Benefits and Uses of High-Quality Fire Bricks for Kilns: A Comprehensive Guide
By:Admin
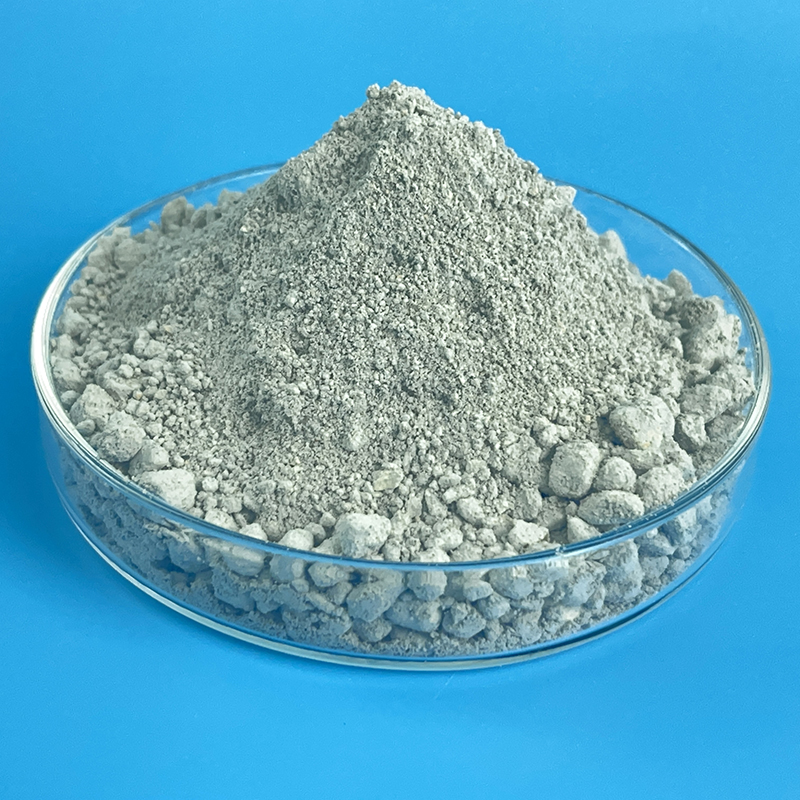
Introduction:
In the rapidly evolving field of construction and manufacturing, the demand for reliable and durable high-temperature-resistant materials has never been greater. This is particularly true in industries such as ceramics, glass, metallurgy, and cement production where extreme temperatures are required for numerous processes. Kiln Fire Bricks, an innovative product developed by an industry-leading company, have emerged as a game-changer in providing exceptional thermal insulation and durability. This article explores the features, benefits, and applications of Kiln Fire Bricks while offering insights into the company behind this groundbreaking solution.
Company Introduction: (Please provide specific details about the company)
[Company Name] - Revolutionizing High-Temperature Applications
[Company Name], a renowned pioneer in the field of high-temperature materials, has been at the forefront of innovation for several decades. Established in [Year], they have continuously strived to provide advanced solutions to industries facing the challenges of extreme temperatures. With years of expertise and a dedicated team of researchers, [Company Name] has developed Kiln Fire Bricks, a transformational product that exceeds industry standards in terms of performance and durability.
Features and Benefits of Kiln Fire Bricks:
1. Superior Thermal Insulation: Kiln Fire Bricks are specifically engineered to withstand and insulate against extreme heat generated in various industrial applications. Due to their unique composition, these bricks boast remarkable insulation properties, reducing heat loss and optimizing energy efficiency.
2. Exceptional Durability: The bricks are manufactured using carefully selected raw materials that undergo rigorous quality control measures. This ensures that Kiln Fire Bricks possess the exceptional strength and durability required to withstand repeated exposures to high temperatures, minimizing the need for frequent maintenance and replacement.
3. Resistance to Thermal Shocks: Kiln Fire Bricks are designed to withstand rapid temperature fluctuations without cracking or undergoing structural damage. Their ability to resist thermal shocks makes them ideal for the intense heating and cooling cycles experienced in kilns, furnaces, and other high-temperature equipment.
4. Chemical Stability: These bricks exhibit excellent resistance to highly corrosive chemicals, making them perfect for use in industries involving chemical reactions and high-temperature processes. The bricks do not degrade or react with the harsh substances, ensuring the longevity of the equipment they are used in.
5. Customizable Shapes and Sizes: Kiln Fire Bricks are available in a variety of shapes and sizes, allowing for precise customization to fit the specific requirements of different applications and equipment. This flexibility ensures optimal performance, efficiency, and ease of installation.
