacturing process.Cement Castable refers to a type of cement that can be poured like a liquid and then hardens into a solid form when it dries. The process of mixing cement and water and then letting it harden has been used in construction for centuries. However, in recent years, the technology has been developed to the extent that this method can be used for industrial purposes. One company that has taken the lead in the production of Cement Castable is {removed due to branding policy}.{company} is a leading supplier of Cement Castable and has made a name for itself in the market for producing top-quality products that meet the unique needs of its clients. The company has invested heavily in research and development to come up with new and innovative products that help its clients maximize their productivity. Cement Castable is one such product that has emerged from the company’s research and development efforts.The key benefit of Cement Castable is that it offers a superior alternative to traditional methods of manufacturing. The product allows for faster and more efficient production processes, which saves manufacturers both time and money. Additionally, Cement Castable can be molded into any shape or size, making it a highly versatile product. This is particularly useful for industries that require precision parts for their products.Another significant advantage of Cement Castable is its excellent durability and resistance to wear and tear. This means that machines and equipment made with this product tend to have a longer lifespan and require less maintenance. Furthermore, the product’s resistance to high temperatures and corrosive substances makes it ideal for industries that operate under extreme conditions.{company} takes pride in the high quality of its Cement Castable products. The company uses only the best raw materials, and its manufacturing processes are rigorously monitored to ensure that every product meets the highest standards of quality. Moreover, the company’s team of technicians and engineers are always on hand to offer technical support and guidance to clients, making the company a one-stop-shop for industrialists.In conclusion, Cement Castable is a game-changer for modern-day industrialists. The product offers a more efficient, versatile, and durable alternative to traditional manufacturing methods. At {company}, we take pride in our contribution to this innovation. Our Cement Castable products have proven to be reliable and of high quality, making us a trusted partner for industries around the world.
Different Types of Refractory Materials: A Complete Guide
Title: Advancements in Refractory Materials Transform IndustriesIntroduction:Refractory materials have been an integral part of various industries, providing crucial resistance to extreme temperatures and chemical reactions. These materials are used in applications such as furnaces, kilns, reactors, and incinerators, where they play a vital role in maintaining operational efficiency. Today, we explore the latest advancements in refractory technology and its impact on industries worldwide.Background:Refractory materials are designed to withstand high temperatures and harsh environments, while also possessing excellent resistance to thermal shock, corrosion, and abrasion. They are commonly categorized into three types: acidic, basic, and neutral refractories, each suited for specific applications. As industries continue to evolve, the demand for more advanced refractory solutions has grown significantly.Company Introduction:{Company Name}, a leading manufacturer and supplier of refractory materials, has been at the forefront of innovation in this industry for many years. With their expertise, extensive R&D capabilities, and commitment to quality, {Company Name} has played a pivotal role in driving technological advancements in refractories.Types of Refractory Materials:1. Acidic Refractories:Acidic refractories primarily consist of silica, alumina, and varying proportions of other oxides. These materials possess excellent resistance to acidic environments, making them ideal for industries such as petrochemicals, energy, and metallurgy. Erosion-resistant acidic refractories have become increasingly popular due to their ability to withstand aggressive chemicals and high temperatures.2. Basic Refractories:Basic refractories are typically composed of magnesia, dolomite, or chrome-magnesia. They exhibit exceptional resistance to basic slag and alkaline environments, which makes them suitable for applications in the steel, cement, and non-ferrous metal industries. The high refractoriness and low thermal conductivity of basic refractories contribute to enhanced energy efficiency and extended equipment lifespan.3. Neutral Refractories:Neutral refractories have a high alumina content and possess excellent resistance to both acidic and basic environments. These materials find wide application in industries such as glass-making, ceramics, and incinerators. Their versatility and durability make them an ideal choice for processes where varied chemical environments are present.Advancements in Refractory Technology:1. Increased Thermal Efficiency:{Company Name}, working in collaboration with research institutions, has developed refractory materials with improved thermal conductivity. These advancements allow for enhanced heat transfer efficiency, resulting in reduced energy consumption and lower production costs for industries utilizing high-temperature processes.2. Enhanced Chemical Resistance:To address the increasing demand for resistance to aggressive chemicals, {Company Name} has developed advanced erosion-resistant refractories. These innovative materials exhibit superior corrosion resistance, enabling industries to operate in highly corrosive environments without compromising performance or durability.3. Longer Lifespan and Reduced Downtime:Through continuous research and development, {Company Name} has created refractory materials with extended lifespans. This improvement significantly reduces downtime associated with maintenance, resulting in enhanced operational efficiency and cost savings for industries relying on refractory-lined equipment.Conclusion:The continuous advancements in refractory materials and technology, spearheaded by {Company Name}, are revolutionizing industries worldwide. With improved thermal efficiency, enhanced chemical resistance, and extended lifespan, these refractory solutions are addressing the ever-evolving needs of industries. By utilizing these latest advancements, businesses can optimize their operations, reduce costs, and ensure safer and more sustainable processes. The future of refractory materials holds promise for industries looking to achieve greater efficiency and productivity in their operations.