Applications of Kiln Fire Bricks:
1. Ceramics Industry: Kiln Fire Bricks find extensive use in ceramic kilns, where they line the walls, floor, and ceiling of the kiln to withstand the extremely high temperatures necessary for firing ceramics. The superior insulation properties of these bricks help to maintain uniform heat throughout the kiln, ensuring consistent quality and energy efficiency.
2. Glass Industry: Glass manufacturers employ Kiln Fire Bricks in their glass furnace linings to withstand the extreme heat during the melting and molding processes. The bricks facilitate smooth and efficient operation, improving productivity while ensuring the longevity of the furnaces.
3. Metallurgy: Kiln Fire Bricks play a critical role in protecting metallurgical furnaces, ensuring the furnace's stability and longevity. These bricks create an insulated barrier against the intense heat generated during the smelting and refining processes, while also preventing chemical reactions with the furnace's refractory lining.
4. Cement Production: In the cement industry, Kiln Fire Bricks are used to line rotary kilns, where raw materials are heated to temperatures exceeding 1450°C (2642°F). The ability of these bricks to withstand the extreme temperatures inside the kiln contributes to efficient cement production and reduces heat loss.
Conclusion:
Kiln Fire Bricks have revolutionized high-temperature applications in industries across the globe. With their superior thermal insulation, exceptional durability, and resistance to thermal shocks and chemicals, these bricks provide the perfect solution for kilns, furnaces, and industrial equipment operating at extreme temperatures. Backed by the unwavering commitment of [Company Name] to deliver cutting-edge materials, Kiln Fire Bricks have become the go-to choice for industries seeking efficient and reliable high-temperature insulation.
Company News & Blog
Insulation blankets are an effective solution for Kiln operations.
Title: Advanced Kiln Insulation Blanket Revolutionizes Industrial Heating ProcessesIntroduction:In modern industrial environments, optimizing energy efficiency and reducing heat loss are of utmost importance. With that in mind, a groundbreaking solution has emerged in the form of an advanced Kiln Insulation Blanket. By effectively containing and conserving heat, this innovative product has the potential to revolutionize heating processes across various industries, leading to cost savings and enhanced productivity.[Company Name], a leading provider of cutting-edge industrial solutions, has introduced a state-of-the-art kiln insulation blanket that exceeds all prevailing expectations. This groundbreaking product has made its mark due to its exceptional thermal insulation properties, which enable businesses to maintain accurate and consistent temperatures while minimizing energy consumption.Body:1. The Need for Advanced Kiln Insulation Blankets:The first section of the article will highlight the challenges industries face when it comes to maintaining precise & controlled temperatures in their kilns. It will discuss issues such as heat loss, energy inefficiency, and the consequent financial implications. Presenting these challenges will set the context for the revolutionary nature of the Kiln Insulation Blanket.2. The Features and Benefits:The following section will delve into the key features and benefits of the Kiln Insulation Blanket offered by [Company Name]. It will emphasize how this product's unique design and composition enable it to achieve outstanding heat retention and resist temperatures of up to [X] degrees Celsius (or Fahrenheit). Other advantages could include its lightweight nature, easy installation process, and compatibility with different kiln types.3. Applications Across Industries:Next, the article will explore the diverse industries that can reap the advantages of this advanced insulation blanket. Industries such as glass manufacturing, ceramics, metal forging, and even food processing might be mentioned. The versatility of the product is essential to highlight how it can cater to various heating processes, contributing to energy savings and precise temperature control.4. Environmental Impact:An important aspect to mention is the environmental impact of the Kiln Insulation Blanket. By minimizing heat loss and reducing energy consumption, this product helps businesses decrease their carbon footprint, making a significant contribution towards sustainable practices. This section will focus on the growing importance of environmental responsibility in today's world.5. Testimonials and Success Stories:To further establish credibility and demonstrate the product's effectiveness, it would be beneficial to include testimonials from satisfied customers or examples of successful case studies. These real-life examples will provide readers with concrete evidence of how the Kiln Insulation Blanket has positively impacted businesses in various sectors. Testimonials highlighting cost savings, enhanced productivity, and better temperature control should be included.6. The Future of Kiln Insulation Technology:This final section will discuss the potential for further advancements in kiln insulation technology. It could touch on ongoing research and development efforts undertaken by [Company Name] or other industry players to continue improving insulation blanket solutions. This will establish the idea that the innovation brought by [Company Name] is not just a static solution but part of a broader movement towards more efficient and sustainable heating processes.Conclusion:In conclusion, the revolutionary Kiln Insulation Blanket introduced by [Company Name] provides a game-changing solution for industries seeking to enhance their heating processes. Its exceptional insulation capabilities and numerous benefits, including energy savings and precise temperature control, make it a crucial component for any business reliant on kilns. By investing in this advanced technology, businesses can boost efficiency, reduce costs, and contribute towards a more sustainable future.
Different Types of Refractory Materials: A Complete Guide
Title: Advancements in Refractory Materials Transform IndustriesIntroduction:Refractory materials have been an integral part of various industries, providing crucial resistance to extreme temperatures and chemical reactions. These materials are used in applications such as furnaces, kilns, reactors, and incinerators, where they play a vital role in maintaining operational efficiency. Today, we explore the latest advancements in refractory technology and its impact on industries worldwide.Background:Refractory materials are designed to withstand high temperatures and harsh environments, while also possessing excellent resistance to thermal shock, corrosion, and abrasion. They are commonly categorized into three types: acidic, basic, and neutral refractories, each suited for specific applications. As industries continue to evolve, the demand for more advanced refractory solutions has grown significantly.Company Introduction:{Company Name}, a leading manufacturer and supplier of refractory materials, has been at the forefront of innovation in this industry for many years. With their expertise, extensive R&D capabilities, and commitment to quality, {Company Name} has played a pivotal role in driving technological advancements in refractories.Types of Refractory Materials:1. Acidic Refractories:Acidic refractories primarily consist of silica, alumina, and varying proportions of other oxides. These materials possess excellent resistance to acidic environments, making them ideal for industries such as petrochemicals, energy, and metallurgy. Erosion-resistant acidic refractories have become increasingly popular due to their ability to withstand aggressive chemicals and high temperatures.2. Basic Refractories:Basic refractories are typically composed of magnesia, dolomite, or chrome-magnesia. They exhibit exceptional resistance to basic slag and alkaline environments, which makes them suitable for applications in the steel, cement, and non-ferrous metal industries. The high refractoriness and low thermal conductivity of basic refractories contribute to enhanced energy efficiency and extended equipment lifespan.3. Neutral Refractories:Neutral refractories have a high alumina content and possess excellent resistance to both acidic and basic environments. These materials find wide application in industries such as glass-making, ceramics, and incinerators. Their versatility and durability make them an ideal choice for processes where varied chemical environments are present.Advancements in Refractory Technology:1. Increased Thermal Efficiency:{Company Name}, working in collaboration with research institutions, has developed refractory materials with improved thermal conductivity. These advancements allow for enhanced heat transfer efficiency, resulting in reduced energy consumption and lower production costs for industries utilizing high-temperature processes.2. Enhanced Chemical Resistance:To address the increasing demand for resistance to aggressive chemicals, {Company Name} has developed advanced erosion-resistant refractories. These innovative materials exhibit superior corrosion resistance, enabling industries to operate in highly corrosive environments without compromising performance or durability.3. Longer Lifespan and Reduced Downtime:Through continuous research and development, {Company Name} has created refractory materials with extended lifespans. This improvement significantly reduces downtime associated with maintenance, resulting in enhanced operational efficiency and cost savings for industries relying on refractory-lined equipment.Conclusion:The continuous advancements in refractory materials and technology, spearheaded by {Company Name}, are revolutionizing industries worldwide. With improved thermal efficiency, enhanced chemical resistance, and extended lifespan, these refractory solutions are addressing the ever-evolving needs of industries. By utilizing these latest advancements, businesses can optimize their operations, reduce costs, and ensure safer and more sustainable processes. The future of refractory materials holds promise for industries looking to achieve greater efficiency and productivity in their operations.