Enhancing Efficiency and Durability: The Essential Guide to Oil Burner Refractory
[Company Name] Launches Innovative and Efficient Oil Burner Refractory[date], [location] - [Company Name], a leading provider of industrial solutions, is proud to announce the launch of its latest innovation in oil burner refractory technology. This new product aims to revolutionize the industry by offering enhanced efficiency, durability, and sustainability.With a focus on delivering high-quality solutions that meet the demands of today's rapidly evolving market, [Company Name] has developed this groundbreaking oil burner refractory to address the needs of various industries such as oil and gas, petrochemical, and power generation.This newly developed refractory material boasts a range of unique features that set it apart from traditional alternatives. Its superior insulation properties ensure reduced heat loss and increased energy efficiency, resulting in significant cost savings for industrial operations. Additionally, the innovative material composition prolongs the refractory's service life, reducing maintenance costs and downtime.The advanced design of this new oil burner refractory also improves combustion efficiency, leading to reduced emissions of harmful pollutants such as carbon dioxide and nitrogen oxide. By enabling a cleaner burning process, [Company Name] aims to contribute to a greener and more sustainable future.Furthermore, [Company Name]'s oil burner refractory offers exceptional resistance to thermal shock and chemical corrosion. This resilience ensures long-term stability and consistent performance in even the most demanding environments. Additionally, the refractory's ease of installation and customization options allow for seamless integration into existing heating systems, minimizing disruptions during upgrades or replacements.Through years of research and development, [Company Name] has fine-tuned their oil burner refractory to align with both customer and industry expectations. The responsive customer support team, coupled with advanced technical guidance, ensures that clients receive tailored solutions to meet their specific requirements.Speaking about the launch of the oil burner refractory, [Company Name]'s CEO stated, "We are thrilled to introduce our latest innovation to the market. At [Company Name], we constantly strive to develop cutting-edge solutions that enhance operational efficiency while prioritizing sustainability. This new refractory material aligns perfectly with our ethos, offering our clients improved performance, reduced costs, and a lower environmental impact."As a renowned industry leader with a global presence, [Company Name] remains committed to continuously driving innovation and providing unrivaled solutions. With the launch of this advanced oil burner refractory, the company aims to solidify its position at the forefront of the industry, catering to the evolving needs of businesses worldwide.Founded [year], [Company Name] has built a solid reputation for delivering excellence across various industrial sectors. With a team of highly skilled professionals and a customer-centric approach, the company has become a trusted partner for businesses seeking superior solutions.The launch of this innovative oil burner refractory is set to reinforce [Company Name]'s position as an industry leader, while also making a positive impact on the environment. As industries strive for energy efficiency and sustainability, [Company Name] continues to play an instrumental role in supporting these goals by providing state-of-the-art solutions.As the global economy moves towards a more sustainable future, [Company Name] remains committed to driving progress and innovation in the industrial sector. With the launch of this new oil burner refractory, the company is poised to empower businesses worldwide with efficient and environmentally friendly solutions, positioning itself as a force to be reckoned with in the industry.
High-quality and Durable 3kg Crucible: Essential for Efficient Operations
Title: Leader in Industrial Materials Launches Advanced 3kg Crucible for Enhanced Manufacturing ProcessesIntroduction:As an industry leader in innovative materials and solutions, our company is proud to announce the launch of an advanced 3kg Crucible, specifically designed to revolutionize manufacturing processes. This new addition to our product portfolio represents our commitment to providing cutting-edge solutions that enhance productivity and efficiency in various industries.Crucible - The Backbone of Manufacturing:Crucibles are an essential component in several manufacturing processes, particularly in industries such as metallurgy, glass, ceramics, and materials science. Crucibles serve as vessels for high-temperature melting, refining, and other material transformation processes. The quality and design of a crucible play a pivotal role in determining the success and efficiency of these manufacturing operations.Innovation Unveiled: Introducing the State-of-the-Art 3kg Crucible:Our company's research and development team has invested extensive efforts into creating a state-of-the-art 3kg Crucible that sets new industry standards. This advanced crucible combines premium quality materials, cutting-edge technology, and precision engineering to deliver exceptional performance and durability.Key Features and Benefits:1. Enhanced Thermal Conductivity: The 3kg Crucible incorporates a proprietary blend of advanced materials that ensures optimal thermal conductivity. This feature allows for faster and more efficient heat transfer, significantly reducing melt times and overall manufacturing cycles.2. Extreme Temperature Resistance: The crucible boasts remarkable resistance to high temperatures, making it ideal for use in extreme heat environments. Its ability to withstand prolonged exposure to high temperatures not only enhances the manufacturing process but also ensures longevity, reducing the need for frequent replacements.3. Superior Chemical Stability: The crucible's composition guarantees excellent