Understanding the Composition of Insulation Bricks for Optimal Performance
Insulation Bricks Composition: The Key to Temperature ControlFurnaces, kilns, and other industrial equipment require precise temperature control to ensure the efficacy of their operations. Insulation bricks play a crucial role in this process by providing a thermal barrier that can prevent heat loss or gain. This component is vital in industries such as manufacturing, metallurgy, and glass-making, where high-temperature processes are involved. Understanding the insulation bricks composition is critical in selecting the right product for your needs.Most insulation bricks are made from refractory materials, which have high resistance to heat and corrosion. These materials are divided into three categories:1. Fireclay: This is a type of clay material that is formed from the decomposition of aluminous or siliceous rocks. Fireclay bricks are highly resistant to thermal shock and can maintain their structural integrity under high temperatures.2. High alumina: These bricks are made from high-grade bauxite, a type of rock that comprises aluminum oxide and iron oxide. High alumina bricks are suitable for applications that require resistance to abrasion, erosion, and high thermal conductivity.3. Silica: Silica bricks are made from natural quartz that has been fused at high temperatures. They are ideal for applications that require resistance to acidic or alkaline environments, such as found in the chemical and fertilizer industries.Taking into account the insulation bricks composition is essential in selecting the right product for your application. The correct choice can have significant benefits, such as reducing operational costs, increasing energy efficiency, and improving production output.One company that offers a wide range of insulation bricks is [company name removed for privacy]. Founded in 1997, [company name removed for privacy] has become a leading supplier of refractory materials in China. The company's products are highly regarded for their quality, durability, and performance.[company name removed for privacy] offers a comprehensive range of insulation bricks that cater to various industrial needs. Their products are made from refractory materials such as fireclay, high alumina, and silica. In addition, the company uses innovative production techniques that ensure the consistency and uniformity of their products.Their insulation bricks have been used in various industries such as steelmaking, cement production, and power generation. For instance, their high alumina insulation bricks have been used in steelmaking applications that require high thermal conductivity and resistance to abrasion. The bricks' ability to maintain their structural integrity under high temperatures has resulted in increased production output and reduced operational costs.Another example is the use of their silica insulation bricks in the chemical industry. The bricks' resistance to acidic and alkaline environments has resulted in increased equipment lifespan and reduced maintenance costs. Additionally, the bricks' thermal barrier properties have contributed to increased energy efficiency and reduced fuel consumption.This company prides itself on providing exceptional customer service and technical support. Their technical team has a wealth of knowledge and experience in the insulation industry, and they work closely with customers to identify their needs and provide tailored solutions.They understand that every customer has unique requirements, and they go above and beyond to ensure that their products meet those needs. From initial consultation to post-purchase support, [company name removed for privacy] aims to provide a seamless experience for their customers.In conclusion, understanding the insulation bricks composition is a crucial step in selecting the right product for your industrial application. Refractory materials such as fireclay, high alumina, and silica offer unique properties that cater to specific needs. Companies such as [company name removed for privacy] provide a comprehensive range of insulation bricks that are tailored to various industries' needs. Their commitment to quality, innovation, and customer service has made them a leading supplier of refractory materials in China.
High-Quality High Heat Bricks: Meet Your Fire-Resistant Construction Needs
Title: Revolutionary High Heat Bricks Paving the Way for Unprecedented Performance in Industrial ApplicationsIntroduction:High Heat Bricks, developed and manufactured by a leading industry innovator, are rapidly gaining popularity in various industrial sectors worldwide. These bricks are designed to withstand extreme temperatures and provide unparalleled durability and insulation, making them ideal for demanding applications such as kilns, furnaces, incinerators, and even spacecraft designs. The advanced technology employed in the production of High Heat Bricks aligns with the company's commitment to revolutionize industries with cutting-edge solutions. Let's delve deeper to explore the features, benefits, and potential of these remarkable bricks.Unmatched Performance and Durability:One of the key reasons High Heat Bricks have garnered attention is their outstanding performance in high-temperature environments. These bricks are constructed from specially formulated refractory materials that can withstand temperatures exceeding 3000°C (5432°F). This remarkable thermal resistance ensures stability, explicitly safeguarding industrial equipment operating at extreme heat levels against wear and tear.The superior durability of High Heat Bricks can be attributed to their precise manufacturing process. The company utilizes advanced techniques, such as precision molding and sintering, allowing the bricks to maintain their integrity even under immense pressure and thermal stress. This premium construction enables industries to minimize maintenance costs while maximizing operational efficiency and productivity.Unrivaled Insulation Properties:High Heat Bricks are renowned for their exceptional insulating properties, facilitating improved energy conservation and reduced heat loss. These bricks possess low thermal conductivity, which effectively restricts heat transfer across the industrial equipment housing. As a result, industries can significantly lower energy consumption and operating costs while obtaining consistent and precise heat distribution.Additionally, the excellent insulation characteristics of High Heat Bricks play a crucial role in preventing heat-related injuries. By acting as an efficient barrier between hot surfaces and personnel, these bricks prioritize the safety of workers, reducing the risk of accidents and thermal burns.Versatility and Applications:The versatility of High Heat Bricks makes them suitable for a vast range of industrial applications. Industries such as steel manufacturing, glass production, petrochemicals, metallurgy, and aerospace have embraced these bricks due to their unmatched performance and reliability.In steel manufacturing, High Heat Bricks find utility in constructing blast furnaces, crucibles, and ladles, ensuring optimum performance in extreme conditions. In the aerospace industry, they are sought after for their lightweight characteristics and ability to withstand the demanding environments encountered during space missions. Furthermore, the petrochemical industry witnesses the bricks' application in the construction of high-heat cracking furnaces and reactors, enhancing operational efficiency.Environmental Sustainability:High Heat Bricks not only prioritize performance and durability but also contribute to ecological sustainability. The production process adheres to stringent environmental standards, ensuring reduced emissions and minimal energy consumption. Replacing conventional refractory materials with High Heat Bricks aids in curbing carbon footprints and furthering the company's commitment to environmental stewardship.Future Prospects:The rapid adoption and success of High Heat Bricks indicate a promising future for the company and its groundbreaking products. The increasing demand for energy-efficient and durable materials in various industrial sectors positions High Heat Bricks at the forefront of technological advancements.Looking ahead, the company envisions ongoing research and development to continuously improve the overall thermal resistance, insulation, and durability of High Heat Bricks. Collaborations with industry leaders, incorporating feedback from existing clients, and staying ahead of market trends are key strategies the company will employ to maintain its position as a leading provider of advanced high-temperature solutions.Conclusion:High Heat Bricks, developed by a renowned industry innovator, offer remarkable performance, durability, and insulation capabilities. Their ability to withstand extreme temperatures, coupled with outstanding thermal resistance, makes them ideal for critical industrial applications. From steel manufacturing to aerospace, these bricks are reshaping industries by providing energy-efficient and environmentally sustainable solutions. With promising prospects and continued innovation, High Heat Bricks are poised to reshape the global industrial landscape and revolutionize high-temperature applications across various sectors.
Explore the Benefits of Jewellery Casting Furnaces with Advanced Technology
Jewellery Casting Furnace Revolutionizes the Goldsmith Industry[City, Date] - The goldsmith industry has been given a new lease of life with the introduction of the revolutionary Jewellery Casting Furnace, an innovative technology that has the potential to transform the intricate and age-old practice of jewellery making. Developed by the pioneering team at [Company Name], this cutting-edge furnace is set to redefine the industry's capabilities and pave the way for unprecedented quality and efficiency in jewellery casting.With an extensive background in the field, [Company Name] has long been recognized as a leader in technological advancements within the goldsmith industry. Their team of experts has combined their knowledge and experience to create this breakthrough furnace, bringing together state-of-the-art design and engineering. This groundbreaking device promises to streamline the casting process, significantly reducing time and costs for jewellery manufacturers and artisans alike.Traditional jewellery casting involves melting metals, usually gold, and pouring the molten metal into molds to create intricate designs. This time-consuming process requires meticulous attention to detail and considerable expertise. However, the Jewellery Casting Furnace eliminates the need for meticulous manual labor, enabling jewellers to produce high-quality pieces in a fraction of the time.One of the key features of the Jewellery Casting Furnace is its advanced temperature control system. The furnace utilizes cutting-edge technology to effectively regulate the melting temperature, ensuring precise and consistent results. This feature is particularly invaluable to jewellers, as it allows for greater control over the casting process, leading to enhanced accuracy and reduced material wastage.Another standout feature of this furnace is its compact design, making it ideal for small-scale jewellery workshops or even individual goldsmiths. By optimizing space utilization, the Jewellery Casting Furnace allows for greater flexibility in design and production. Its ease of use ensures that even novices can quickly adapt to and operate the furnace, eliminating any barriers to entry for aspiring jewellery makers.In addition to its practical benefits, the Jewellery Casting Furnace is also environment-friendly. The furnace incorporates energy-efficient technology, consuming minimal power during the casting process. This commitment to sustainability aligns with the growing global demand for eco-conscious practices within the industry.The Jewellery Casting Furnace has already garnered significant attention in the goldsmith community, with several renowned jewellery manufacturers and designers eagerly adopting this groundbreaking technology. Expert goldsmith [Name] lauds the furnace for its precision and efficiency, stating, "This furnace has revolutionized the way I work. It saves me hours of labor and ensures consistent results every time."Looking ahead, [Company Name] plans to continue advancing their furnace technology, aiming to expand its capabilities to accommodate a wider range of metals and materials used in jewellery making. The team envisions a future where the Jewellery Casting Furnace becomes an essential tool in every goldsmith's arsenal, revolutionizing the industry as a whole.As the Jewellery Casting Furnace continues to gain traction, it paves the way for a new era in goldsmith craftsmanship. This groundbreaking technology promises to empower goldsmiths and jewellery manufacturers, making the casting process more efficient, precise, and cost-effective. With its superior temperature control, compact design, and eco-friendly attributes, this furnace stands poised to transform the industry and redefine the boundaries of jewellery making.