chemical stability, enabling it to withstand the corrosive effects of molten materials and aggressive chemicals often used in various manufacturing applications. This stability minimizes contamination risks and ensures consistent production quality.4. Design for Optimal Pouring: The 3kg Crucible has been meticulously engineered for improved pouring precision. Its innovative design eliminates the risk of spillage and allows for smooth, controlled pouring, maximizing operational safety and minimizing material wastage.5. Durable and Easy to Clean: Constructed with durability in mind, the crucible exhibits exceptional strength, preventing cracking, chipping, and premature wear. Additionally, its easy-to-clean surface simplifies maintenance, reducing downtime and improving overall efficiency.Quality Assurance and Industry Applications:Our company emphasizes stringent quality control measures to ensure each 3kg Crucible meets the highest standards of reliability and performance. Through extensive testing and continuous improvement, we are confident that our crucibles will exceed expectations even in the most demanding industrial applications.The new 3kg Crucible is anticipated to have a widespread impact across various sectors, such as foundries, laboratories, educational institutions, and product development centers. Its versatility and superior performance make it an indispensable tool for professionals engaged in alloy production, metal casting, research, and development.Conclusion:As a trusted leader in the production of industrial materials, our company's launch of the advanced 3kg Crucible reinforces our commitment to driving innovation and excellence in manufacturing processes. With its exceptional features and benefits, this new crucible stands to enhance productivity, reduce costs, and improve overall operational efficiency across multiple industries. We are confident that this groundbreaking product will revolutionize the way materials are transformed and contribute to the success of our customers' endeavors.
Advancements in Continuous Casting Furnace Technology for Enhanced Industrial Efficiency
[Company Introduction]{Insert Company Name} is a renowned leader in the manufacturing sector, known for its cutting-edge technologies and innovative solutions. With a global footprint and an extensive portfolio of products, the company has established its presence across various industries, including the metals industry.[News Content]Continuous Casting Furnace Revolutionizes the Metals Industry{City, Date} - In a bid to redefine the way metal products are manufactured, {Insert Company Name}, a pioneer in industrial technologies, has unveiled its latest breakthrough in the field of metal casting - the state-of-the-art Continuous Casting Furnace (CCF). This revolutionary furnace is set to transform the metals industry, offering unmatched efficiency, precision, and sustainability.Traditionally, metal casting processes have relied on batch production, which involved melting large quantities of metal to create discrete batches of products. However, the Continuous Casting Furnace, developed by {Insert Company Name}, eliminates the need for batch production, leading to significant improvements in productivity and product quality.The Continuous Casting Furnace incorporates advanced technologies that allow for the continuous production of metal products, such as steel billets, slabs, and blooms. This continuous process ensures a constant flow of output, minimizing downtime and maximizing overall throughput. With this innovative furnace, manufacturers can achieve higher production volumes, reducing lead times and meeting the ever-increasing demands of the market.One of the standout features of the Continuous Casting Furnace is its ability to enhance product quality and consistency. By maintaining a steady, controlled flow of molten metal, the furnace ensures uniformity in the casting process, resulting in products with fewer defects, improved dimensional accuracy, and enhanced surface finishes. This translates into superior end products that meet the stringent quality standards of various industries.In addition to its efficiency and product quality benefits, the Continuous Casting Furnace also offers remarkable sustainability advantages. The furnace utilizes advanced energy management systems that optimize energy consumption and decrease environmental impact. By streamlining the casting process, manufacturers can significantly reduce energy usage and minimize waste generated during production. This ensures a more sustainable approach to manufacturing, aligning with global efforts to reduce carbon emissions and promote eco-friendly practices.{Insert Company Name} has invested significant resources in research and development to bring the Continuous Casting Furnace to market. The company’s team of highly skilled engineers and metallurgical experts have collaborated to design a furnace that delivers exceptional performance across various industries, including automotive, construction, and manufacturing."The introduction of our Continuous Casting Furnace represents a major milestone in the metals industry. This cutting-edge technology will revolutionize the way metal products are manufactured, offering transformative benefits to our customers," said {Spokesperson Name}, {Job Title} at {Insert Company Name}.This breakthrough innovation is a testament to {Insert Company Name}'s commitment to pushing the boundaries of what is possible in industrial manufacturing. The company's dedication to research, development, and technological advancements has solidified its position as a global leader, continuously delivering solutions that address the evolving needs of industries worldwide.As the metals industry embraces the Continuous Casting Furnace, manufacturers can expect increased productivity, improved product quality, and a reduced environmental footprint. This game-changing technology is set to shape the future of metal casting, offering a more efficient, sustainable, and competitive approach to manufacturing.