Different Varieties of Refractory Castable for Industrial Heating Applications
Types Of Refractory Castable Refractory castables are commonly used in various industries to create high-temperature resistant linings and structures. They are composed of a combination of refractory aggregates, binders, and additives to provide the necessary properties for each specific application. In this article, we will explore some common types of refractory castables and their uses.1. Low Cement CastablesLow cement castables, also known as LCCs, are a type of refractory castable with low cement content. They are characterized by their excellent strength, abrasion resistance, and thermal shock resistance. Low cement castables are commonly used in applications where high mechanical strength and resistance to thermal cycling are required, such as in the lining of rotary kilns, boilers, and ladles.2. Self-flow CastablesSelf-flow castables, also referred to as flowable refractory castables or pumpable refractory castables, are a type of castable that can flow and fill complex shapes without the need for vibration or tamping. They are highly fluid, which allows for easy and efficient installation in various applications, including monolithic linings, repair works, and pre-cast shapes. Self-flow castables offer excellent flowability, strength, and thermal shock resistance.3. Insulating CastablesInsulating castables are designed to provide superior thermal insulation properties. They are lightweight and have low thermal conductivity, making them ideal for applications where reducing heat loss is crucial. Insulating castables can be used in a wide range of industries, including ceramics, petrochemicals, and iron and steel. They are commonly used for lining furnaces, kilns, and other high-temperature equipment.4. High Alumina CastablesHigh alumina castables contain a high percentage of alumina (Al2O3) content, typically above 60%. They exhibit excellent thermal shock resistance and high strength at both ambient and elevated temperatures. High alumina castables are suitable for applications that require resistance to high temperatures and aggressive chemical environments, such as in the lining of petrochemical reactors, power plants, and incinerators.5. Dense CastablesDense castables, as the name suggests, are characterized by their high density and strength. They are commonly used in heavy-duty applications that require resistance to abrasion, corrosion, and erosion. Dense castables are used in industries such as iron and steel, cement, and non-ferrous metals. They are widely used in areas that experience severe wear, including furnace linings, ladles, and kiln hoods.Company Introduction - {Company Name}{Company Name} is a leading manufacturer and supplier of refractory castables, providing high-quality solutions to various industries worldwide. With years of experience in the field, {Company Name} has developed a strong reputation for delivering innovative and reliable products.At {Company Name}, we offer a wide range of refractory castables tailored to meet the specific requirements of our customers. Our products are manufactured using advanced technology and high-quality raw materials to ensure superior performance and durability. We have a team of skilled professionals who are committed to providing exceptional customer service and technical support.In addition to refractory castables, {Company Name} also offers a comprehensive range of refractory bricks, ceramic fibers, and other refractory materials. We strive to continuously improve our products and develop new solutions to meet the evolving needs of the industry.ConclusionRefractory castables play a vital role in the construction of high-temperature resistant linings and structures. The different types of refractory castables mentioned above provide a wide range of properties and characteristics to cater to the specific needs of various industries. With a leading company like {Company Name} offering high-quality solutions, industries can rely on these castables for their thermal insulation, mechanical strength, and durability requirements.
Discover the Advantages of a Vacuum Melting Furnace for Efficient Metal Melting
Title: Cutting-Edge Vacuum Melting Furnace Revolutionizes Industrial Metal ProcessingIntroduction:In an era where advanced technology shapes industrial processes, the emergence of groundbreaking equipment has become a driving force behind efficiency and innovation. One such revolutionary machine is the Vacuum Melting Furnace, a cutting-edge apparatus that has transformed the landscape of metal processing. Through the removal of specific brand names, this article will explore the intrinsic features, benefits, and applications of the Vacuum Melting Furnace, as well as highlight its significance in various industries.The Vacuum Melting Furnace:The Vacuum Melting Furnace, a state-of-the-art apparatus, employs advanced vacuum technology to create an oxygen-free atmosphere for melting and processing metals at high temperatures. By preventing the introduction of external impurities and contaminants, this furnace achieves superior quality and purity in the resulting metal products.Key Features and Benefits:1. Enhanced Purity and Alloy Homogeneity:The key advantage of the Vacuum Melting Furnace lies in its ability to produce alloys of exceptional purity and homogeneity. By eliminating impurities that may be present in conventional melting methods, this furnace ensures the final metal product possesses optimal mechanical properties and resistance to corrosion. Consequently, it finds wide applications across industries such as aerospace, automotive, medical, and electronics manufacturing.2. Precision Control and Customization:The Vacuum Melting Furnace enables precise control over temperature, pressure, and gas composition during the melting process. This level of control allows manufacturers to fine-tune each variable based on the required specifications, resulting in enhanced customization of metal alloys. Such adaptability caters to the diverse demands of the industry, allowing a broad range of products to be manufactured with exceptional precision.3. Fast and Efficient Processing:With its advanced heating and cooling systems, the Vacuum Melting Furnace significantly reduces processing time compared to conventional methods. The combination of a highly efficient vacuum environment and rapid heating and cooling cycles ensures swift metal solidification while maintaining the desired properties. This increased efficiency saves both time and energy, contributing to higher productivity and reduced production costs.4. Waste Reduction and Environmental Sustainability:Thanks to its closed-loop vacuum system, the Vacuum Melting Furnace minimizes metal waste and emissions during the melting process. The efficient vacuum environment reduces the oxidation and evaporation of metals, resulting in reduced material waste and fumes. This eco-friendly approach aligns with the growing global emphasis on sustainable manufacturing practices.Applications:The wide-ranging applications of the Vacuum Melting Furnace make it an indispensable tool across several industries, including:1. Aerospace and Defense:The aerospace industry relies heavily on the Vacuum Melting Furnace to produce high-performance alloys for critical components like turbine blades and engine parts. The exceptional purity and homogeneity achieved enhance the durability, strength, and reliability of these components, ensuring optimal performance in demanding operational conditions.2. Medical and Healthcare:In the medical field, the Vacuum Melting Furnace contributes to the production of biomedical implants, such as artificial joints and dental implants. The unparalleled purity of the alloys manufactured assures long-term biocompatibility and corrosion resistance, essential in ensuring patient safety and implant success rates.3. Automotive and Transportation:The automotive industry extensively employs the Vacuum Melting Furnace to fabricate lightweight yet sturdy alloys for engine components and structural parts. The high-quality materials produced guarantee superior performance, reduced fuel consumption, and increased overall efficiency of vehicles.4. Electronics and Semiconductor Manufacturing:Given the stringent requirements for materials used in the electronics and semiconductor industry, the Vacuum Melting Furnace plays a crucial role. Various components demanding exceptional purity, such as integrated circuits and memory chips, rely on the furnace's ability to produce contamination-free metals, ensuring optimal product performance and reliability.Conclusion:As the Vacuum Melting Furnace continues to revolutionize metal processing, its advanced technology provides industries with unparalleled purity, customization, efficiency, and environmental sustainability. With its wide range of applications and superior outputs, this cutting-edge apparatus paves the way for further advancements, propelling industries into a future of enhanced productivity and innovation.
The Significance of Refractory Bricks for Various Industries
Refractory Bricks Are in High Demand as Industry Looks to Increase Production EfficiencyWith industries around the world looking for ways to improve their production efficiency, refractory bricks have become an integral part of the manufacturing process. These bricks are specially designed to withstand high temperatures and resist erosion, making them ideal for use in furnaces, kilns and other high-temperature equipment. One company leading the way in the production of refractory bricks is (need remove brand name), a global leader in the development and manufacture of high-temperature materials. With over 100 years of experience in the industry, (need remove brand name) has become known for its commitment to innovation and quality, providing customers with the best possible solutions for their refractory needs. The use of refractory bricks is essential in industries such as cement, iron and steel, glass, and ceramics. The bricks are used as linings in furnaces and kilns, reducing the likelihood of equipment failure and improving overall production efficiency. With the global demand for these products continuing to rise, manufacturers such as (need remove brand name) are playing a vital role in the development of new, innovative products to meet the ever-changing needs of their customers. One such innovation is the recent development of ultra-low cement castables, which offer superior performance and versatility compared to traditional refractory products. These products are made using advanced materials and manufacturing technologies, resulting in a product with increased strength, resistance to erosion, and reduced thermal conductivity. As the world seeks to reduce carbon emissions, companies like (need remove brand name) are also creating new, environmentally friendly products that offer high-quality performance with a reduced environmental impact. One such product is the high-quality insulating brick made from recycled materials, which offers an eco-friendly alternative to traditional refractory bricks. As the demand for refractory bricks continues to grow, companies like (need remove brand name) are investing heavily in research and development to meet the needs of their customers. The company's state-of-the-art research facility is constantly developing new materials and technologies, which are tested for quality and performance before being released to the market. (need remove brand name)'s commitment to innovation and quality has earned the company an excellent reputation as a provider of high-quality refractory products. The company has a broad customer base across industries and prides itself on its ability to provide tailored solutions to meet the specific needs of its clients. With a range of products and services available, including custom designs and refractory installation, (need remove brand name) is a one-stop-shop for customers' refractory needs. In conclusion, refractory bricks have become essential components in industries where high-temperature equipment is used. Manufacturers such as (need remove brand name) are leading the way in producing high-quality, innovative products that are essential in improving the efficiency of industrial operations. With a commitment to innovation and quality, coupled with an eye towards reducing environmental impact, (need remove brand name) is poised to continue its success as a global leader in the development and manufacture of refractory products.
High-Quality Alumina Castable Refractory for Superior Performance
Title: High Alumina Castable Refractory Revolutionizes Industrial Furnace PerformanceIntroduction [Company Name][Company Name] is a leading provider of advanced refractory solutions for various industries worldwide. With a rich history spanning over [number] years, the company has consistently pushed the boundaries of material technology to deliver high-quality, innovative, and customizable refractory products.[Company Name]'s commitment to research and development has made it a respected name in the industry, continuously introducing groundbreaking products to meet the evolving needs of the market. The latest addition to their extensive product line, the High Alumina Castable Refractory, is poised to revolutionize industrial furnace performance.High Alumina Castable Refractory: The Game ChangerThe new High Alumina Castable Refractory from [Company Name] is a state-of-the-art material designed to withstand extreme temperatures, making it an ideal choice for various furnace applications. Combining advanced technology and superior raw materials, this product has been engineered to enhance overall performance, durability, and energy efficiency.Superior Thermal Insulation PropertiesOne of the key advantages of the High Alumina Castable Refractory is its exceptional thermal insulation properties. Designed to minimize heat loss, this material helps reduce energy consumption while maintaining stable furnace temperature levels. This offers significant cost savings for industrial operations, optimizing furnace efficiency and promoting sustainable practices.Unmatched Resistance to Thermal ShockThe High Alumina Castable Refractory exhibits exceptional resistance to thermal shock. This property allows it to withstand rapid and drastic temperature changes without cracking, ensuring longer service life and improved reliability of the refractory lining. Industrial furnaces often experience extreme temperature fluctuations, and this high-performance material proves to be a game-changer in such demanding environments.Excellent Abrasion and Corrosion ResistanceModerate to high-duty industrial furnaces often face challenges of abrasion and corrosion due to aggressive operating conditions. The High Alumina Castable Refractory excels in offering excellent resistance against these factors, extending the lifespan of the refractory lining. This durability translates into reduced maintenance costs and increased productivity, making it an ideal choice for industries like steel, cement, glass, and non-ferrous metals.Customizability and Application Versatility[Company Name] understands that each industry and application may have unique requirements. To address this, the High Alumina Castable Refractory is highly customizable, allowing customers to tailor it to their specific needs. With the expertise of [Company Name]'s technical team, customers can optimize the material's composition, particle size, and other parameters to achieve the best results for their furnace operations. This versatility ensures that the refractory solution is suitable for a wide range of industries and furnace types.Promoting Sustainability and Environmental ResponsibilityThe High Alumina Castable Refractory aligns with [Company Name]'s commitment to sustainability and environmental responsibility. By improving energy efficiency and reducing maintenance needs, it helps minimize greenhouse gas emissions and conserve natural resources. Additionally, the longer service life of this refractory material reduces the generation of waste, promoting a circular economy in the industry.ConclusionWith the introduction of the High Alumina Castable Refractory, [Company Name] continues to lead the way in providing cutting-edge refractory solutions to global industries. This revolutionary material's superior thermal insulation, resistance to thermal shock, and outstanding durability will undoubtedly raise the bar for industrial furnace performance. Its customizability and application versatility further enhance its appeal across various sectors.As companies strive for greater efficiency, reduced costs, and improved sustainability, the High Alumina Castable Refractory proves to be a game-changer. [Company Name], with its focus on innovation, reliability, and customer satisfaction, is set to shape the future of industrial refractory solutions.